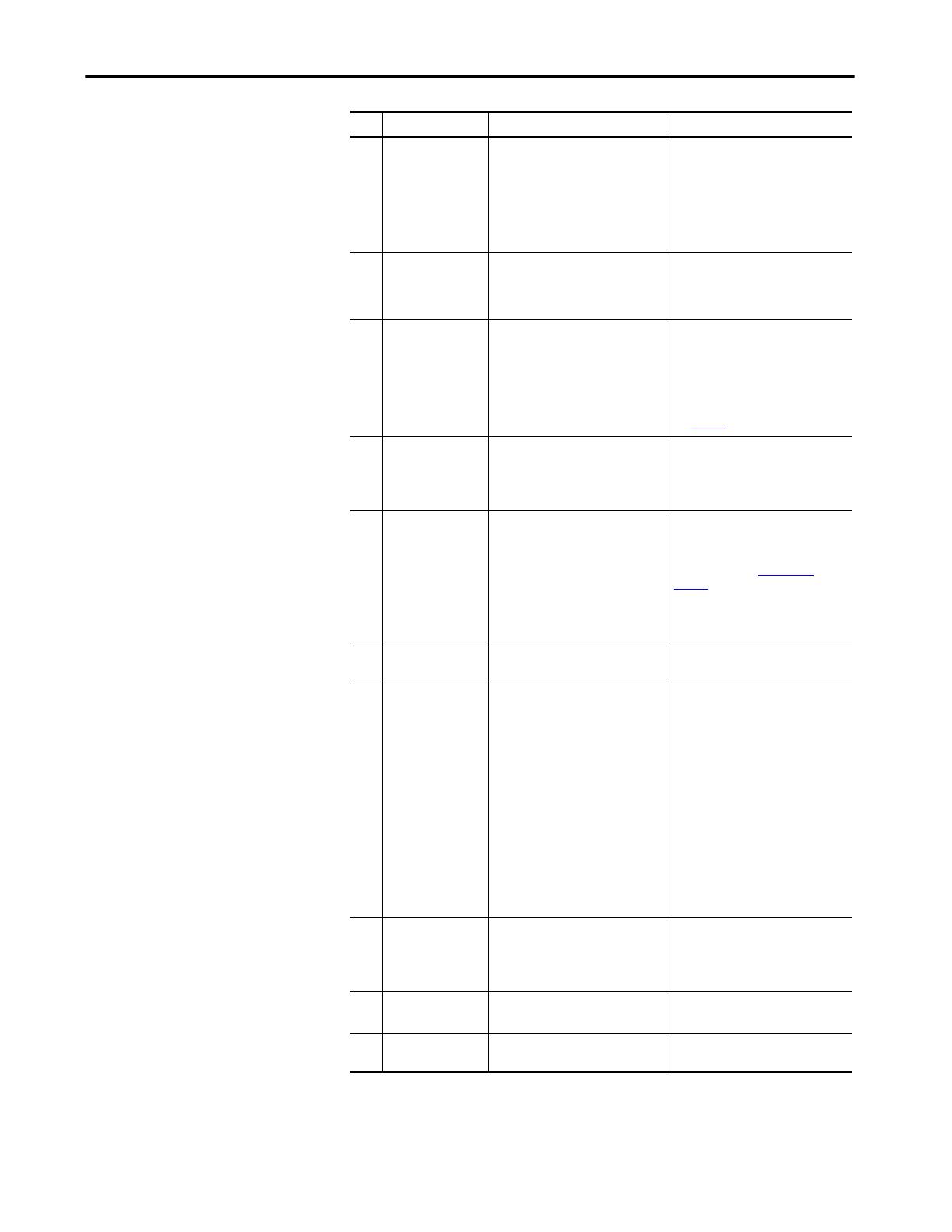
Rockwell Automation Publication 20Y-TG001C-EN-P - April 2017 13
Troubleshooting and Error Codes Chapter 1
5 DC OverVolt The DC bus voltage exceeded the
maximum value of 911V for 400/480V
units, or 1200V for 600/690V units.
Check if the AFE was in a regenerative
current limit condition, which can
indicate an excess regenerative load.
Adjust parameter 076 [Regen Power
Lmt].
Monitor incoming AC line for high
voltage or voltage transients.
7 Overload When input current exceeds 125% for
60 seconds or 150% for 30 seconds.
The overload is a linear type in
counting up.
Reduce the current consumption of the
AFE or increase parameter 133 [Cnvrtr
OL Factor].
8 HeatsinkOvrTp The power structure heatsink
temperature has exceeded the
maximum allowable value.
85 °C (185 °F) = Alarm
90 °C (194 °F) = Fault
Verify that the maximum ambient
temperature has not been exceeded.
Check the fans (including ASIC board on
the power structure).
Check for an excess load.
Verify that the airflow plate is installed.
See page 45
.
9 IGBT OverTemp The output transistors have exceeded
their maximum operating temperature
due to an excessive load.
Verify that the maximum ambient
temperature has not been exceeded.
Check the fan or fans.
Check for an excess load.
10 System Fault A hardware problem exists in the
power structure.
Reset the fault and restart.
Verify the fiber-optic connections.
Verify ASIC board jumper connections
from X9 to X15 (see Figure 13 on
page 91).
Contact technical support.
If the problem persists, replace or repair
the power structure.
12 AC OverCurr The AC line current has exceeded the
hardware current limit.
Check for an excessive load or other
causes of excess current.
13 Ground Fault A current path to earth ground exists
that is greater than the parameter 082
[Ground I Lvl] value. The current must
appear for 800 milliseconds before the
unit will fault.
Use a digital voltmeter to check for low
impedance to ground, and verify the bus
cables/bars between these items:
Disconnect and AC input lines
Power structure and LCL filter
For AFE in IP20 enclosure:
• Q0 input breaker and K1 input
contactor, which includes the
precharge disconnect
• LCL filter and K1 input connection
For AFE in IP21 enclosure:
• Q1 (MCCB) and Q0 disconnect switch,
which includes the precharge
disconnect
• LCL filter and Q1 (MCCB)
14 Power Structure Fault A hardware problem exists in the
power structure.
Cycle the power.
Contact technical support.
If the problem persists, replace the
converter unit.
17 LineSync Fail One input of the known phase rotation
is missing.
Check all user-supplied fuses.
Check the AC input line voltage.
21 Phase Loss There are zero current in one of the
three phases.
Check supply voltage, fuses, and cable.
No. Name Description Action (if appropriate)