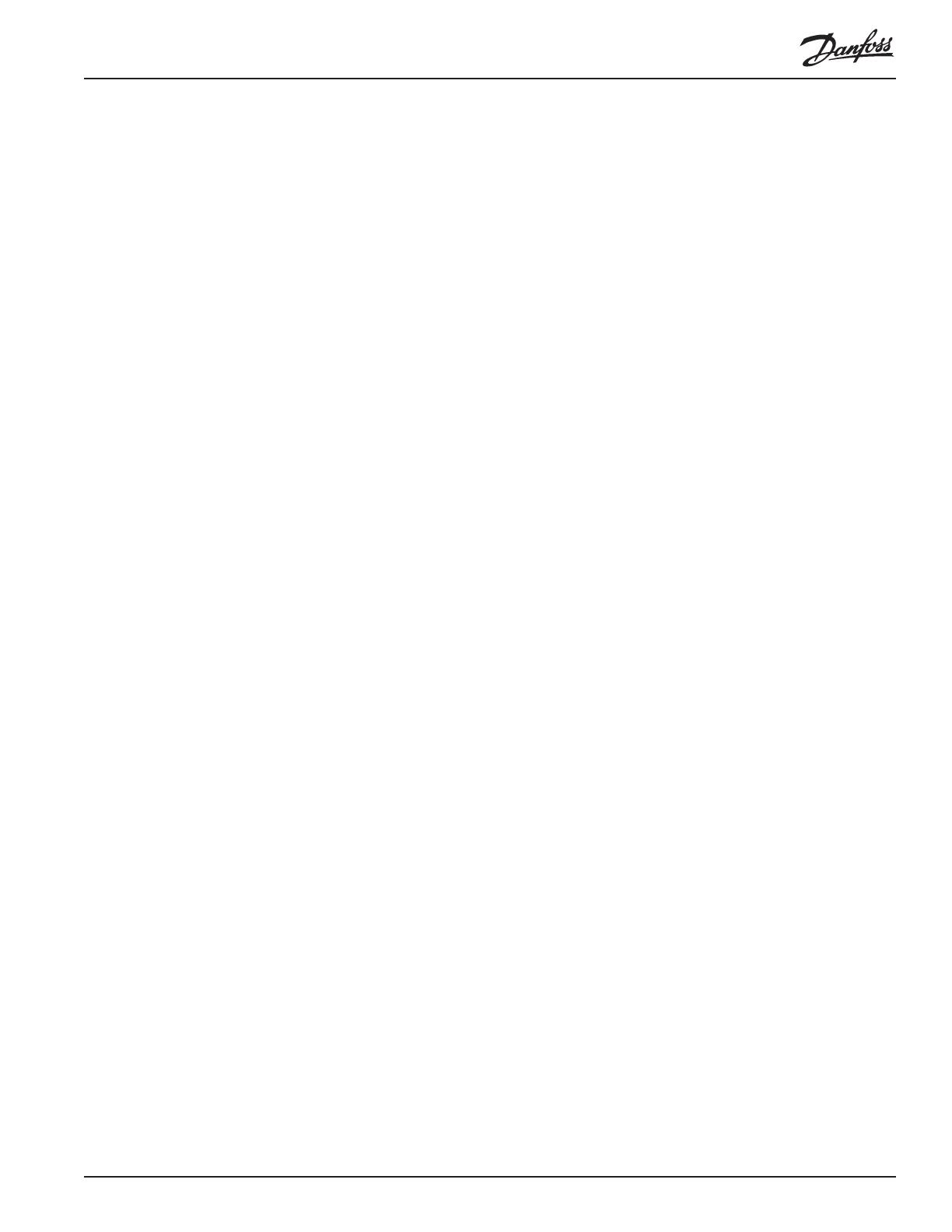
AKC 55 System Manual RC.IU.B3.22 4-19
box, multi-deck, single deck, service, etc.
Fixture Name (List box) There is a large selection of common fixture
names for each of the fixture types that can be se-
lected above, and there is a selection User Def. After
making that selection, you will be able to spell out your
own name on the following line.
Enter user defined name (Label) The name of a user-defined fixture. Any of
the characters in the AKC 55 character set can be
used, including upper and lower case letters and
symbols.
Monitor box door (List box: Yes, No) Whether or not a box door switch
will be monitored (appears for boxes only).
Shutdown when door open (List box: Yes, No) Whether or not to shut down
refrigeration when the box door is open.
No case/box sensors (0 to 15) The number of sensors in this fixture or
circuit.
Temperature control (List box: Yes, No) Whether or not temperature contol
will be used.
Controlling sensor (List box:)
Min Temp The lowest of the sensors in the fixture or
on the circuit will be used for temperature control.
Max Temp The highest of the sensors in the fixture
or on the circuit will be used for temperature control.
Average The average of all the sensors in the fixture
or on the circuit will be used for temperature control.
[circuit names] The name of each sensor will be
listed, and any can be selected. That sensor, then, will
be used for temperature control.
Target: (-99.0 to 150.0 [target] 1.0 to 20.0 [range] The target
temperature and the range about the target, used in
temperature control. The range is the amount above or
below target that the actual sensor temperature is
allowed to change before a control action is taken.
Type of defrost (List box) Various types of defrost can be chosen:
None, Hot Gas, Time Off, Air, or Electric.
Drip down delay (1 to 600) The number of seconds that refrigeration
will remain off after termination of defrost.
Termination type [Defrost time settings made on the pages that follow
must also be considered. If a minimum defrost time
is used, that time must elapse regardless of the
settings made on this page. If a defrost duration is
specified, either that time must elapse OR the
requirements set on this page must be satisfied for
defrost to terminate.]
(List box) Various termination strategies are listed.
Defrost sensor There is a dedicated defrost tem-
perature sensor that will be used to terminate defrost.
Disch air snsr The fixture discharge air sensor will
be used to terminate defrost at a set temperature.
On/Off Input An electrical switch (such as a Klixon
®