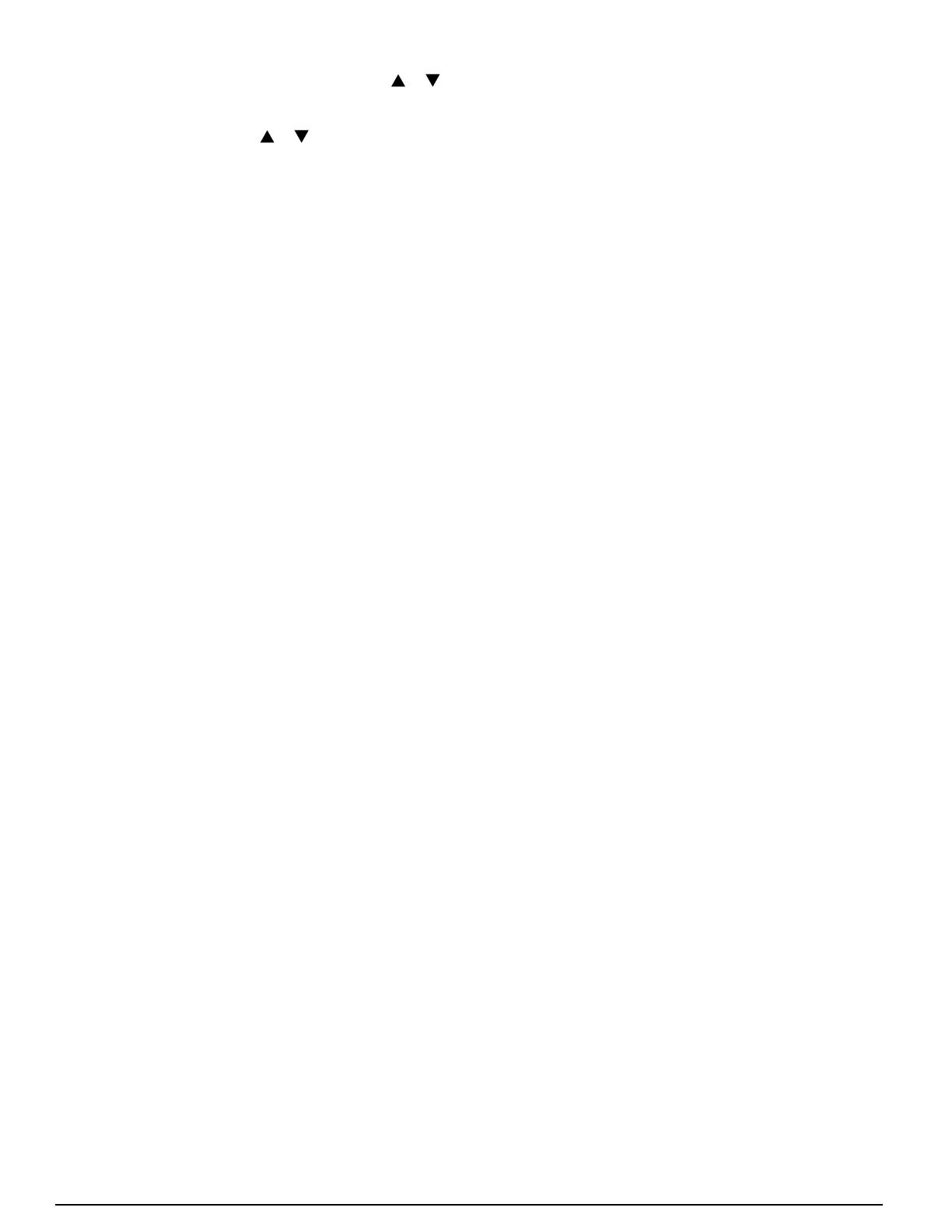
15
5. ForsystemswithoutiQZone,adjusttheoperatingsetpoint
if desired using a temporary hold (pressing the or key
whentheMainScreenisdisplayed).WithiQZone,zone
control enabled, adjust the operating setpoint for each zone
individually by touching the or icon.(RefertoiQZone
SystemZoneThermostatUser’sManualfordetails.)
System Startup Checkout & Troubleshooting
The following is a summary of the sequence for typical first
operationto check out the system. Referenceis made to
INSTALLER SETTINGS and SERVICE INFORMATION
described above.
1. Install system hardware as described in the individual
component installation instructions.
2. Install power and control wiring to all system components,
including the controller, in accordance with the iQ Field
Wiring Installation Instructions.
3. Perform pre-charge evacuation of field-installed refrigerant
lines as described in preceding sections.
4. ForiQZonesystems,rstapply12voltdcpowertothe
zonecontrolboardwiththeprovidedAC/DCconverter.Apply
electrical power to the system (including the heat pump).
Thecontrollerscreendisplaybacklightshouldcomeon,
and the “iQ” splash screen should appear. If it does not,
tracethe24vaccontrolpowertothe“R”terminalonthe
thermostat.CONFIGURATIONNEEDEDshouldappear
onthetoplineoftheMainScreen(unlessthethermostat
had been previously used on a similar iQ system).
5. ProceedwithSystemCongurationfromtheINSTALLER
SETTINGS menu (described above). On the SYSTEM
CONFIGURATIONscreenverifythattheusingsize(2ton,
3ton,or4ton)iscorrectasindicated.Ifthewrongvalue
isshown,theinvertermayrequirere-initialization.Contact
the service representative of the distributor in this case.
Onthesamescreen,theentriesunderCOMMUNICATION
should be followed by “OK”. If “CHECK” appears for a
communicationitem,gototheCOMMUNICATIONSTATUS
screen(intheSERVICEINFORMATIONmenu,described
above), and view which elements are not communicating.
Traceandcheckthethreecommunicationwiresthroughout
the system. If isolating a communication problem proves to
be difficult, it may be useful to disconnect all communication
wiresexceptthosewhichlinkthethermostatandthenon-
communicating element.
6. IfCOMMUNICATIONSTATUSwasnotcheckedduringthe
previousstep,checkitatthistime.Alllisteditemsshould
showastatusof“OK”.Ifanyshow“BAD”,determinethe
source of the problem as indicated in the previous step,
and resolve.
7. ForiQZonesystemsonly,themainscreenshouldappear
with no temperature reading, and“ZONE CTRL”should
appearbelow“OFF”.Ifthisisnotthecase,gototheZONE
CONTROLscreenfromtheSETTINGSmenu,andchange
thezonecontroloptiontoENABLE.IfZONECONTROL
does not show up on that menu, the iQ controller has never
communicated with the zone control board, and power and
communication wiring to the zone control board need to be
checked.Ifthemainscreenrevertstobacktothezoning-
disabled screen (showing room temperature), power and
communication wiring to the zone control board need to
bechecked.
8. Set date and time as described above. This will provide a
“time stamp” for any fault which may arise during system
checkout.
9. Iftheinstallationincludesanewgasfurnace,checkout
its operation first. This may be best accomplished from
FURNACE TESTS under SERVICE TESTS from the
INSTALLERSETTINGSmenu(seeabove).Followsteps
instructionsprovidedinthefurnace’sinstallationinstructions.
Besuretoverifybloweroperationduringthetest.
10.Iftheoutdoortemperatureisabove60°F(14°C),testthe
refrigerant system running in cooling mode first. If the
outdoortemperatureisbetween12°and60°F(-11and
14°C),testtherefrigerantsystemrunninginheatingmode
rst.ThismaybestbeaccomplishedfromCHARGEMODE
underSERVICETESTSfromtheINSTALLERSETTINGS
menu. Follow the refrigerant charge adjustment procedure
explained above. Note that if a fault is determined in the
outdoorequipment,thebackupheatingmeans(electric
strip heat or gas furnace) will start instead.
11. When charge adjustment is completed (if required), run
the heat pump in both cooling and heating modes. This
mayalsobedoneusingSERVICETESTSalthoughsome
diagnostic messages are disabled in that method.
12.Check the FAULT STATUS screen (described above)
for any faults logged during the startup process. Any
messagelistedas“ACTIVEFAULT”referstoacondition
whicheitherstillexistsoroccurredwithinthepreceding5
minutes. Every fault or notification should appear in the
FAULTHISTORYlogwhichstartsonthesamescreen.
The last 10 faults to have occurred are retained in this
list. Each new item pushes other logged faults down in
the list. The second line associated with each of the 10
entries includes the time and date of detection. While
the wording of fault messages is intended to provide a
reasonable indication as to the responsible condition, the
information conveyed by the abbreviated wording is limited.
Consequentlytheinstallershouldrefertotrainingliterature
for further information in understanding fault messages.
13.Ifneeded,makeuseofinformationprovidedbelowunder
Troubleshooting: What to Expect with Normal Operation.
14.Independently conrm operation of any accessories
installed with the heat pump system following instructions
provided with that equipment.
15.Complete the remainder of conguration settings and
entries as specified above under Installer Settings and
OtherCongurationEntries.
16.ForiQZonesystems,conrmthezonesystemsetupby
checkinginformationonthe ZONING DATA and ZONE
MODULESTATUSscreens,accessedfromtheSERVICE
INFORMATIONmenu.(SeeSYSTEMDIAGNOSISAND
TROUBLESHOOTINGbelow.).