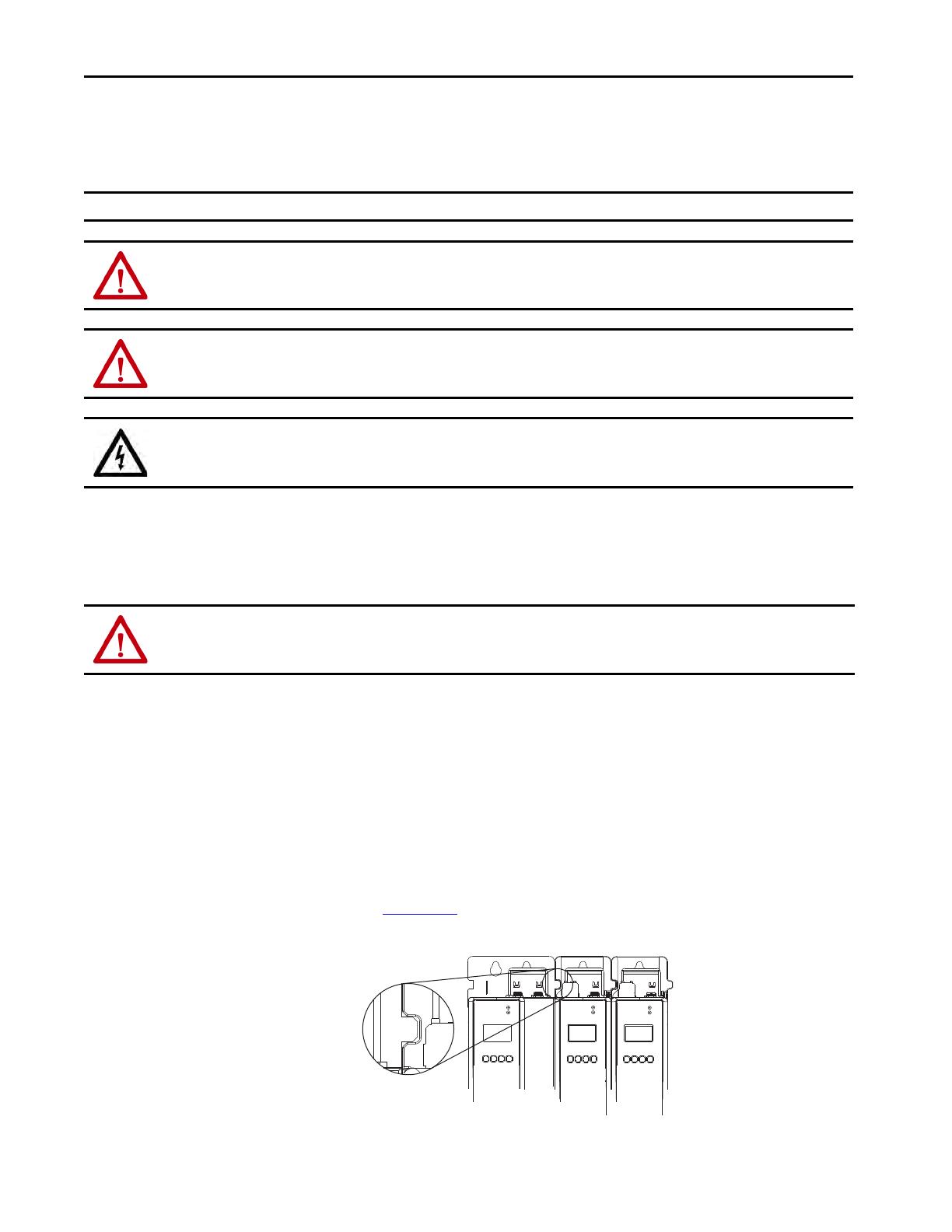
Rockwell Automation Publication 2198T-IN001C-EN-P - October 2019 7
Kinetix 5700 iTRAK Power Supply and iTRAK Bus Conditioner Module
Grounding Screw
The iTRAK power supply must be run from only grounded-wye power distribution with the grounding screw installed (default setting). Do not
remove the grounding screw.
Install the iTRAK Power Supply
These procedures assume that you have prepared your panel and understand how to bond your system. For installation instructions regarding
equipment and accessories that are not included here, refer to the instructions that came with those products.
System Mounting Requirements
• The iTRAK power supply must be enclosed in a grounded conductive enclosure that offers protection as defined in standard EN 60529
(IEC 529) to IP54 such that they are not accessible to an operator or unskilled person. A NEMA 4X enclosure exceeds these requirements
providing protection to IP66.
• The panel that you install inside the enclosure for mounting your system components must be on a flat, rigid, vertical surface that is not
subjected to shock, vibration, moisture, oil mist, dust, or corrosive vapors in accordance pollution degree 2 (EN 61800-5-1) because the
product is rated to protection class IP20 (EN 60529).
Mount the iTRAK Power Supply
The iTRAK power supply must be spaced by aligning the zero-stack tab and cutout. To mount, size, and configure shared-bus configurations, see
the Kinetix 5700 Servo Drives User Manual, publication 2198-UM002.
Mount the iTRAK power supply to the cabinet subpanel with M5 (#10-32) steel bolts that are torqued to 4.0 N•m (35.4 lb•in), max.
IMPORTANT EMC performance can be affected if you remove the grounding screw.
ATTENTION: If you remove the grounding screw, the risk of equipment damage exists because the unit no longer maintains line-to-neutral voltage protection.
ATTENTION: To avoid personal injury, the grounding-screw access door must be kept closed when power is applied. If power was present, and then removed,
wait at least 5 minutes for the system voltage to dissipate, and verify that no voltage exists before accessing the grounding screw.
SHOCK HAZARD: Avoid hazard of electrical shock; mount and wire the power supply before power is applied. Once power is applied, connector terminals can
have voltage present even when not in use.
ATTENTION: Plan the installation of your system so that you can cut, drill, tap, and weld with the system that is removed from the enclosure. Because the system
is of the open type construction, be careful to keep any metal debris from falling into it. Metal debris or other foreign matter can become lodged in the circuitry
and result in damage to components.
Zero-stack Tab and
Cutout Aligned
Shared-bus connection system is not shown for clarity.