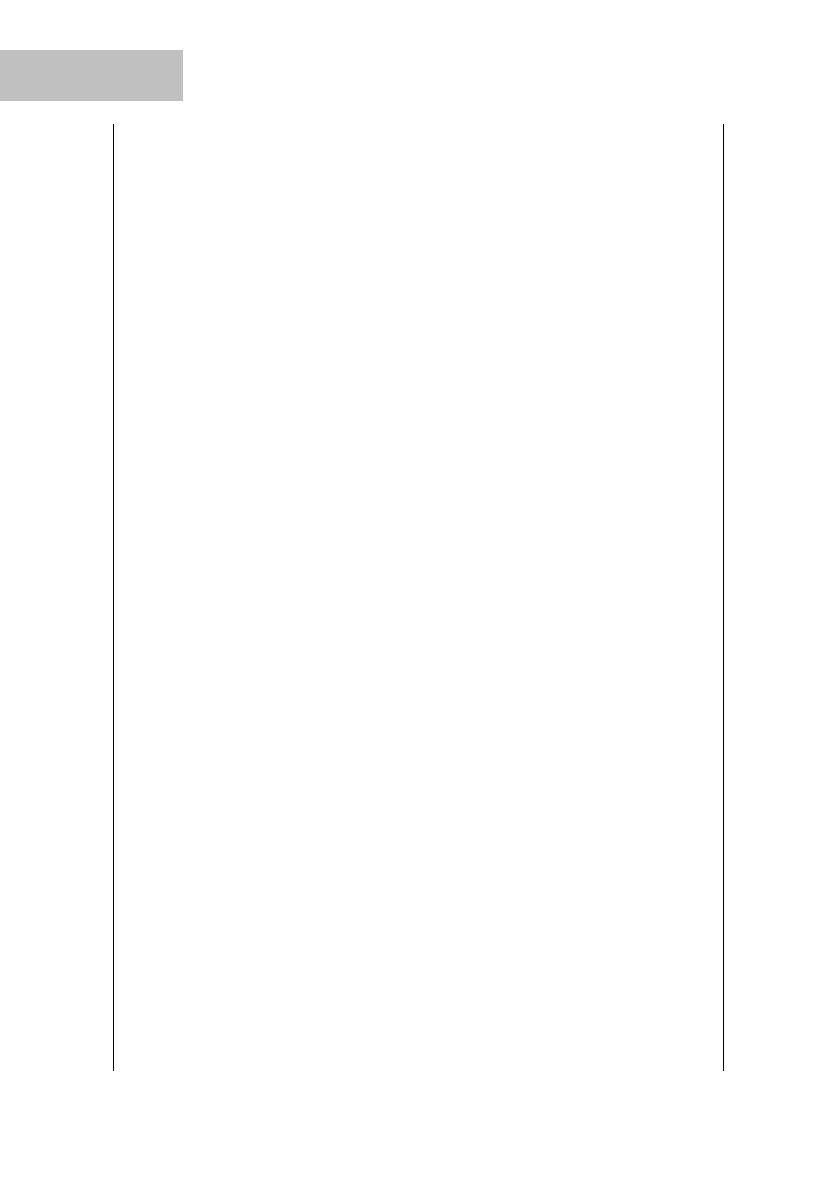
GB LSI
8 008 308/M848/06-05-02 Operating Instructions · LSI
144 © SICK AG · Industrial Safety Systems · Germany · All rights reserved
3. Daily testing of the protective device by authorised and
instructed personnel:
To test your LSI system correctly:
1. The test must be carried out for the relevant preset
monitoring case.
2. Check the mechanical installation to ensure that all
mounting screws are secure and that the PLS is properly
aligned.
3. Check each PLS unit for visible changes, such as damage,
manipulation etc.
4. Switch on the machine/plant.
5. Watch the LEDs on each PLS (red, green, yellow).
6. If at least one LED is not permanently lit when the
machine/plant is switched on, it is to be assumed that there
is a fault in the machine or plant. In this case the machine
must be shut down immediately and checked by a
specialist.
7. Deliberately obstruct the protective field without risk to any
personnel while the machine is running in order to test the
effectiveness of the entire system. The LEDs of each
tested PLS unit must change from green to red and the
hazardous movement must stop immediately. Repeat this
test at different points in the danger area and on all PLS
units. If you discover any non-conformance of this function,
the machine/plant must be shut down immediately and
checked by a specialist.
8. For stationary applications, check that the danger area
marked out on the floor matches the shape of the
protective field stored in the PLS
and that any gaps are
protected by additional safety measures. In the case of
mobile applications, check that the moving vehicle actually
stops at the field limits which are set in the LSI and listed
on the data plate in the vehicle or in the configuration
protocol. If you discover any non-conformance of this
function, the machine/plant/vehicle must be stopped
immediately and checked by a specialist.