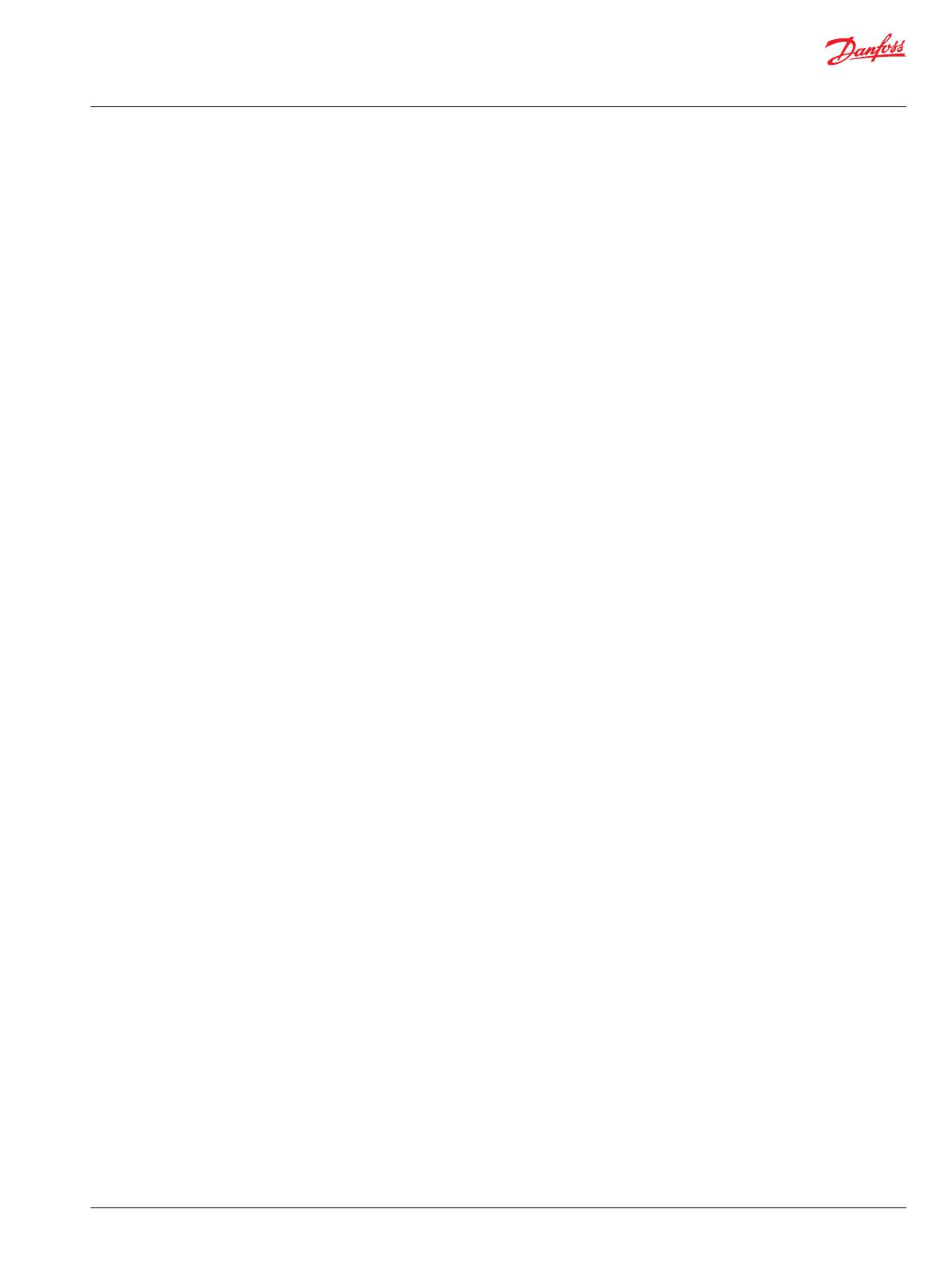
About this manual
WS103 Remote Solution Technical Information...................................................................................................................5
Overview
WS103 remote solution..................................................................................................................................................................6
OEM responsibility...........................................................................................................................................................................6
Safety critical functions.................................................................................................................................................................. 7
FCC notice...........................................................................................................................................................................................8
Device elements
WS103 device elements.................................................................................................................................................................9
Front label......................................................................................................................................................................................9
Nameplate label.......................................................................................................................................................................... 9
Ordering information
WS103 model.................................................................................................................................................................................. 11
Product configuration model code.........................................................................................................................................11
Cables, protection cap, and accessories................................................................................................................................11
WS103 kit.......................................................................................................................................................................................... 12
WS system tools and documentation.....................................................................................................................................12
Conformity
Compliant with CE.........................................................................................................................................................................13
Compliance with E1...................................................................................................................................................................... 13
Compliance with FCC................................................................................................................................................................... 13
PLUS+1
®
Compliant.......................................................................................................................................................................13
Safety information
Data transmission.......................................................................................................................................................................... 14
Health care facilities......................................................................................................................................................................14
Air traffic communications.........................................................................................................................................................14
Explosive areas................................................................................................................................................................................14
Antennas on WS devices.............................................................................................................................................................15
Electronic equipment interference......................................................................................................................................... 15
Installation........................................................................................................................................................................................15
Power supply and connection.................................................................................................................................................. 15
Polarity reversal.............................................................................................................................................................................. 15
Ingress protection rating.............................................................................................................................................................16
Machine wiring guidelines......................................................................................................................................................... 16
Machine welding guidelines......................................................................................................................................................16
Disposal............................................................................................................................................................................................. 17
Functions
Operating modes...........................................................................................................................................................................18
Power modes...................................................................................................................................................................................18
Host processor................................................................................................................................................................................ 18
CAN interface...................................................................................................................................................................................18
Serial interface.................................................................................................................................................................................18
WLAN frequencies......................................................................................................................................................................... 18
WLAN mode infrastructure.........................................................................................................................................................20
WLAN infrastructure and PLUS+1
®
Service Tool.................................................................................................................20
WLAN CAN to CAN bridging...................................................................................................................................................... 20
Access control and security........................................................................................................................................................20
Bluetooth
®
mode............................................................................................................................................................................21
Bluetooth
®
and PLUS+1
®
Service Tool.................................................................................................................................... 21
Bluetooth
®
Classic CAN to CAN bridging...............................................................................................................................21
Technical data
Electrical data.................................................................................................................................................................................. 22
Mechanical data............................................................................................................................................................................. 22
Interface / protocols / certifications........................................................................................................................................22
Installation
Technical Information
WS103 Remote Solution
Contents
©
Danfoss | April 2016 BC00000365en-US0102 | 3