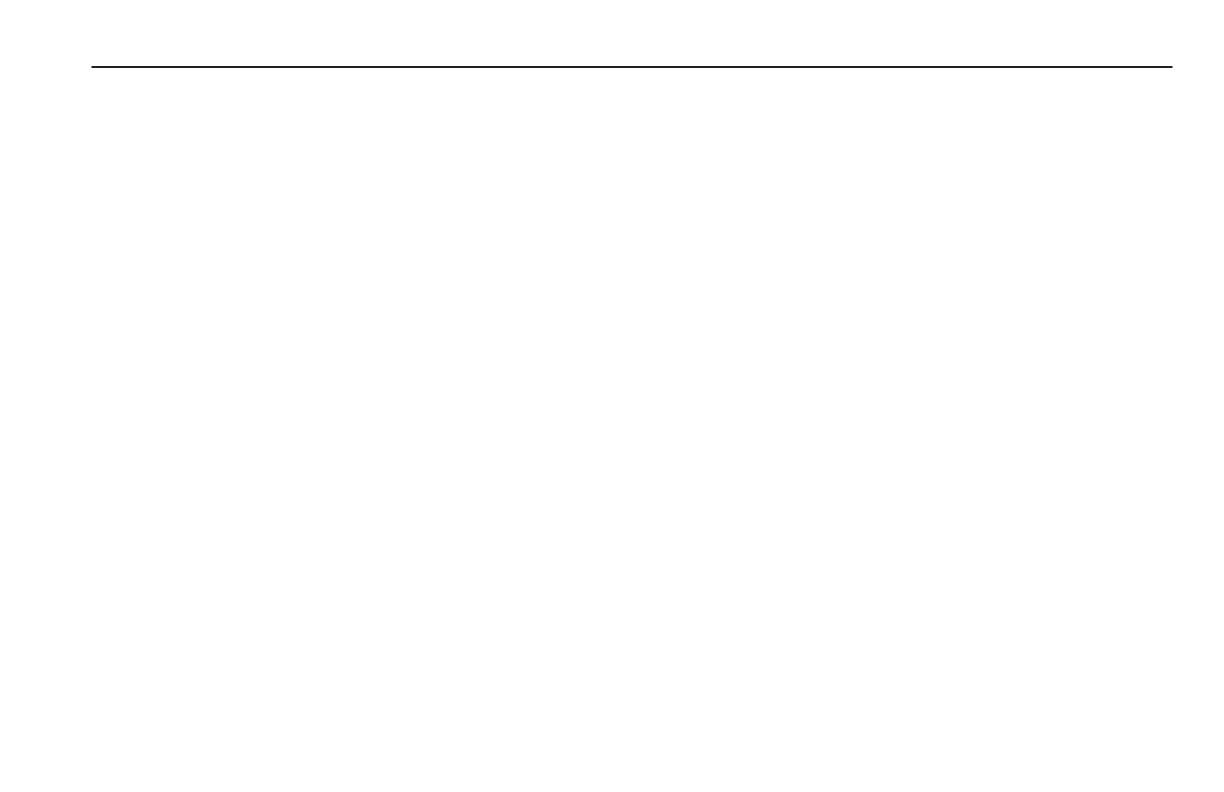
Table of Contents
Chapter 1 – Information and Precautions
Chapter Objectives 1-1. . . . . . . . . . . . . . . . . . . . . . . . . . . . . . . . .
Manual Objectives 1-1. . . . . . . . . . . . . . . . . . . . . . . . . . . . . . . . . .
Receiving, Unpacking, Inspection, Storing 1-2. . . . . . . . . . . . . . . .
General Precautions 1-2. . . . . . . . . . . . . . . . . . . . . . . . . . . . . . . .
Conventions Used In This Manual 1-3. . . . . . . . . . . . . . . . . . . . . .
Nameplate Location 1-4. . . . . . . . . . . . . . . . . . . . . . . . . . . . . . . .
Firmware Compatibility 1-4. . . . . . . . . . . . . . . . . . . . . . . . . . . . . .
Catalog Number Code Explanation 1-5. . . . . . . . . . . . . . . . . . . . . .
Chapter 2 – Installation/Wiring
Chapter Objectives 2-1. . . . . . . . . . . . . . . . . . . . . . . . . . . . . . . . .
Terminal Block Access 2-3. . . . . . . . . . . . . . . . . . . . . . . . . . . . . . .
Input Devices 2-5. . . . . . . . . . . . . . . . . . . . . . . . . . . . . . . . . . . . .
Input Power Conditioning 2-6. . . . . . . . . . . . . . . . . . . . . . . . . . . . .
Input Fusing 2-6. . . . . . . . . . . . . . . . . . . . . . . . . . . . . . . . . . . . . .
Electrical Interference – EMI/RFI 2-7. . . . . . . . . . . . . . . . . . . . . . .
RFI Filtering 2-8. . . . . . . . . . . . . . . . . . . . . . . . . . . . . . . . . . . . . .
CE Conformity 2-8. . . . . . . . . . . . . . . . . . . . . . . . . . . . . . . . . . . .
Grounding 2-9. . . . . . . . . . . . . . . . . . . . . . . . . . . . . . . . . . . . . . .
Power Wiring 2-11. . . . . . . . . . . . . . . . . . . . . . . . . . . . . . . . . . . .
Drive Operation without a Human Interface Module (HIM) 2-17. . . . .
Control Wiring 2-17. . . . . . . . . . . . . . . . . . . . . . . . . . . . . . . . . . . .
Output Devices 2-22. . . . . . . . . . . . . . . . . . . . . . . . . . . . . . . . . . .
Cable Termination 2-22. . . . . . . . . . . . . . . . . . . . . . . . . . . . . . . . .
Adapters 2-23. . . . . . . . . . . . . . . . . . . . . . . . . . . . . . . . . . . . . . .
Chapter 3 – Human Interface Module
Chapter Objectives 3-1. . . . . . . . . . . . . . . . . . . . . . . . . . . . . . . . .
HIM Description 3-1. . . . . . . . . . . . . . . . . . . . . . . . . . . . . . . . . . .
HIM Operation 3-1. . . . . . . . . . . . . . . . . . . . . . . . . . . . . . . . . . . .
HIM Removal and Installation 3-4. . . . . . . . . . . . . . . . . . . . . . . . . .
HIM Modes 3-5. . . . . . . . . . . . . . . . . . . . . . . . . . . . . . . . . . . . . . .
Program and Display Modes 3-7. . . . . . . . . . . . . . . . . . . . . . . . . .
Process Mode 3-10. . . . . . . . . . . . . . . . . . . . . . . . . . . . . . . . . . . .
EEprom Mode 3-11. . . . . . . . . . . . . . . . . . . . . . . . . . . . . . . . . . . .
Search Mode 3-14. . . . . . . . . . . . . . . . . . . . . . . . . . . . . . . . . . . .
Control Status Mode 3-15. . . . . . . . . . . . . . . . . . . . . . . . . . . . . . .
Password Mode 3-17. . . . . . . . . . . . . . . . . . . . . . . . . . . . . . . . . .
Chapter 4 – Start–Up
Chapter Objectives 4-1. . . . . . . . . . . . . . . . . . . . . . . . . . . . . . . . .
Start-up Procedure 4-1. . . . . . . . . . . . . . . . . . . . . . . . . . . . . . . . .
Chapter 5 – Programming
Chapter Objectives 5-1. . . . . . . . . . . . . . . . . . . . . . . . . . . . . . . . .
Chapter Conventions 5-1. . . . . . . . . . . . . . . . . . . . . . . . . . . . . . . .
Function Index 5-1. . . . . . . . . . . . . . . . . . . . . . . . . . . . . . . . . . . .
Parameter Flow Chart 5-1. . . . . . . . . . . . . . . . . . . . . . . . . . . . . . .
Programming Example 5-4. . . . . . . . . . . . . . . . . . . . . . . . . . . . . .
Metering 5-5. . . . . . . . . . . . . . . . . . . . . . . . . . . . . . . . . . . . . . . . .
Set Up 5-8. . . . . . . . . . . . . . . . . . . . . . . . . . . . . . . . . . . . . . . . . .
Advanced Setup 5-15. . . . . . . . . . . . . . . . . . . . . . . . . . . . . . . . . .
efesotomasyon.com - Allen Bradley,Rockwell,plc,servo,drive