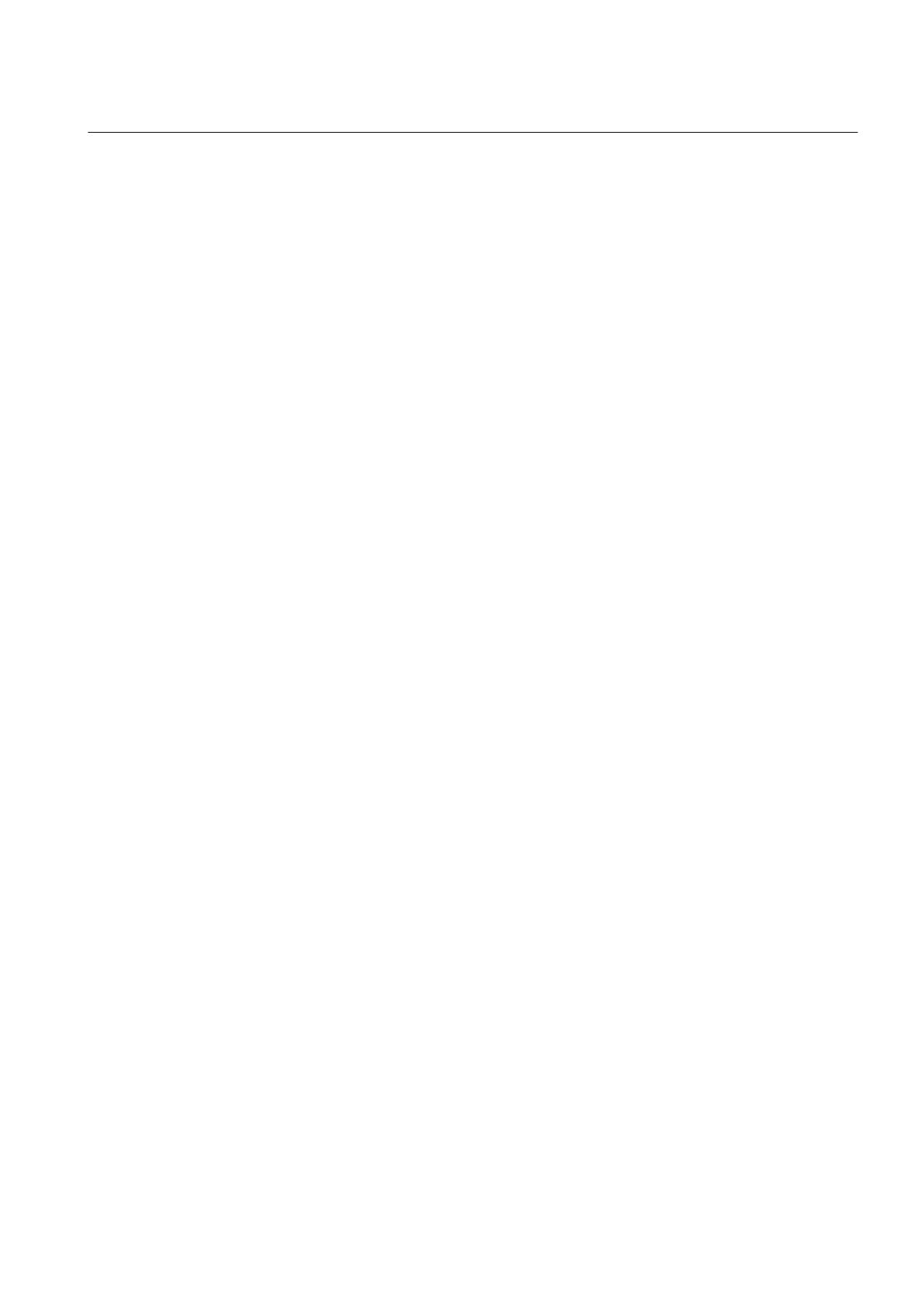
Table of contents
Section 1 Introduction.......................................................................3
This manual........................................................................................ 3
Intended audience.............................................................................. 3
Product documentation.......................................................................4
Product documentation set............................................................4
Document revision history............................................................. 4
Related documentation..................................................................5
Symbols and conventions...................................................................5
Symbols.........................................................................................5
Document conventions.................................................................. 5
Section 2 IEC 60870-5-103 overview...............................................7
IEC 60870-5-103 standard................................................................. 7
Documentation................................................................................... 8
Section 3 Vendor-specific implementation....................................... 9
Product series implementation........................................................... 9
Communication link............................................................................ 9
Communication link setup........................................................... 10
Diagnostic counters..................................................................... 11
IEC 60870-5-103 process data.........................................................12
IEC 60870-5-103 data objects.....................................................12
Indications................................................................................... 12
ASDU 2 type fault number and relative time data.................. 13
Configuring of IEC 60870-5-103 indications...........................13
Class 1 event overflow........................................................... 14
Chronology of Class 1 events................................................ 14
Class 1 data message priorities............................................. 15
LED objects............................................................................ 15
Analog events..............................................................................16
Configuring of analog events..................................................16
Value interpretation................................................................ 17
Controls....................................................................................... 17
Circuit breaker control model................................................. 17
Local, Remote, Station, All and Off states..............................17
Control operation rejections................................................... 18
Measurands.................................................................................18
Class 2 measurands...............................................................18
Other Class 2 measurand frames.......................................... 19
Selection of Class 2 frame..................................................... 20
Table of contents
615 series 1
Communication Protocol Manual