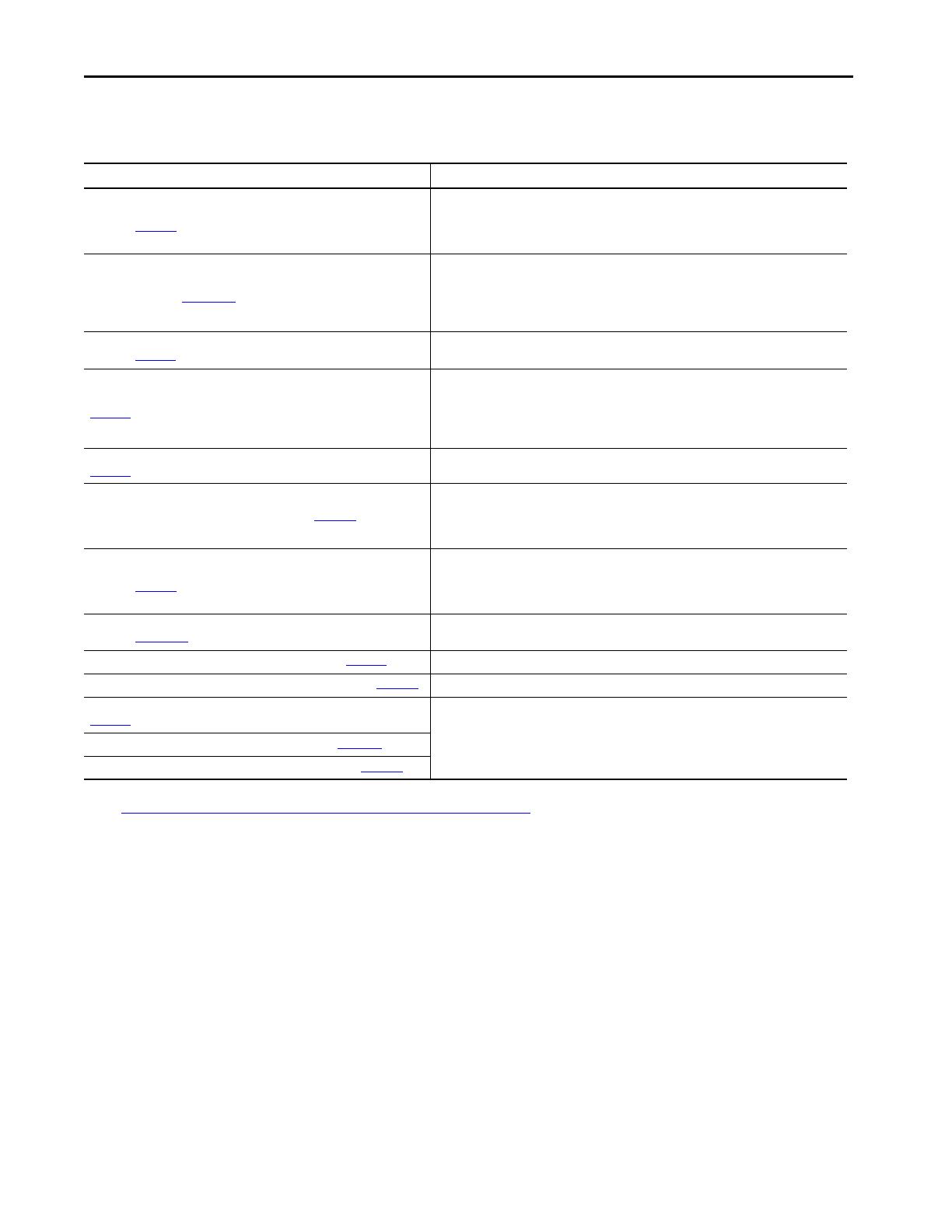
Rockwell Automation Publication 750-IN017B-EN-P - June 2018 13
PowerFlex 750-Series Service Cart Frames 8…10 Conversion Kit
Additional Resources
These documents contain additional information concerning related products from Rockwell Automation.
Go to: http://www.rockwellautomation.com/global/literature-library/overview.page
to view or download publications. To order paper copies of
technical documentation, contact your local Allen-Bradley distributor or Rockwell Automation sales representative.
Resource Description
PowerFlex 750-Series Products with TotalFORCE Control Hardware Service Manual,
publication 750-TG100
Provides detailed information on:
• Preventive maintenance
• Component testing
• Hardware replacement procedures
Drives in Common Bus Configurations with PowerFlex 755TM Bus Supplies Application
Techniques, publication DRIVES-AT005
Provides basic information to properly wire and ground the following products in common bus
applications:
• PowerFlex 755TM drive system for common bus solutions
• PowerFlex 750-Series AC and DC input drives
• Kinetix 5700 servo drives
PowerFlex 750-Series Service Cart and DCPC Module Lift Installation Instructions,
publication 750-IN105
Provides instructions to setup and use the PowerFlex 750-Series Service Cart and DCPC Lift. Includes spare
parts for the service cart and for the PowerFlex 750-Series frame 8…10 module conversion kit.
PowerFlex 755TM DC Precharge Modules Unpacking and Lifting Instructions, publication
750-IN103
These publications provide detailed information on:
• Component weights
• Precautions and recommendations
• Hardware attachment points
• Lifting the component out of the packaging
PowerFlex 755TM Power and Filter Module Storage Hardware Instructions, publication
750-IN106
Provides detailed installation and usage instructions for this hardware accessory
PowerFlex 750-Series AC Drives Technical Data, publication 750-TD001
Provides detailed information on:
• Drive specifications
• Option specifications
• Fuse and circuit breaker ratings
PowerFlex 750-Series AC Drives Hardware Service Manual – Frame 8 and Larger,
publication 750-TG001
Provides detailed information on:
• Preventive maintenance
• Component testing
• Hardware replacement procedures
Wiring and Grounding Guidelines for Pulse-width Modulated (PWM) AC Drives,
publication DRIVES-IN001
Provides basic information to properly wire and ground PWM AC drives.
PowerFlex 750-Series AC Drive Installation Instructions, publication 750-IN001
Provides information to install the Safe Speed Monitor option module in PowerFlex 750-Series drives
PowerFlex 750-Series Service Cart and DCPC Lift Renewal Parts, publication 750-PC106 Provides information to install the spare parts to the PowerFlex 750-Series Service Cart.
PowerFlex 750-Series Products with TotalFORCE Control Installation Instructions,
750-IN100
The installation of programming, and technical data of PowerFlex 750-Series products with TotalFORCE
control.
PowerFlex Drives with TotalFORCE Control Programming Manual, 750-PM100
PowerFlex 750-Series Products with TotalFORCE Control Technical Data, 750-TD100