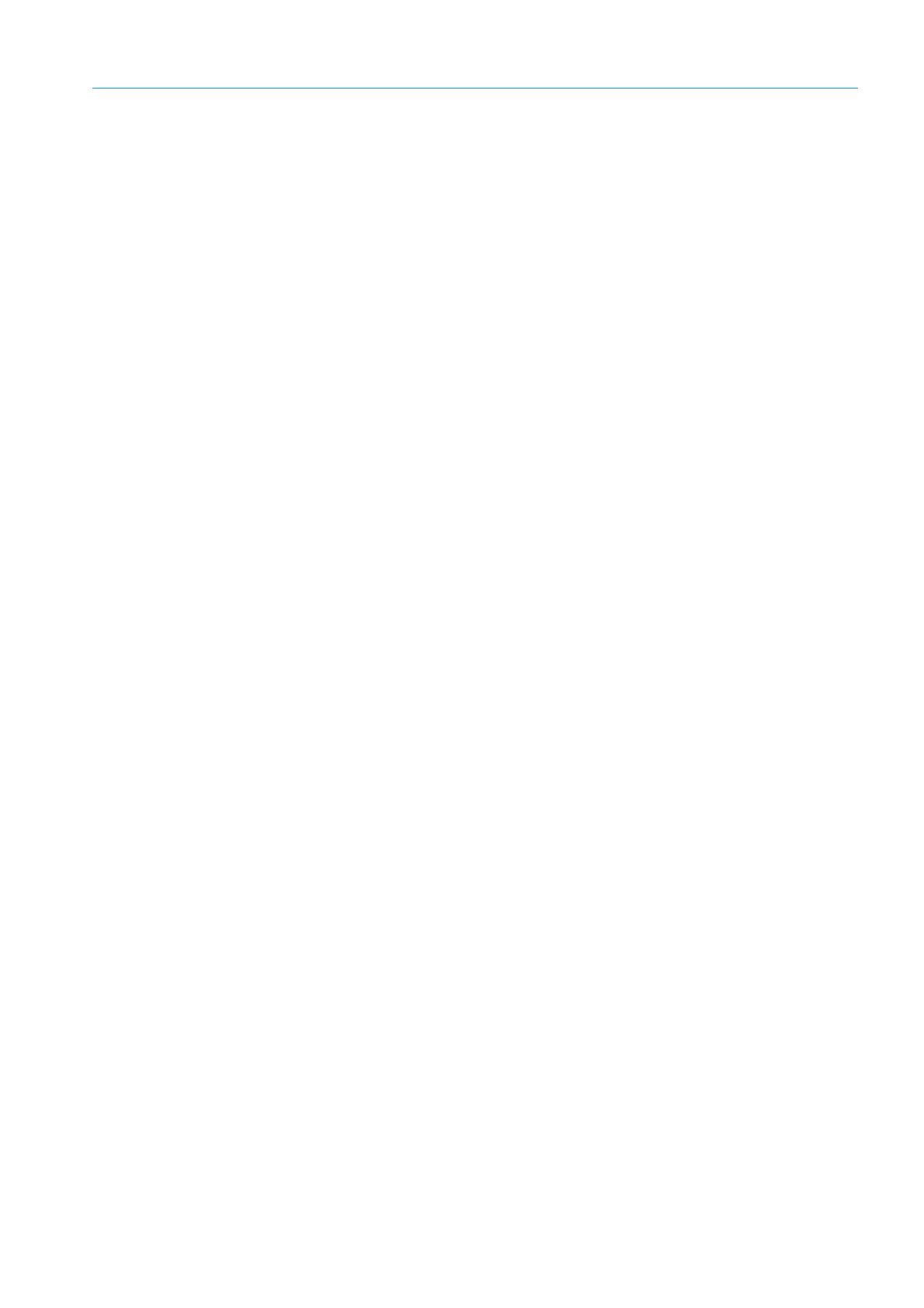
CONTENTS
3
8024019/AE00/V1-0/2019-02 | SICK A D D E N D UM T O O P E R A T I N G I N S T R U C T I O N S | FWE200DH
Subject to change without notice
1 Important information .............................................................................. 4
1.1 About this document....................................................................................... 4
1.2 Main hazards................................................................................................... 4
1.3 Symbols and document conventions ............................................................. 5
1.3.1 Warning symbols ............................................................................ 5
1.3.2 Warning levels and signal words.................................................... 5
1.3.3 Information symbols ....................................................................... 5
1.4 Intended use ................................................................................................... 5
1.5 Responsibility of user...................................................................................... 6
1.5.1 General information........................................................................ 6
2 Product description ................................................................................... 7
2.1 Characteristics and function .......................................................................... 7
2.2 Device components ........................................................................................ 7
2.2.1 Purge air heater .............................................................................. 8
2.2.2 Pressure regulator .......................................................................... 8
2.2.3 Heated extraction hose .................................................................. 9
2.2.4 Water valves and ball valve..........................................................10
2.2.5 Water connection provided by operator ......................................10
2.2.6 Water connections on WBP swirl chamber cover........................10
3 Commissioning / configuring ................................................................12
3.1 Temperature setting of the heating bands ..................................................12
3.2 Connecting the heated extraction hose (optional) ......................................13
3.3 Connecting the purge air heater...................................................................14
3.4 Setting parameters .......................................................................................16
3.4.1 Activating temperature control / heated extraction hose...........16
3.4.2 Configuring the purge air heater ..................................................17
3.4.3 Standard configuration flowchart ................................................19
4 Maintenance.............................................................................................21
4.1 General information ......................................................................................21
4.2 Replacing the water filter..............................................................................21
4.3 Leak test of the water circuit........................................................................22
4.4 Checking the spray pattern...........................................................................23
5 Malfunction messages............................................................................24
6 Repair work ..............................................................................................25
6.1 Replacing the WBP control block .................................................................25
6.2 Replacing the WBP ball valve .......................................................................26
7 Technical data ..........................................................................................27
7.1 Optional components....................................................................................27
7.2 Spare parts / consumables ..........................................................................27
Contents
Contents