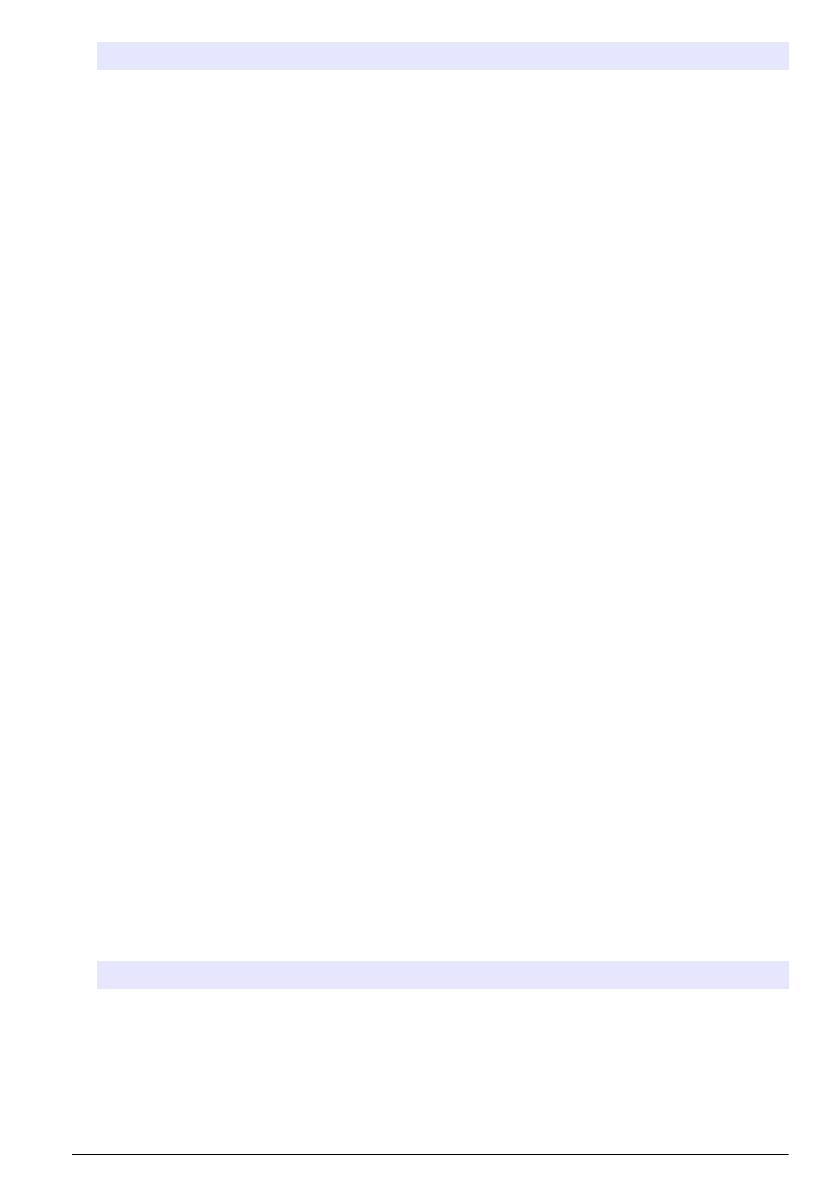
Option Description
DISPLAY FORMAT Changes the number of decimal places that are shown on the measure screen. When
set to auto, the number of decimal places changes automatically with changes in the
measured value.
MEAS UNITS Changes the units for the selected measurement—select the unit from the list
available.
TEMP UNITS Sets the temperature units to °C (default) or °F.
T-COMPENSATION Adds a temperature-dependent correction to the measured value:
• NONE—Temperature compensation not required
• USP—Set the alarm level for the standard USP definition table
• ULTRA PURE WATER—Not available for TDS. Set the compensation type
according to the sample characteristics—Select NaCl , HCl, AMMONIA or ULTRA
PURE WATER
• USER—Select BUILT IN LINEAR, LINEAR or TEMP TABLE:
• BUILT IN LINEAR—Use the pre-defined linear table (slope defined as 2.0%/°C,
reference temperature as 25 °C)
• LINEAR—Set the slope and reference temperature parameters if different from
the built-in parameters
• TEMP TABLE—Set the temperature and multiplication factor points (refer to the
conductivity module documentation)
• NATURAL WATER—Not available for TDS
CONFIG TDS TDS only—changes the factor that is used to convert conductivity to TDS: NaCl
(0.49 ppm/µS) or CUSTOM (enter factor between 0.01 and 99.99 ppm/µS).
CABLE PARAM Sets the sensor cable parameters to improve measurement accuracy when the sensor
cable is extended or shortened from the standard 5 m. Enter the cable length,
resistance and capacitance.
TEMP ELEMENT Sets the temperature element to PT100 or PT1000 for automatic temperature
compensation. If no element is used, the type can be set to MANUAL and a value for
temperature compensation can be entered.
FILTER Sets a time constant to increase signal stability. The time constant calculates the
average value during a specified time—0 (no effect) to 60 seconds (average of signal
value for 60 seconds). The filter increases the time for the sensor signal to respond to
actual changes in the process.
LOG SETUP Sets the time interval for data storage in the data log—5, 30 seconds, 1, 2, 5, 10,
15 (default), 30, 60 minutes.
RESET DEFAULTS Sets the configuration menu to the default settings. All sensor information is lost.
Resin option
Use the RESIN option to view and change the parameters related to the resin cartridge. These
parameters must be defined before the analyzer is used for the first time.
1. Push the menu key and select TEST/MAINT>RESIN.
2. To monitor the status of the resin select the TRACK option and push enter.
Option Description
YES Monitor the resin status. When the life expectancy of the resin is less than 10 days a warning
message is triggered. When the life expectancy reaches 0 days a system error is triggered.
NO The resin is not monitored.
English 19