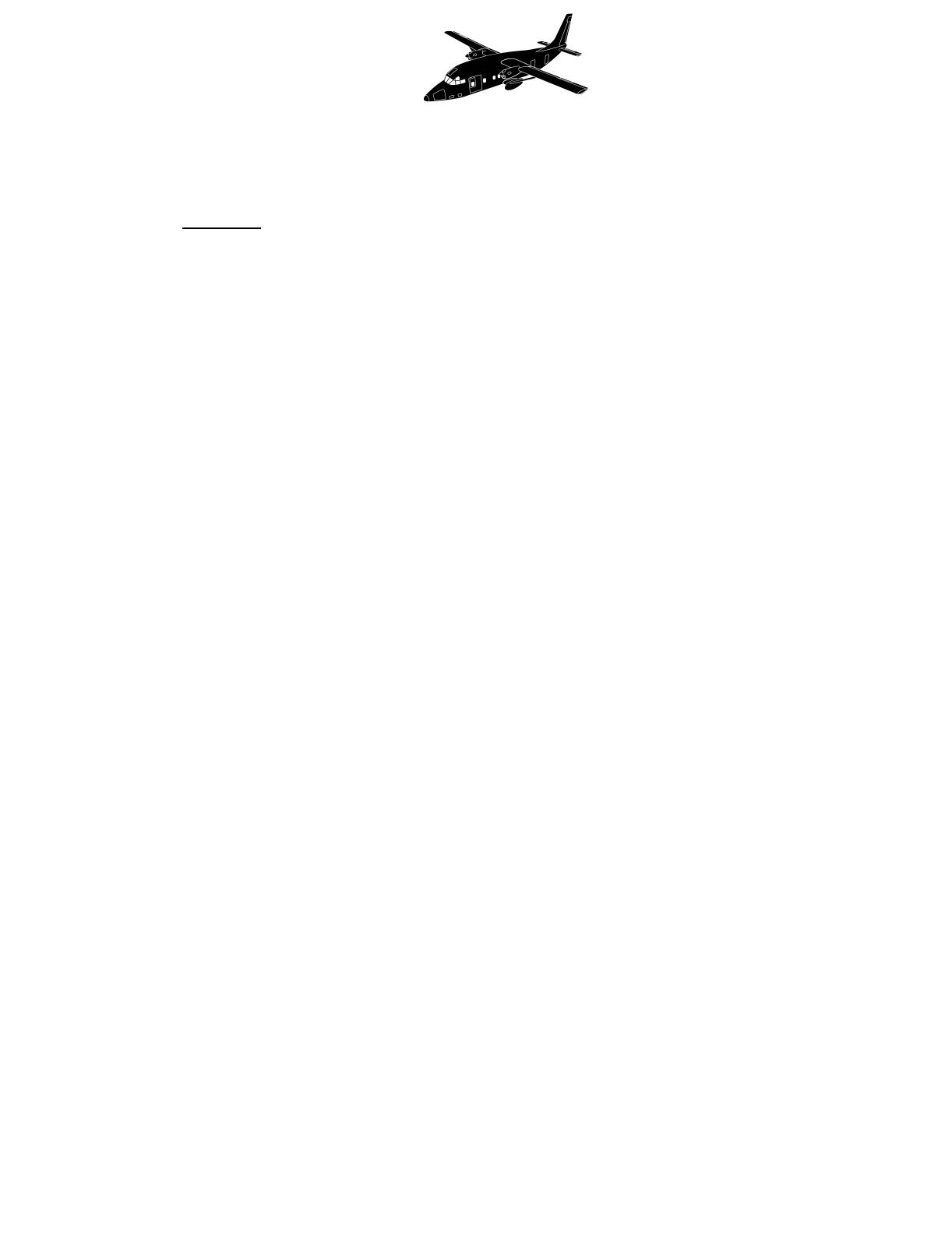
Jun 30/01
30-11-36
Page 203
EFFECTIVITY:
All
z
SD3-60 AIRCRAFT MAINTENANCE MANUAL
D. Adhesion reduction
(1) ICEX application
WARNING: FAILURE TO FOLLOW DIRECTIONS COULD RESULT IN BODILY INJURY OR
DEATH. HARMFUL VAPOURS MAY CAUSE SKIN AND EYE IRRITATION. USE
ONLY IN A WELL VENTILATED AREA. TO AVOID PROLONGED OR REPEATED
SKIN CONTACT, USE RUBBER OR NEOPRENE GLOVES (INDUSTRIAL/
ALKALINE RESISTANT TYPE). WEAR CHEMICAL GOGGLES. WHEN
CONTAINER IS NOT IN USE, KEEP IT TIGHTLY CLOSED TO AVOID
EVAPORATION. KEEP AWAY FROM OPEN FLAMES AND ELECTRIC
HEATERS. DO NOT DISPOSE OF EMPTY CONTAINER BY BURNING.
BURNING GIVES OFF TOXIC SUBSTANCES. IF THERE IS EYE CONTACT,
FLUSH WITH WATER FOR 15 MINUTES. USE SOAP AND WATER AFTER SKIN
CONTACT. IF EYE OR SKIN IRRITATION PERSISTS, SEE A PHYSICIAN. IF
SWALLOWED, DO NOT INDUCE VOMITING. SEE A PHYSICIAN IMMEDIATELY.
KEEP OUT OF REACH OF CHILDREN.
B.F. Goodrich ICEX is a silicone based material specifically compounded to reduce the
strength of adhesion between ice and the rubber surfaces of the aircraft de-icers. ICEX
will not harm rubber and offers added ozone protection.
Properly applied and renewed at periodic intervals, ICEX provides a smooth polished
film that evens out the microscopic irregularities on the surface of the rubber parts. ICEX
provides a barrier to ice adhesion and causes ice to shear easily when the de-icers are
operated.
One quart will provide 500 square feet coverage when applied as directed.
ICEX may be applied directly over AGE-MASTER No. 1 treated surface, so long as the
AGE-MASTER No. 1 has dried for 24 hours and is clean. Otherwise:
(a) Thoroughly wash using soap and water solution.
(b) Remove substances which cannot be removed by soap and water using isopropyl
alcohol; however if this is done the surface must be cleaned again with soap and
water.
(c) Rinse thoroughly with clean water and allow to dry.
ICEX should be applied sparingly to achieve the optimum results. If the application is too
heavy, it will cause the surface to become sticky, thus attracting runway dust and
reducing ice removing efficency.
The frequency of application will be dependent upon the number of flight hours
accumulated and the type of weather encountered. One application of ICEX may be
expected to last for 50 flight hours during the icing season. Re-apply as often as required
to maintain a thin polished film on the de-icer surfaces.