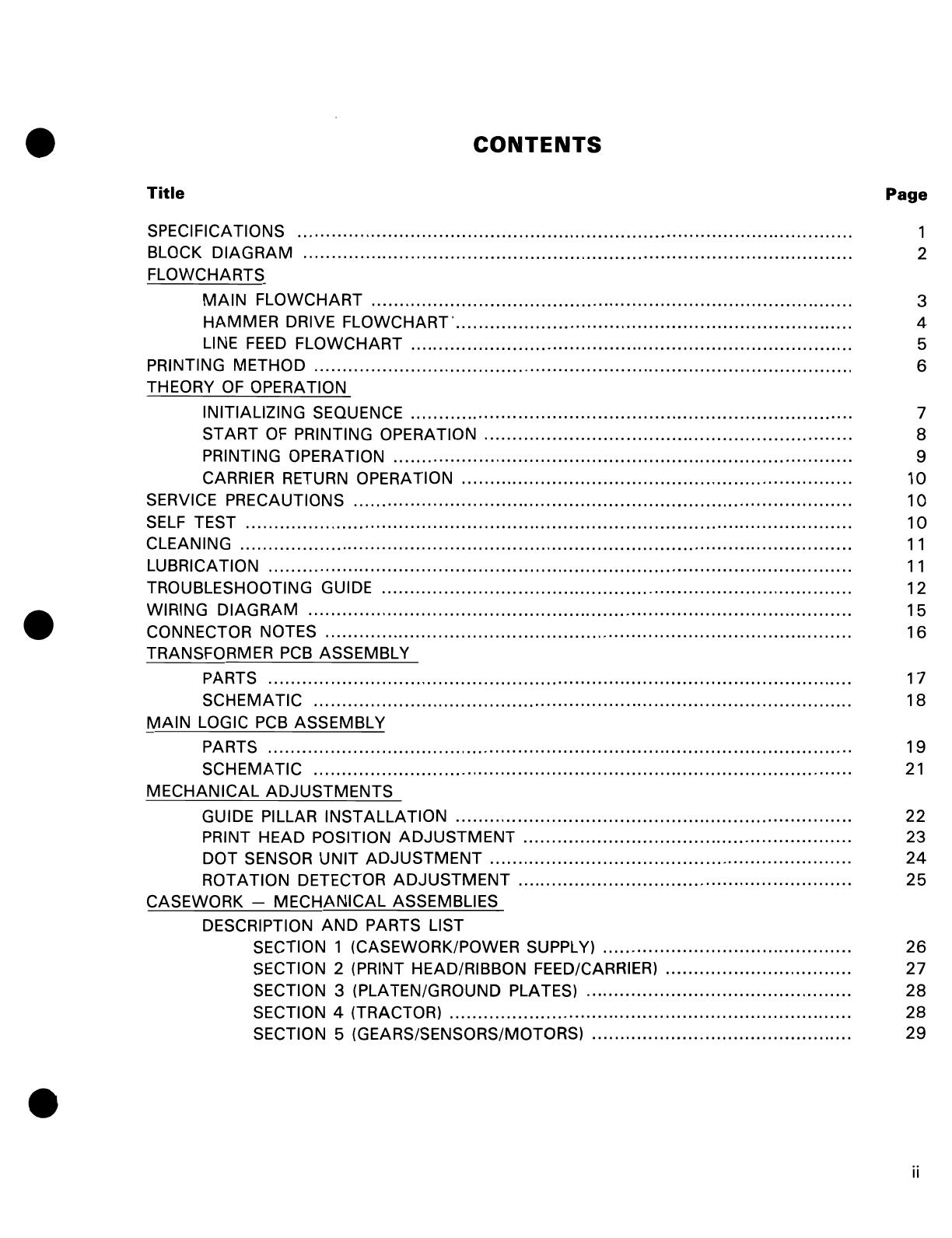
CONTENTS
Title
Page
SPECIFICATIONS
..................................................................................................
1
BLOCK DIAGRAM .....
............................................................................................
2
FLOWCHARTS
MAIN
FLOWCHART
.....................................................................................
3
HAMMER DRIVE
FLOWCHART·......................................................................
4
LINE
FEED
FLOWCHART
......
....
...................................
.................................
5
PRINTING METHOD
........
.................
....
..........................
.................................
.......
6
THEORY
OF
OPERATION
INITIALIZING SEQUENCE
.......
......................................
....
.............................
7
START
OF
PRINTING OPERATION
.........................
........................................
8
PRINTING OPERATION
.................................................................................
9
CARRIER RETURN OPERATION
.....................................................................
10
SERVICE
PRECAUTIONS.
..................................
.....................................................
10
SELF
TEST
...........................................................................................................
10
CLEANING
............................................................................................................
11
LUBRICATION
.......................................................................................................
11
TROUBLESHOOTING GUIDE
............
.....
..............................
...
........
.........................
12
WIRING DIAGRAM
.........
..................
.........................
...............
.............................
15
CONNECTOR NOTES
........
...
..............
.........
..................
......
...................................
16
TRANSFORMER
PCB
ASSEMBLY
PARTS
.......................................................................................................
17
SCHEMATIC
...............................................................................................
18
MAIN
LOGIC
PCB
ASSEMBLY
PARTS
.......................................................................................................
19
SCHEMATIC
...............................................................................................
21
MECHANICAL
ADJUSTMENTS
GUIDE PILLAR INSTALLATION
......................................................................
22
PRINT HEAD POSITION
ADJUSTMENT
.......................
.........
..........
................
23
DOT SENSOR UNIT
ADJUSTMENT
........................
..............
..........................
24
ROTATION DETECTOR
ADJUSTMENT
...........................................................
25
CASEWORK -
MECHANICAL
ASSEMBLIES
DESCRIPTION AND PARTS LIST
SECTION 1 (CASEWORK/POWER SUPPLY)
..................
..........
................
26
SECTION 2 (PRINT HEAD/RIBBON FEED/CARRIER)
.................................
27
SECTION 3 (PLATEN/GROUND PLATES)
...............................................
28
SECTION 4 (TRACTOR)
.......................................................................
28
SECTION 5 (GEARS/SENSORS/MOTORS)
..............................................
29
ii