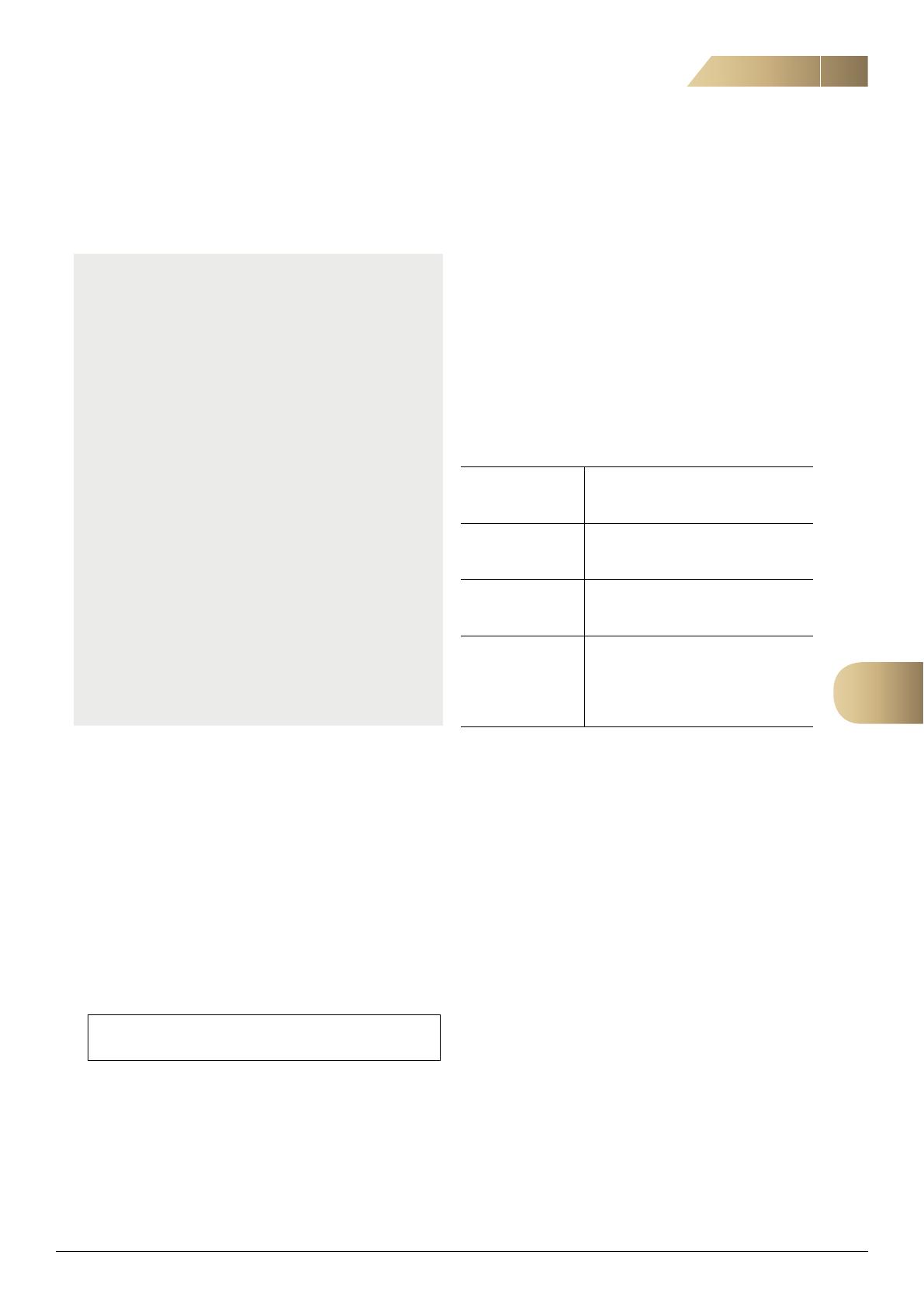
13
eQ MASTER COMMISSIONING
FläktGroup DC_9990GB 20190107_R0 Specifications are subject to alteration without notice
SETTINGS/FUNCTIONS
If a function is not activated, its menus or settings will not be
visible. The same applies within the function, depending on which
sub-functions are activated. For instance, if only fan stage 1 is acti-
vated, fan stages 2 and 3 cannot be selected in other functions.
DAMPERS
Multiple dampers can be connected and controlled by the eQ
Master. The dampers are controlled either via Modbus or via IO.
No additional settings need to be configured for damper actua-
tors connected via Modbus. The settings are factory configured.
Settings for directly connected damper actuators (i.e. damper
actuators connected to IO by an installation engineer) are under
MAIN INDEX Ú UNIT Ú
DAMPER CONTROL
An Off delay time is configured here. This means the time the
damper waits before switching off after the fans are switched off.
An “Opening time” is specified under Dampers The opening time
is the operating time allowed in order for the damper to open. All
directly connected dampers have the same operating parameters.
In other words, the supply air damper and the extract damper have
the same parameters. If the selected damper actuators have diffe-
rent opening times, the longest time should be specified.
Supply air control
Supply air control is a temperature control function where the
supply air temperature is kept constant, with or without some type
of setpoint offset, without any data being sent from the room. This
control function is suitable in rooms where the heating and cooling
loads are relatively constant and predictable, or rooms with indivi-
dual room control.
Room control
Room control is available in two versions, either with or without
a cascade function. The room temperature is measured and the
supply air temperature is adjusted as necessary. The user sets
minimum and maximum limits for the supply air temperature.
If room control is used, two sensors can be used to control the
temperature based on an average value.
Extract air control
Extract air control is the same as the room control function above,
except instead of the room temperature being measured, the
primary sensor is installed in the extract air duct.
Heating-cooling
setpoint
Set the heating setpoint and cooling
setpoint as separate values.
Cooling setpoint ≥ Heating setpoint.
Heating setpoint +
dead zone
Specify heating setpoint and dead zone.
Cooling setpoint = Heating setpoint +
dead zone.
Cooling setpoint –
dead zone
Specify cooling setpoint and dead zone.
Heating setpoint = Cooling setpoint –
dead zone.
Setpoint ±½ dead
zone
Specify the setpoint as the average
of the heating and cooling setpoints,
with the desired dead zone distributed
equally above and below the setpoint
value.
SECTION 5.
DAMPER............................................................................................................ 13
TEMPERATURE .........................................................................................13–14
OUTDOOR TEMPERATURE COMPENSATION .........................................14
OUTDOOR TEMPERATURE CURVE ...........................................................14
COOLING RECOVERY TEMPERATURE .....................................................14
COOLING RECOVERY ENTHALPY ............................................................. 15
FANS .................................................................................................................. 15
EXTRA FANS eQ EXTRA ........................................................................15–16
RECOVERY UNIT.......................................................................................17–19
AFTERTREATMENT ................................................................................20–22
PUMP CONTROL .....................................................................................22–23
EXTRA ZONES eQ EXTRA ............................................................................24
HUMIDITY ................................................................................................. 24–25
COMBINED PRODUCTS ................................................................................26
FILTERS .............................................................................................................27
PRE-HEATING ..................................................................................................27
OPERATING MODE .................................................................................28–30
OTHER FUNCTIONS ................................................................................31–35
WATER CIRCUITS eQ EXTRA ..............................................................36–38
TEMPERATURE
It generally applies to all temperature control that there are several
ways of setting the desired setpoint. When the temperature drops
below the heating setpoint, the heating sequence is activated, and
when it rises above the cooling setpoint the cooling sequence is
activated. When the actual temperature is within the dead zone,
all output signals that affect temperature will be zero. The compo-
nents that deliver cooling/heating are controlled in sequence in a
predetermined order, which is factory configured.
5