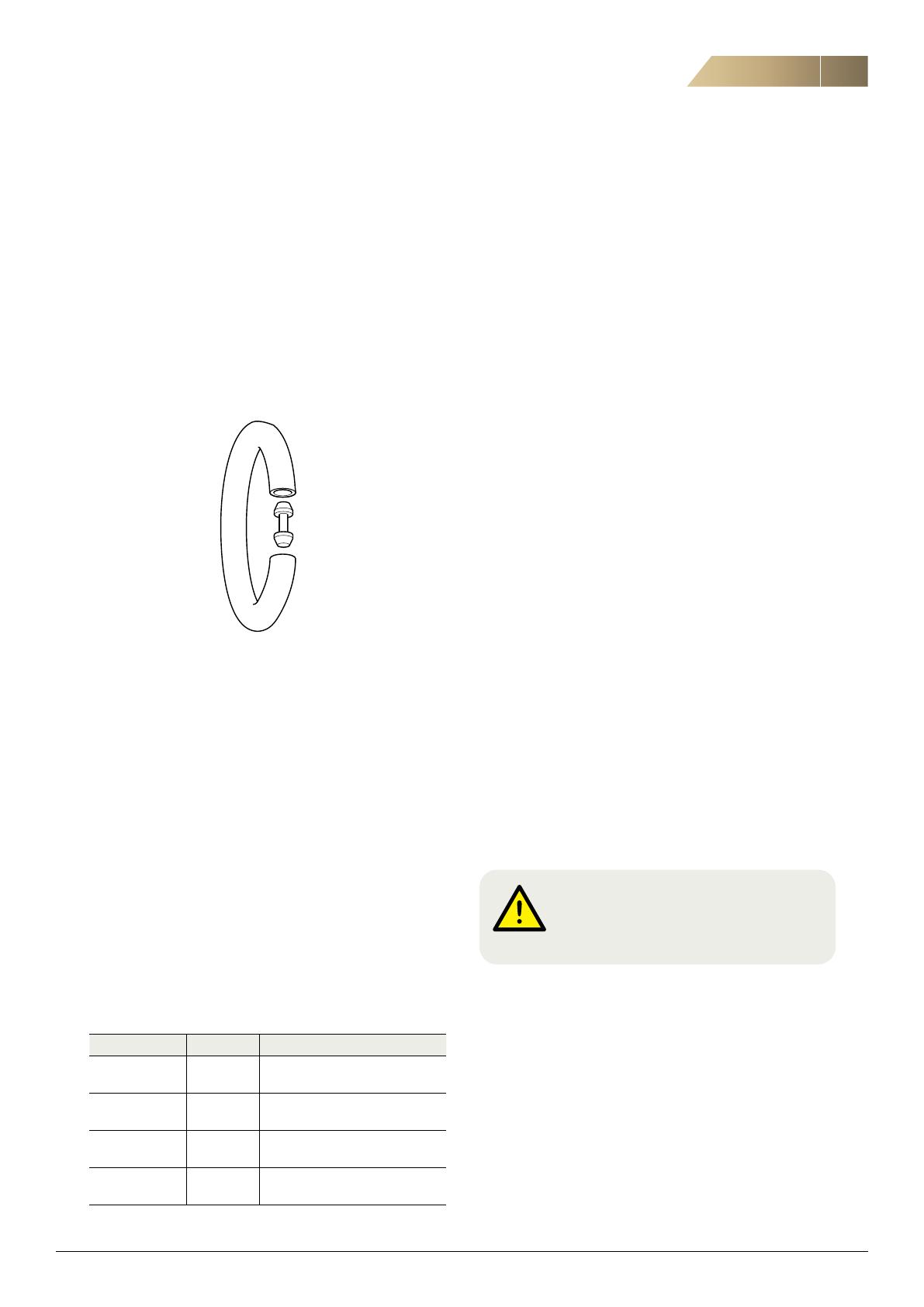
ROTARY HEAT EXCHANGER
Installation and maintenance instruction
5
FläktGroup DC_9112GB 20220921_R1 Specifications are subject to alteration without notice
TO CHANGE THE DRIVE BELT
Due to wear, it may be necessary to change the drivebelt.
The original belt has a welded joint. The replacement belt is jointed
together by means of the pin supplied with it. The correct replace-
ment belt with correct length can be selected from the spare
parts list. Alternatively, 10 or 20 meter length can be purchased
for cutting and fixing on site.
DIRECTION OF ROTATION
Check that the rotor is rotating in the right direction.
MAINTENANCE
Inspection and service on the heat recovery unit concern mainly
the rotor, seals and drive equipment.
The heat recovery unit is accessible for service through the
inspection doors which cover the whole of the side wall. The
rotor can be rolled out for service.
The intervals are based on the assumption that the unit is in
operation for about 2000 hours over a 12-month period and
operates in a normal comfort ventilation installation. If the dust
content of the supply and/or exhaust air is high, the unit should
be inspected more frequently. Maintenance of the heat recovery
unit is greatly facilitated if the recommended equipment is used
for monitoring and purging operation.
SERVICE SCHEDULE
Object Interval Action
Rotor face 6 months Inspect and clean,
if necessary.
Drive belt 6 months Check for tension and wear.
Rotor bearings 12 months The EQRB has permanently
lubricated bearings.
Monitoring
equipment
12 months Check the performance.
ROTOR - FACE SURFACES
Non-hygroscopic
Check that there is no dust deposit on the rotor faces.
If necessary, either vacuum-clean the rotor or use compressed
air aimed straight at the surface from a distance of at least 50
mm blowing from the clean towards the dust coated side.
If vacuum-cleaning or blowing with compressed air proves to
be inadequate (greasy dust), clean the non-hygroscopic rotor
surface as follows:
Spray a grease solvent by hand onto the dust-coated surface,
then blow clean with compressed air from the opposite side
aimed straight at the surface from a distance of at least 50 mm.
As an alternative, the rotor may be flushed with low pressure
steam up to 50 kPa or water up to 50 bar from a distance of at
least 50 mm aiming straight at the surface, provided that the
condensate from the steam or the flushing water can be satis-
factory collected.
Hygroscopic/Sorption/Epoxy
Check that there is no dust deposit on the rotor faces.
If necessary, either vacuum-clean the rotor face or use
compressed air aimed straight at the surface from a distance
of at least 50 mm blowing from the clean side towards the dust
coated side.
Water or grease solvents may not be used for these types of
rotors.
BEARINGS
The EQRB is equipped with permanently lubricated bearings
for which no maintenance is needed. Check that the bearing
sound is normal.
PURGING SECTOR
The EQRB has a fixed purging sector and no adjustment is
necessary.
IMPORTANT!
Never use methyl ethyl ketone, acetone
or other agressive solvents.