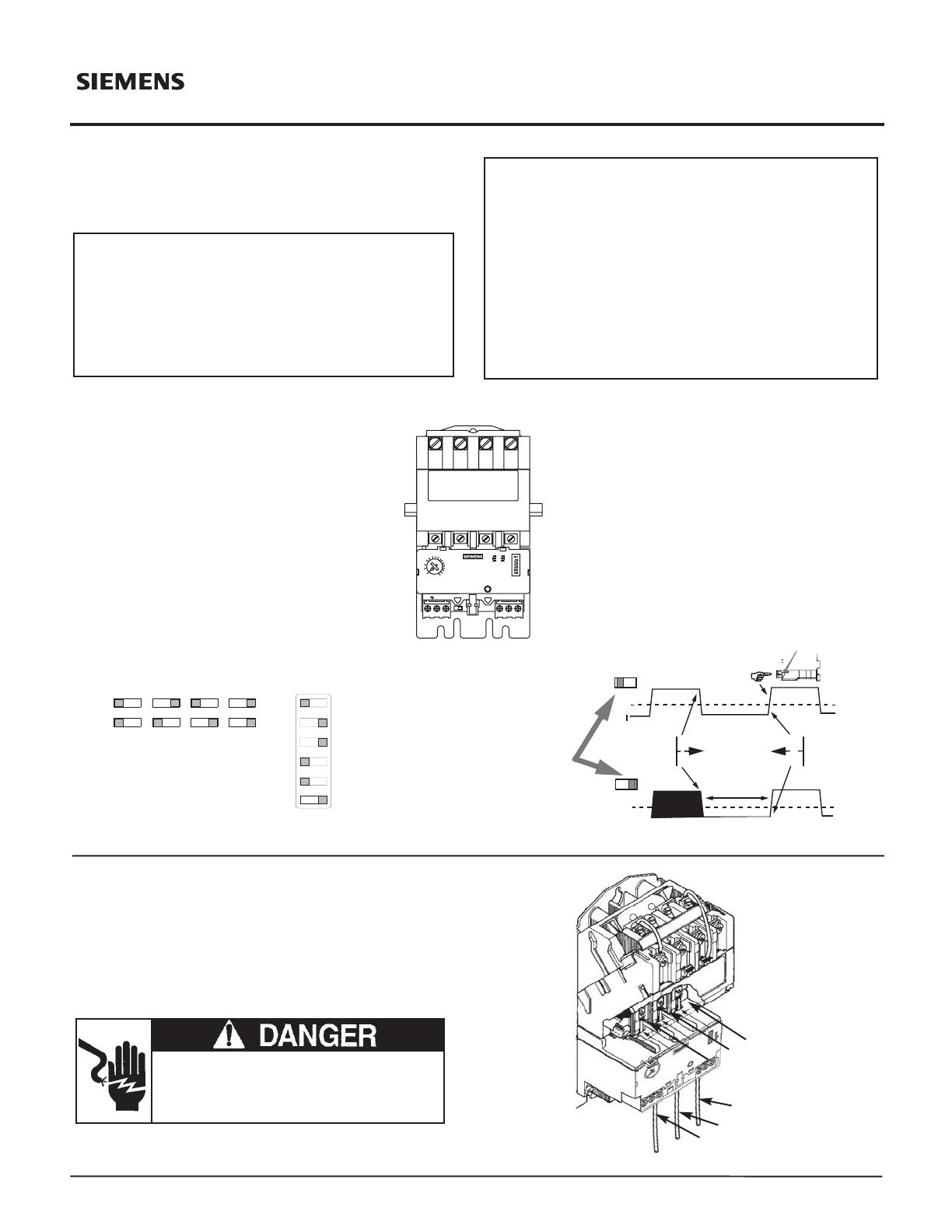
1
Installation Guide E87010-A0354-T002-A1-14CL
June 2015
for ESP200
Fig. 1
Siemens Industry, Inc. 5300 Triangle Parkway, Norcross, GA 30092 www.usa.siemens.com
1 DIP Switch Settings
Wire contactor per enclosed diagram.
2Wiring
Hazardous voltage.
Will cause death or serious injury
.
To avoid electrical shock or burn, turn off main and control
voltages before performing installation or maintenance.
(If ESP200 has windows) Push one motor lead through each pass-through
window in the overload relay, and connect to the contactor terminals (T1,T2,T3).
(Use only with 3-phase motors at 50/60Hz).
(If ESP200 has terminals) Connect each motor lead to the overload relay
terminals (T1, T2, T3).
(Use only with motors at 50/60 Hz).
THIS EQUIPMENT CONTAINS HAZARDOUSVOLTAGES. DEATH,
INJURY,OR PROPERTY DAMAGECAN RESULT IF SAFETY INSTRUCTIONS ARE NOT
FOLLOWED. ONLY QUALIFIED PERSONNEL SHOULD WORK ON OR AROUND THIS
EQUIPMENT AFTER BECOMING THOROUGHLY FAMILIAR WITH ALL WARNINGS,
SAFETY NOTICES,AND MAINTENANCE PROCEDURES CONTAINED HEREIN. THE
SUCCESSFULAND SAFE OPERATION OF THIS EQUIPMENTIS DEPENDENT UPON
PROPER HANDLING, INSTALLATION, OPERATION ANDMAINTENANCE.
QUALIFIED PERSON
FORTHE PURPOSEOF THIS MANUALAND PRODUCT LABELS,AQUALIFIED PERSON
IS ONE WHO IS FAMILIAR WITH THE INSTALLATION, CONSTRUCTIONAND
OPERATION OF THE EQUIPMENT, AND THE HAZARD INVOLVED. IN ADDITION, HE OR
SHE HAS THE FOLLOWING QUALIFICATIONS:
a) Is trained and authorizedto energize, deenergize, clear, groundand tag circuits and
equipment in accordance with established safety practices.
b) Is trained in the proper careand use of protective equipment such as rubber gloves, hard
hat,
safety glasses or faceshields, flash clothing, etc., in accordance with established safety practices.
c) Is trained in rendering first aid.
IMPORTANT
THESE INSTRUCTIONSDONOT PURPORT TO COVER ALL DETAILSORVARIATIONSIN
EQUIPMENT, NOR TO PROVIDEFOR EVERY POSSIBLE CONTINGENCYTOBEMET IN CONNEC-
TION WITH INSTALLATION, OPERATIONOR MAINTENANCE. SHOULD FURTHER INFORMATION
BE DESIRED OR SHOULD PARTICULAR PROBLEMS ARISE WHICH ARENOT COVERED
SUFFICIENTLY FOR THEPURCHASER’S PURPOSES, THEMATTER SHOULD BE REFERREDTO
THE LOCAL SIEMENS SALES OFFICE.THE CONTENTSOF THISINSTRUCTION MANUAL SHALL
NOT BECOME PA RT OF OR MODIFY ANY PRIOR OREXISTINGAGREEMENT, COMMITMENT OR
RELATIONSHIP. THE SALES CONTRACT CONTAINSTHE ENTIRE OBLIGATIONOF
SIEMENS. THE WARRANTY CONTAINEDINTHE CONTRACTBETWEENTHE PA RTIESIS THE
SOLE WARRANTYOF SIEMENS.ANY STATEMENTS CONTAINED HEREINDONOT CREATE NEW
WARRANTIES OR MODIFYTHE EXISTINGWARRANTY.
100% FLA
~ 3 min.
100% FLA
MAN.
MAN.
AUTO
AUTO
O
O
O
O
95
96
95
96
OFF
OFF
OFF
OFF
AUTO
OFF
ON
ON
PHASE UNBAL ON
PHASE LOSS ON
RESET MODE MAN.
GROUND FAULT ON
CLASS 5 10 20 30
ESP200
FULL LOAD AMPS
RESET
TEST
CAT.NO.
48ATC3S00
3UBB123-4CW2
95 96 A3+
A4- 97 98
5
6
4
3
12
10
7
8
9
5
TRIP CLASS
PHASE UNBAL ON
PHASE LOSS ON
OFF
OFF
RESET MODE MAN
GROUNDFAULT ON
AUTO
OFF
10
20
30
T1
T3
(with windows)
(with terminals)
T2
T1
T3
T2
Fig. 2
Fig. 3
SERIOUS PERSONAL
Trip Current: 125% of Full Load Current.
Phase Loss: Trip time in < 3 seconds.
Ground Fault trip: Ground fault current > 60%
of present motor current.
Reset Mode: Automatic or Manual.