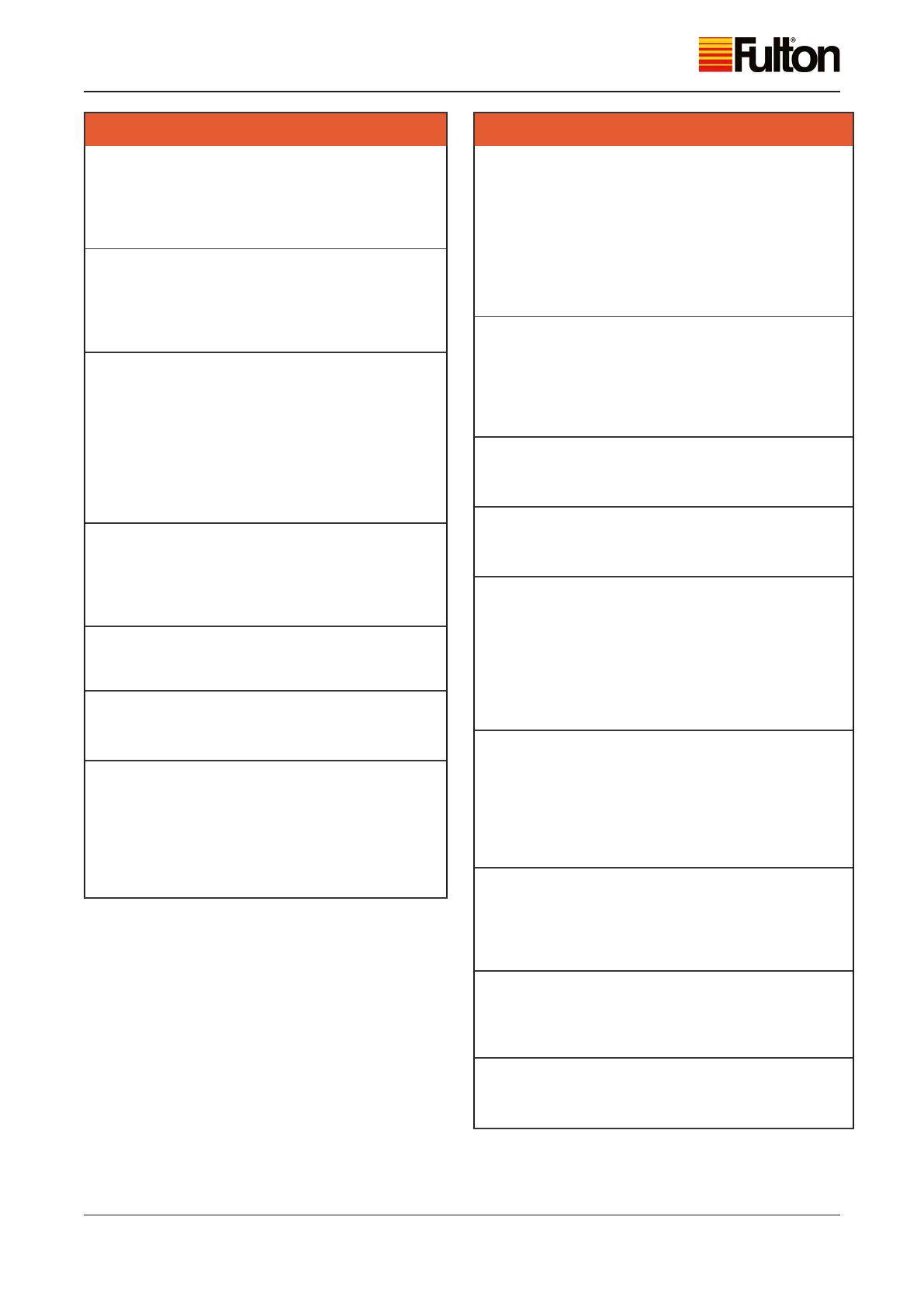
SAFETY PRECAUTIONS
|Page V J-CLASSIC-IOMM-1
The discharge from the safety relief valve shall be
arranged so that there will be no danger of scalding
personnel or damage to equipment. Provisions should
be made to properly drain safety relief valve discharge
piping.
Fluids under pressure may cause injury to personnel or
damage to equipment when released. Be sure to shut off
all incoming and outgoing fluid shut-off valves and
carefully decrease all trapped pressures to zero before
performing any maintenance.
Do not attempt to start the equipment for any testing
prior to filling and purging the vessel. A dry fire will
seriously damage the equipment and may result in
property damage or personnel injury and is not covered
by warranty. In case of a dry firing event, shut off
the fuel supply and allow the vessel to cool to room
temperature before fluid is reintroduced to the pressure
vessel. The boiler should be inspected by a qualified
individual prior to commissioning the unit.
When opening any drains on the equipment or piping
system, steps should be taken to avoid scalding/ burning
of personnel due to hot fluids. Whenever possible, the
system should be cooled prior to opening any drains.
Hot surfaces (over 49 °C) should be insulated or
shielded for safety where practicable. See
Should overheating occur or the gas supply fails to shut
off, manually shut off the gas supply external to the
equipment.
Improper installation or maintenance of gauge glass and
connections can cause immediate or delayed breakage
resulting in bodily injury and/or property damage. Only
trained personnel should install and maintain gauge glass
connections. Wear suitable safety eyewear during
installation. Be sure all parts are free of chips and debris.
WATER SOFTENER, SALT & CHEMICAL TREATMENT
The chemicals required to operate the water softeners and
chemical treatment plants CAN BE SUPPLIED by Fulton Ltd.
It is the responsibility of the operator to ensure adequate
supplies of chemical are always available (including
commissioning). Costly repairs could be required should the
plant operate without chemicals, or the wrong dosage of
chemicals.
HYDRAULIC TEST - RISK OF BRITTLE FRACTURE
Hydraulic testing requires specialist equipment and is
normally only required by engineering surveyors /
inspectors. To ensure the material/ pressure vessel does
not suffer from brittle fracture, hydraulic testing should
not be conducted below 7 °C.
The flue arrangement and draft conditions should be in
accordance with the information in this manual for proper
performance of the equipment.
Use appropriate leak-detection fluid. Clean all piping
thoroughly after completing the leak check.
A temperature exceeding 32 °C* in the boiler room may
cause premature failure of electrical components.
Provisions should be made to maintain an ambient
temperature of 32 °C* or less (the panel box interior should
not exceed 32 °C*.
*Pumps, Programmable Logic Controllers (PLC) or
sequence panels may require lower ambient
temperatures or additional cooling.
Particulate matter or chemicals (example: per
chloroethylene, chlorine, or halogenated compounds) in the
combustion air supply to the boiler will cause damage or
failure to the burner and is not covered under warranty.
High-risk situations for particulate matter to be in the air
include construction and maintenance activities.
For all systems containing boilers or unfired steam
generators, the water chemistry in the boiler must be kept
within the limits outlined in this manual. Failure to do so may
cause premature pressure vessel failure and poor steam
quality and will void the warranty.
Do not run the pump dry. Irreparable damage to the seal can
result. Prime the pump in accordance with the
manufacturer’s instructions. Never operate the pump with a
closed discharge valve.
Should you suspect that the boiler’s flue passageways have
become blocked, stop the boiler immediately and contact
the Fulton office.