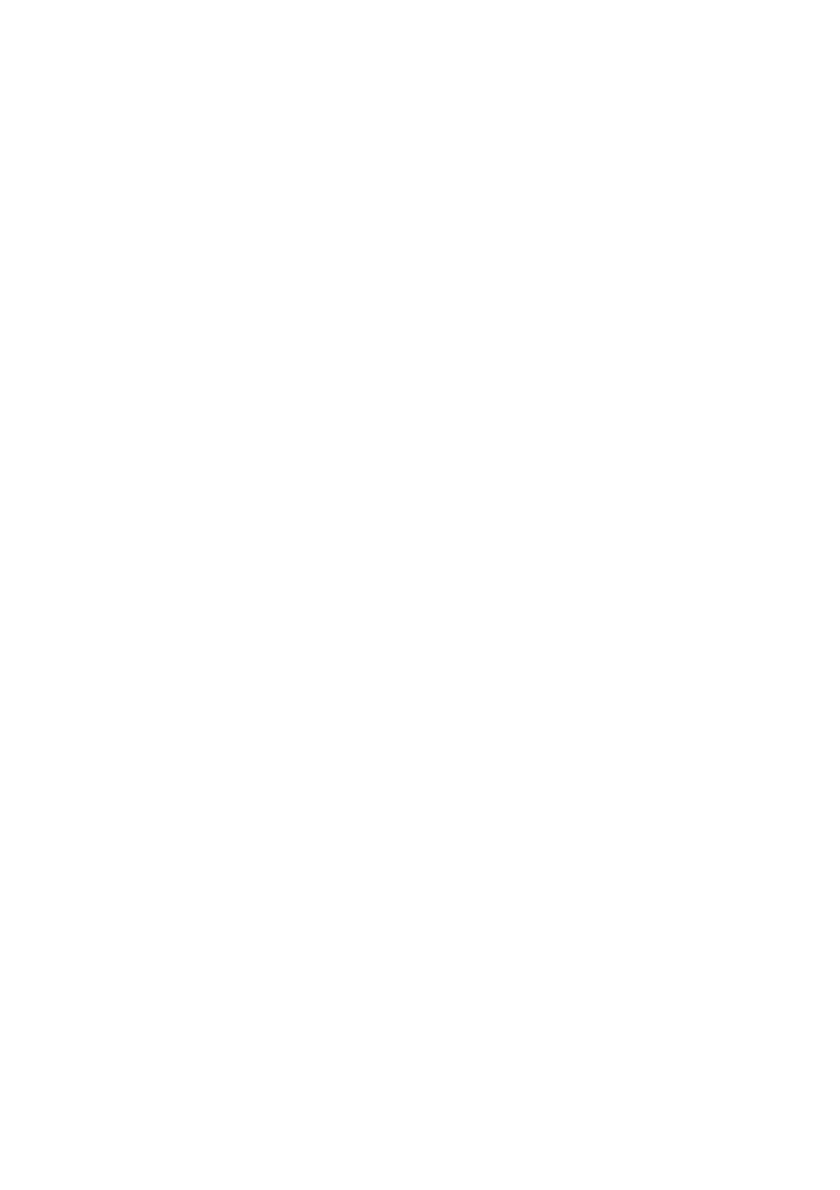
CARBON-DIOXIDE CAN BECARBON-DIOXIDE CAN BE
CARBON-DIOXIDE CAN BECARBON-DIOXIDE CAN BE
CARBON-DIOXIDE CAN BE
DANGEROUSDANGEROUS
DANGEROUSDANGEROUS
DANGEROUS
WW
WW
W
ARNINGARNING
ARNINGARNING
ARNING
1.1.
1.1.
1.
ALAL
ALAL
AL
WW
WW
W
AA
AA
A
YSYS
YSYS
YS
connect COconnect CO
connect COconnect CO
connect CO
22
22
2
or Gas Cylinderor Gas Cylinder
or Gas Cylinderor Gas Cylinder
or Gas Cylinder
to a REDUCING Vto a REDUCING V
to a REDUCING Vto a REDUCING V
to a REDUCING V
ALAL
ALAL
AL
VEVE
VEVE
VE
..
..
.
2.2.
2.2.
2.
NEVERNEVER
NEVERNEVER
NEVER
try to connect Cylindertry to connect Cylinder
try to connect Cylindertry to connect Cylinder
try to connect Cylinder
directly to Product Containerdirectly to Product Container
directly to Product Containerdirectly to Product Container
directly to Product Container
..
..
.
3.3.
3.3.
3.
NEVERNEVER
NEVERNEVER
NEVER
Interconnect Soft Drinks COInterconnect Soft Drinks CO
Interconnect Soft Drinks COInterconnect Soft Drinks CO
Interconnect Soft Drinks CO
22
22
2
or Gas Cylinder Equipmentor Gas Cylinder Equipment
or Gas Cylinder Equipmentor Gas Cylinder Equipment
or Gas Cylinder Equipment
with other Equipment.with other Equipment.
with other Equipment.with other Equipment.
with other Equipment.
4.4.
4.4.
4.
ALAL
ALAL
AL
WW
WW
W
AA
AA
A
YSYS
YSYS
YS
Secure Cylinder uprightSecure Cylinder upright
Secure Cylinder uprightSecure Cylinder upright
Secure Cylinder upright
whilst in Use.whilst in Use.
whilst in Use.whilst in Use.
whilst in Use.
5.5.
5.5.
5.
ALAL
ALAL
AL
WW
WW
W
AA
AA
A
YSYS
YSYS
YS
Keep Cylinder away fromKeep Cylinder away from
Keep Cylinder away fromKeep Cylinder away from
Keep Cylinder away from
Heat.Heat.
Heat.Heat.
Heat.
6.6.
6.6.
6.
NEVERNEVER
NEVERNEVER
NEVER
Drop or throw Cylinders.Drop or throw Cylinders.
Drop or throw Cylinders.Drop or throw Cylinders.
Drop or throw Cylinders.
7.7.
7.7.
7.
NEVERNEVER
NEVERNEVER
NEVER
TT
TT
T
ry to Unscrew Fittings fromry to Unscrew Fittings from
ry to Unscrew Fittings fromry to Unscrew Fittings from
ry to Unscrew Fittings from
Containers.Containers.
Containers.Containers.
Containers.
8.8.
8.8.
8.
ALAL
ALAL
AL
WW
WW
W
AA
AA
A
YSYS
YSYS
YS
VV
VV
V
entilate Area after COentilate Area after CO
entilate Area after COentilate Area after CO
entilate Area after CO
22
22
2
Leakage.Leakage.
Leakage.Leakage.
Leakage.