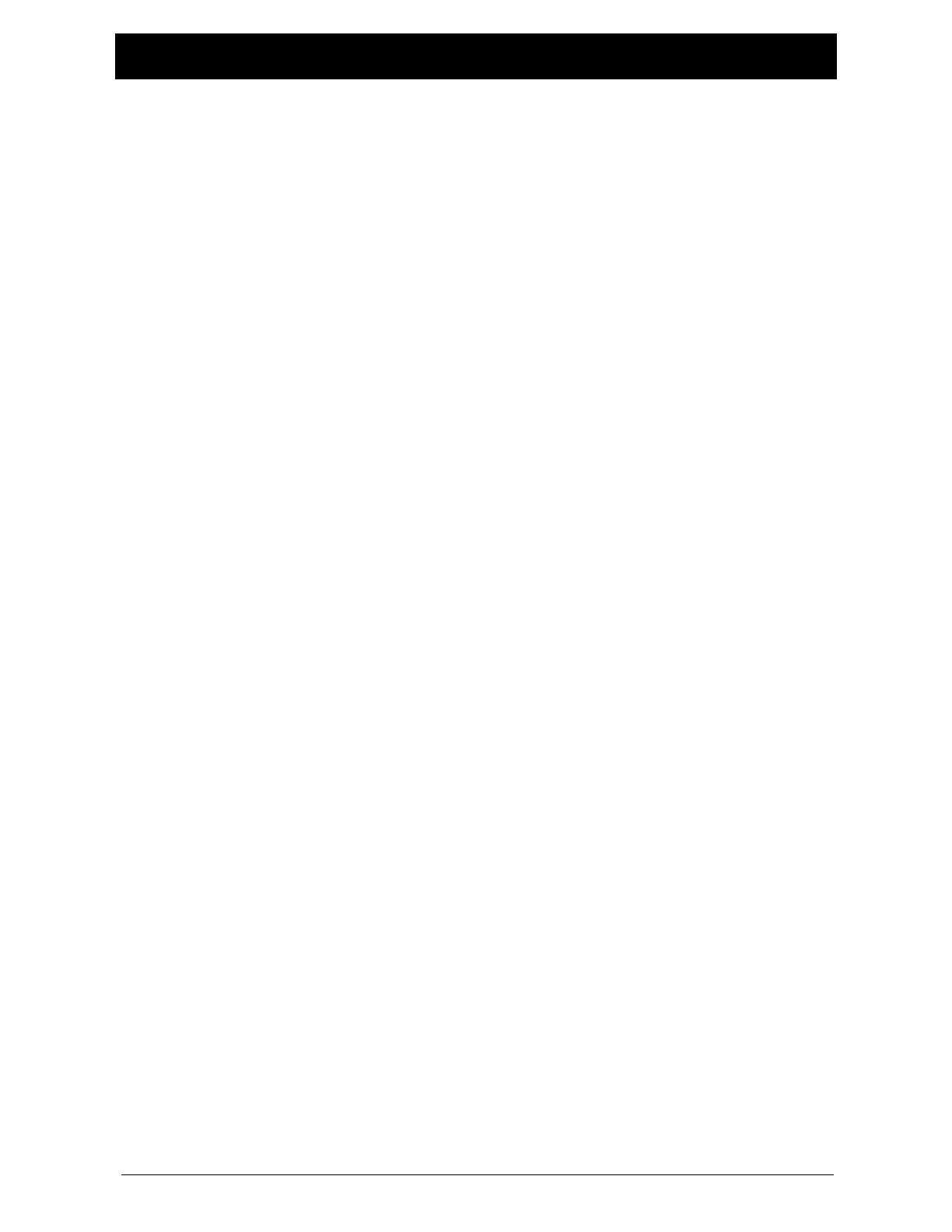
www.maxcessintl.com FIFE-500 MI 1-915 1 E
INTRODUCTION .................................................................................... 1-1
About these operating instructions .......................................................................... 1-1
CE marking .............................................................................................................. 1-1
Product overview ..................................................................................................... 1-2
SAFETY INSTRUCTIONS .......................................................................... 2-1
Instructions for use .................................................................................................. 2-1
Safety symbols ......................................................................................................... 2-1
Symbols used........................................................................................................... 2-2
Basic safety information ........................................................................................... 2-3
INSTALLATION ...................................................................................... 3-1
Mechanical installation ............................................................................................ 3-1
Mounting dimensions ..................................................................................... 3-2
Pneumatic connection to splice table .............................................................. 3-3
Installing the operator interface ............................................................................... 3-4
Relocating the operator interface.................................................................... 3-4
Panel mount model ......................................................................................... 3-5
Wall mount model .......................................................................................... 3-6
Electrical installation ................................................................................................ 3-7
Power connection ........................................................................................... 3-7
Digital inputs and outputs .............................................................................. 3-8
Wiring diagrams ........................................................................................... 3-11
MAINTENANCE ...................................................................................... 4-1
Sensors ........................................................................................................... 4-2
Operator interface screen ............................................................................... 4-2
MODEL NUMBER KEY ............................................................................. 5-1
SPECIFICATIONS .................................................................................... 6-1
General .................................................................................................................... 6-1
Certifications and environmental compatibility ........................................................ 6-1
Inputs and outputs .................................................................................................. 6-2
Maximum cable lengths ........................................................................................... 6-2
SERVICE AND REPLACEMENT PARTS ........................................................ 7-1