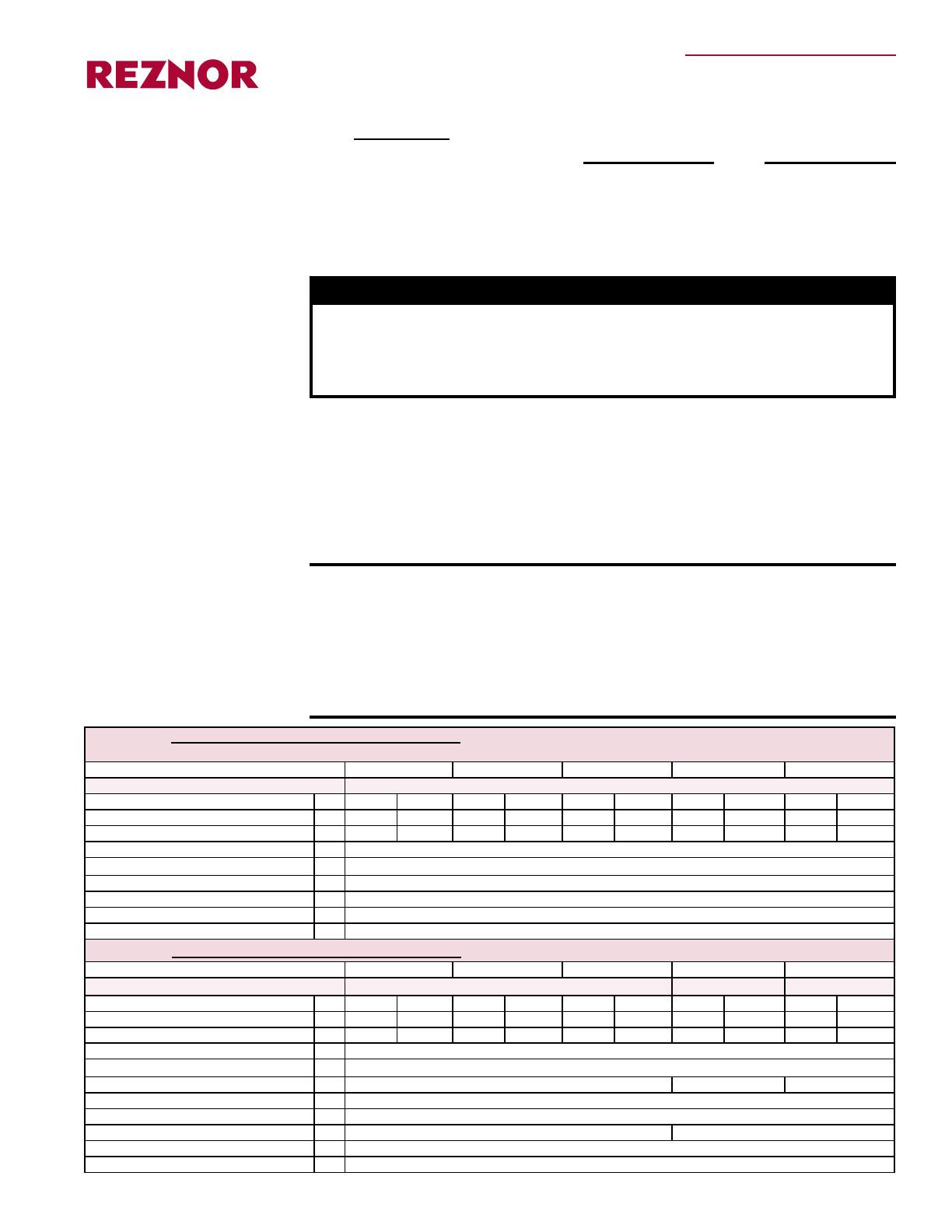
Form CP-MAPS II-GC (01-15), P/N 209417R4, Page 1
Applies to: Gas Heat Section Sizes 100, 150, 200, 250,
and 300 on MAPS
®
II Model RDCA and Model RDDA
Form CP-MAPS II-GC (01-15)
Obsoletes Form CP-MAPS II-GC (Version A)
All gas conversion must be done by a qualied service person in accordance with
these instructions and in compliance with all codes and requirements. In Canada, gas
conversion shall be carried out in accordance with the requirements of the Provincial
Authorities having jurisdiction and in accordance with the requirements of the CAN/
CGA-B149.1 and .2 installation code.
WARNING
Improper installation, adjustment, alteration, service, or
maintenance can cause property damage, injury, or death.
For assistance or additional information, consult a qualied
installer, service agency, or the gas supplier.
Application and Kit
Selection
HAZARD INTENSITY LEVELS of Warnings
1. DANGER: Failure to comply will result in severe personal injury or death
and/or property damage.
2. WARNING: Failure to comply could result in severe personal injury or
death and/or property damage.
3. CAUTION: Failure to comply could result in minor personal injury and/or
property damage.
The gas conversion kits in these instructions are for an optional heat section (Sizes
100-300) of MAPS
®
II Model RDCA packaged cooling/heating and MAPS
®
II Model
RDDA cooling/reheat/heating systems. (NOTE: For converting larger heat section
sizes, contact the factory service department.)
Natural gas heat sections have either three-stage heating or modulating heating con-
trol. Propane fueled heat sections are only available in three-stage heating.
Verify that the kit being used is the appropriate one for the installation.
Comply with all warnings and follow the instructions carefully.
Components - Gas
Conversion Kits for
MAPS
®
II Models
RDCA and RDDA
with Gas Heat
Sizes 100 - 300
Gas Conversion Kits and Instructions
TABLE 1A - Natural Gas TO Propane Conversion Kits (NOTE: If equipped with Option AG57, 6:1 modulating gas
control, modulation must be disabled before gas conversion. Follow instructions on page 2.)
Gas Section Capacity (MBH) / Size 100 150 200 250 300
Conversion Kit P/N 269845
Description of Component Qty P/N Marking P/N Marking P/N Marking P/N Marking P/N Marking
Gas Orice for small burner section 1 205862 1.7 mm 124967 2.1 196852 #39 196853 #37 205720 2.9 mm
Gas Orice for larger burner section 1 205859 3/32 205860 2.9 mm 205716 3.3 mm 205717 3.75 mm 205718 4.1 mm
Gas Valve Conversion Spring Kit 2 98720, Honeywell #393691, for VR8105, VR8205, & VR8305 Single-Stage Valves
Gas Valve Conversion Spring Kit 2 260605, Honeywell #396221 for a VR8215 Single-Stage Valve (replacement valve)
Propane Conversion Disk 1 37752
Sheetmetal Screw (for attaching disk) 1 11813
Conversion Kit Tape 1 64391 (ll out and adhere near to heat section rating plate)
High Altitude Adjustment Label 1 197062 - Use if elevation is above 2000 ft (610M).
TABLE 1B - Propane TO Natural Gas Conversion Kits (3-stage system only)
Gas Section Capacity (MBH) / Size 100 150 200 250 300
Conversion Kit P/N 269859 209418 209419
Description of Component Qty P/N Marking P/N Marking P/N Marking P/N Marking P/N Marking
Gas Orice for small burner section 1 205863 2.75mm 120146 3.4mm 120152 #23 205719 4.4MM 120158 #10
Gas Orice for larger burner section 1 205857 #23 205858 #12 205713 7/32 205714 6.2MM 205715 6.9MM
Gas Valve Conversion Spring Kit 2 98721, Honeywell #394588, for VR8105, VR8205, & VR8305 Single-Stage Valves
Gas Valve Conversion Spring Kit 2 261651, Honeywell #396222 for a VR8215 Single-Stage Valve (replacement valve)
Secondary Combustion Air Restrictor 2 N/A 205492 205493
Natural Gas Conversion Disk 1 1401
Sheetmetal Screw (for attaching disk) 1 11813
Sheetmetal Screws (for restrictors) 8 N/A 11813
Conversion Kit Tape 1 64391 (ll out and adhere near to heat section rating plate)
High Altitude Adjustment Label 1 197062 - Use if elevation is above 2000 ft (610M).