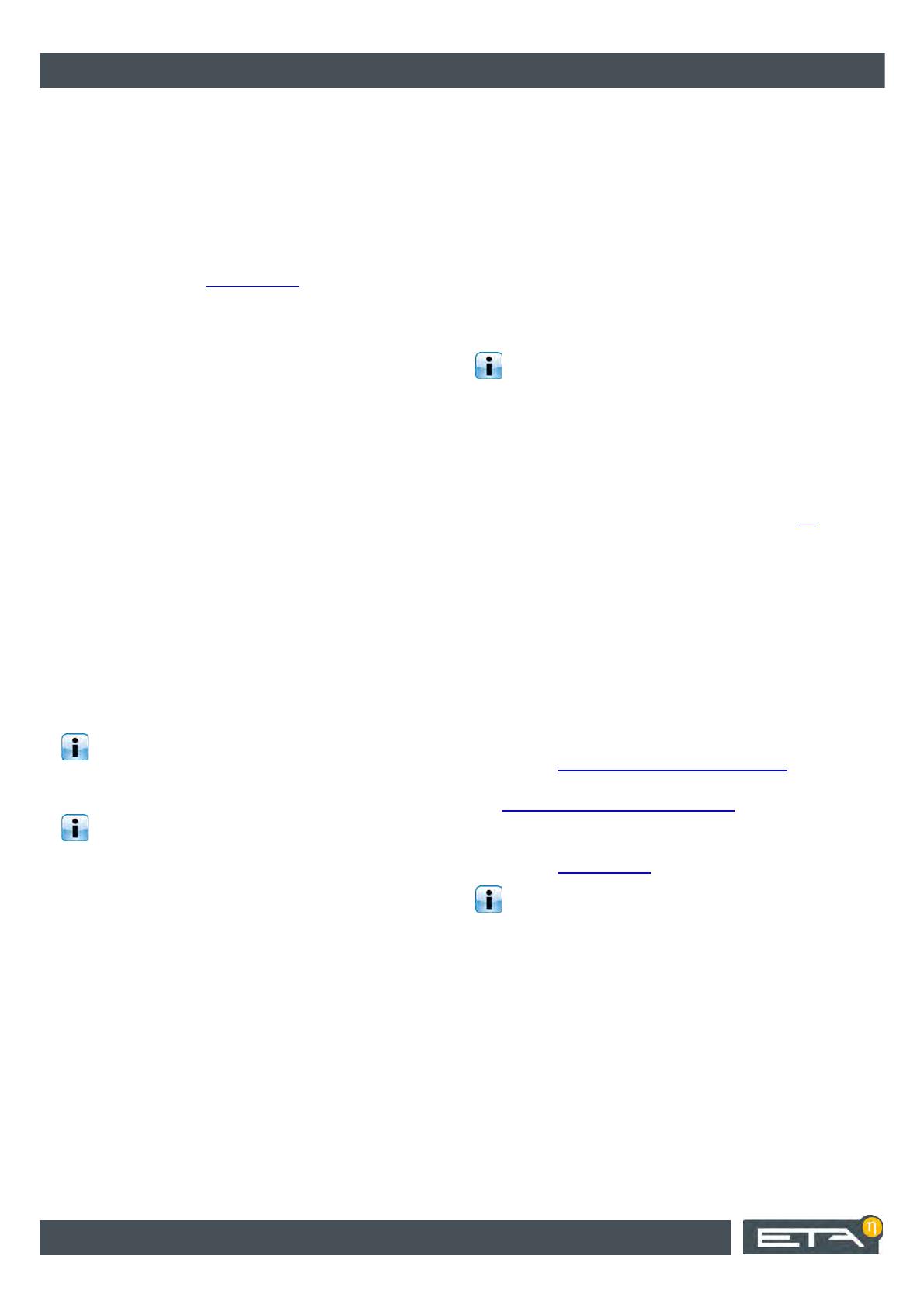
14 www.eta.co.at
Slag Changing the fuel
Setting the fuel type in the control system
The control system provides a selection of different
fuels. For each one different values are stored for the
combustion and de-ashing. If the fuel is changed, the
new fuel must also be set in the control system. If the
water content and density are known, these
parameters must also be adjusted. Changing the fuel,
density and water content in the control system is
described in chapter 6.2.2.1 "
Fuel".
4.1 Slag
What is slag?
Slag is liquified ash of combusted fuel. Liquefaction
occurs when the combustion temperature in the boiler
reaches the ash melting point of the fuel.
Slag clogs the openings in the grate and prevents the
flow of air. As a result, the combustion temperature
increases, which further promotes the formation of
slag. This causes increased wear of the combustion
chamber, the grate, and its de-ashing parts as well as
faults and unnecessary additional maintenance
demands.
How does slag form?
The ash melting point of wood is approximately 1100
°C. The combustion temperature of the boiler (with
good quality wood chips) is approximately 900 °C.
Since the combustion temperature is lower than the
ash melting point of the fuel, no slag will form.
The ash melting point of miscanthus and
impurities like needles, leaves, soil, dirt, and
rotten fuel is approximately 800 °C. Therefore, a high
level of impurities will lead to the formation of slag.
Optional flue gas recirculation is one way to avoid
the formation of slag. Flue gas recirculation
directs a portion of the flue gas back into the
combustion chamber, reducing the combustion tem-
perature. As a result, the ash melting point of the fuel
is no longer reached, greatly reducing the formation of
slag.
Causes of slag
The causes of slag can be divided into the following
categories:
Characteristics of the fuel
• Wood chips and miscanthus containing a high
level of ash, contaminants (soil, sand, stones), a
high proportion of bark or leaves and needles.
• Pellets and bark pellets that contain a high
proportion of ash.
Improper operation and maintenance of the boiler.
• Leaks in the boiler caused by improperly sealed
maintenance openings.
• Unsealed Lambda probe, defective seals on the
ash box, flue gas recirculation.
• Boiler and flue gas recirculation not regularly
cleaned, or flue gas recirculation does not work
due to high flue draught.
Incorrect control system settings
• Incorrect fuel settings
• De-ashing interval too long.
Generally speaking, the darker the wood chips,
the higher the proportion of dirt that will cause
slag.
When the fuel causes slag
If pieces of slag are found in the ash box, then this is
usually caused by the fuel's ash content. Therefore,
the boiler must be de-ashed more often. This is done
by shortening the de-ashing interval; see page 34
.
An excessive flue draught can also cause slag by
reducing the effectiveness of the flue gas recirculation.
If the flue draught is over 15 Pa, a draught limiter is
required, or a nozzle on the chimney opening with
which higher exit velocities and better lift for the flue
gas are achieved.
Remedies for slag
If slag appears, the following measures can be used as
remedies:
• Shorten the de-ashing interval by 50%. See
chapter 6.2.2.3 "
Boiler de-ashing interval".
• Raise the residual oxygen content O
2
. See chapter
6.2.2.6 "
Increase O2 target value".
• Install flue gas recirculation on the boiler
• Check the position of the firebed level sensor. See
chapter 4.2 "
Settings".
In any case, the de-ashing interval must be
adjusted. As an additional measure, the residual
oxygen content can be briefly raised. However, if
would be preferable to change the fuel or to retrofit the
optional flue gas recirculation in order to sustainably
lower the combustion temperature.