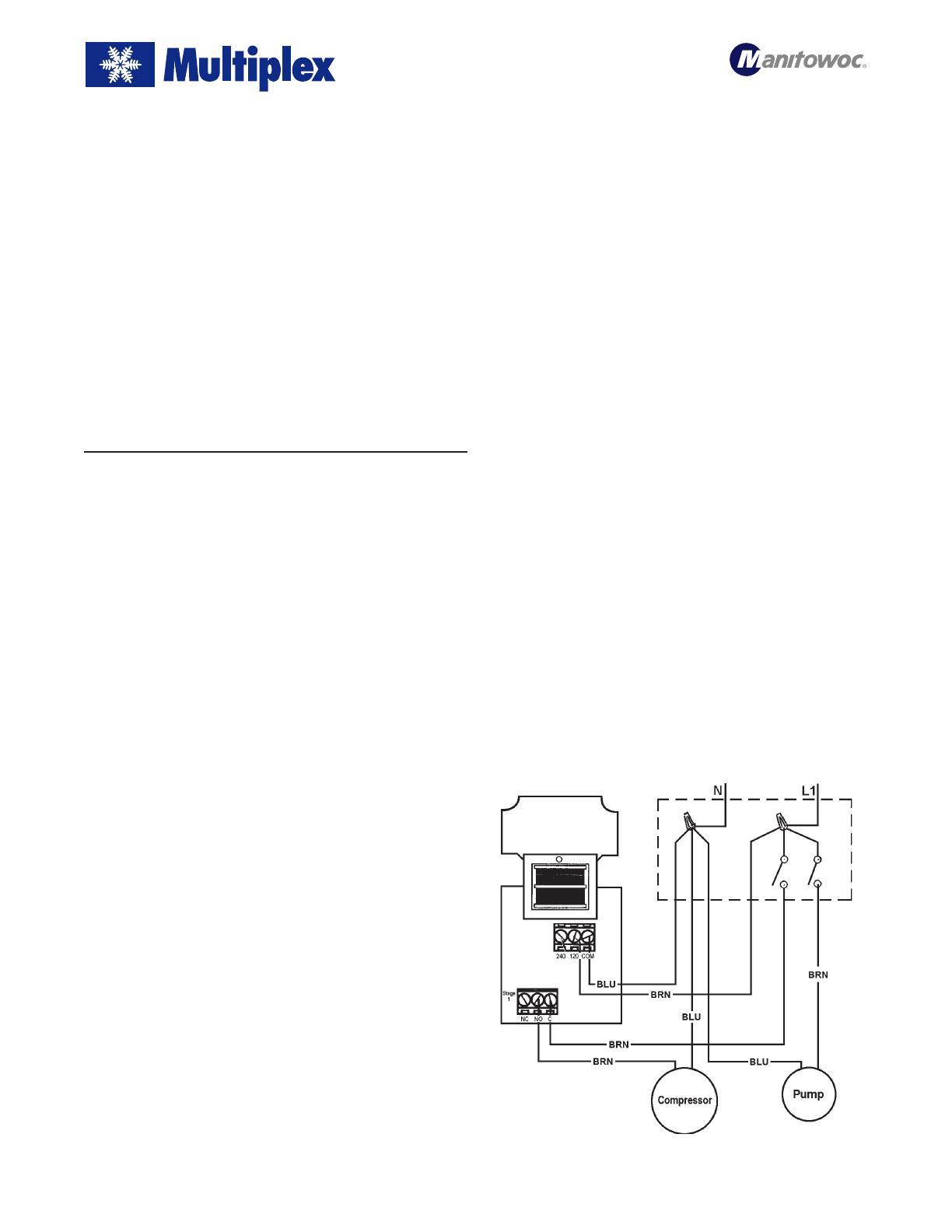
In accordance with our policy of continuous product development and improvement,
this information is subject to change at any time without notice.
EI219360 Issued (JMT/KAK) 6 March, 2001
Manitowoc Beverage Equipment
2100 Future Drive Sellersburg, IN 47172-1868
Tel: 812.246.7000, 800.367.4233 Fax: 812.246.9922
www.manitowocbeverage.com
Foodservice Group
Multiplex Beverage Equipment Installation Instructions for
Electronic Temperature Control Retrofit Kit
for Model 75 Beermaster Glycol Chiller
P.N. 00219360
This kit is designed to replace the existing Ranco mechani-
cal temperature control in a Multiplex Model 75 Beermaster
Glycol Chiller. The Electronic Temperature Control (ETC) is
mounted under the top cover of the Model 75 Beermaster Gly-
col Chiller and provides a constant display readout of the sen-
sor temperature. It will be readily visible by lifting the top
cover of the unit.
Installing the electronic temperature
control retrofit kit
Tools Required
Screwdriver,
5
/32" Tip
Screwdriver,
1
/4" Tip
Screwdriver, #2 Phillips
Nut Driver,
5
/16"
Wire Cutter/Stripper
Installation
1. Turn “off” all control switches on unit.
2. Disconnect electrical power at branch circuit disconnect.
For cord-connected units, simply unplug the power cord.
3. Remove the cover panel from unit.
4. Remove the access panel from switch/control box.
5. Remove cover from temperature control mounted to bulk-
head.
6. Loosen two (2) terminal screws and disconnect both brown
wires.
7. Pull wires back through hole in bottom of control.
8. Cut the terminal connectors off the brown wires and strip
the wire ends
5
/16". Note that one (1) of the wires is at-
tached to one (1) of the control switches and the other
wire is routed to the refrigeration compressor.
9. From the opposite side of the bulkhead, loosen and re-
move two (2) screws that secure the temperature con-
trol. Remove the temperature control from the unit.
10. Position the ETC assembly where the holes in the rear
flange of the mounting bracket align with the holes in the
bulkhead, and the holes in the mounting bracket front
flange align with the two (2) holes in the front flange of
the motor shelf.
11. Secure the ETC assembly with two (2) #10 Phillips head
screws through the bulkhead holes, and with two (2) #10
hex head screws into the motor shelf.
Note: The screws into the motor shelf are self-threading
screws. Use a 5/16" nut driver to install.
12. Route the blue and brown wires extending from the ETC
into the switch/control box via the wire opening in the
bottom of the box.
13. Disconnect the two (2) wire nuts, add the blue and brown
wires to their respective wire groups, and reconnect the
wire nuts.
14. Loosen the four (4) screws in the ETC cover and open the
ETC.
15. Route the two (2) newly stripped brown wires formerly
connected to the old temperature control through the
opening in the end of the ETC.
16. Insert the stripped end of the wire from the control switch
into opening marked “C” of the ETC lower terminal block.
Tighten the pressure screw to secure the wire.
17. Insert the other stripped wire end into the adjacent open-
ing, marked “NO”. Tighten the pressure screw to secure
the wire.
18. Replace the cover on the ETC and temporarily secure by
partially starting two (2) diagonal screws (the cover will
be removed again later).
19. Route the sensor cord through an opening in the bulkhead
to the glycol tank
20. Using cable ties, secure the sensor to the bracket attached
to the evaporator.
21. Attach the cover plate to the switch/control box.