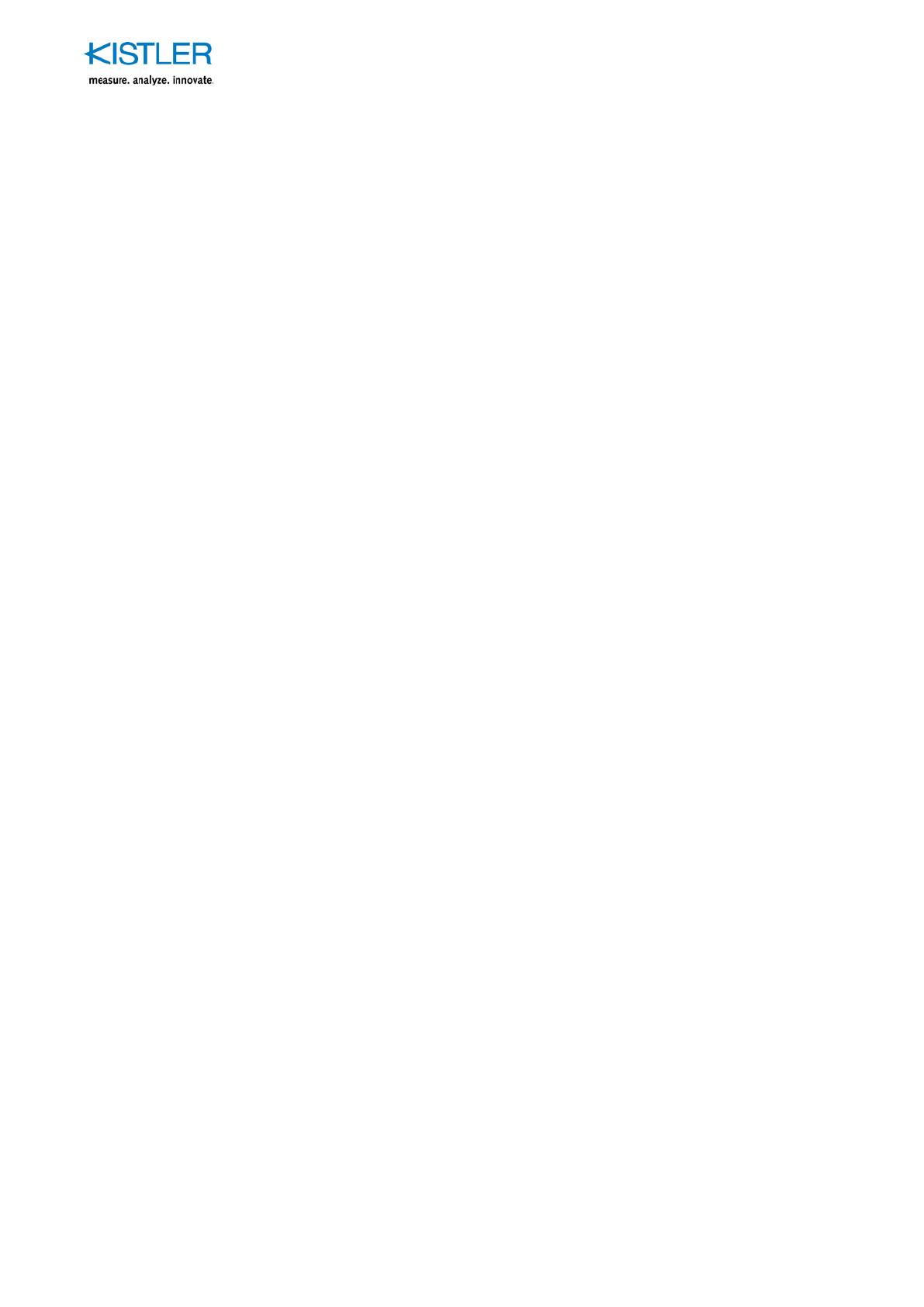
Pressure generator Type 6904A1
Page 2 6904A_002-716e-12.17
Content
1. Foreword ...................................................................................................................................... 3
2. Before you start ........................................................................................................................... 4
2.1 Scope of supply ................................................................................................................... 4
2.2 Safety first ........................................................................................................................... 4
2.3 Golden rules ........................................................................................................................ 4
3. System description ..................................................................................................................... 5
3.1 The selector valve ............................................................................................................... 6
3.2 The spindle .......................................................................................................................... 6
3.3 Sensor mounting ports ........................................................................................................ 7
3.4 Mounting seal configuration ................................................................................................ 7
4. Installation and commissioning ................................................................................................. 8
4.1 Mounting the pressure generator ........................................................................................ 8
4.2 Fitting the lever arms ........................................................................................................... 9
4.3 Check sensor mounting ports ............................................................................................. 9
4.4 Filling the fluid reservoir .................................................................................................... 10
4.5 Purging the system ........................................................................................................... 10
5. Operation .................................................................................................................................... 11
5.1 Mounting sensors .............................................................................................................. 11
5.1.1 Reference sensor ................................................................................................. 11
5.1.2 Unit under test ...................................................................................................... 11
5.2 Priming .............................................................................................................................. 12
5.3 Pressure application .......................................................................................................... 12
6. Appendix .................................................................................................................................... 13
6.1 Dimensions ........................................................................................................................ 13
6.2 Spare parts ........................................................................................................................ 14
6.3 Additional equipment ......................................................................................................... 14
6.4 Calibration fluid.................................................................................................................. 15
Total pages: 15