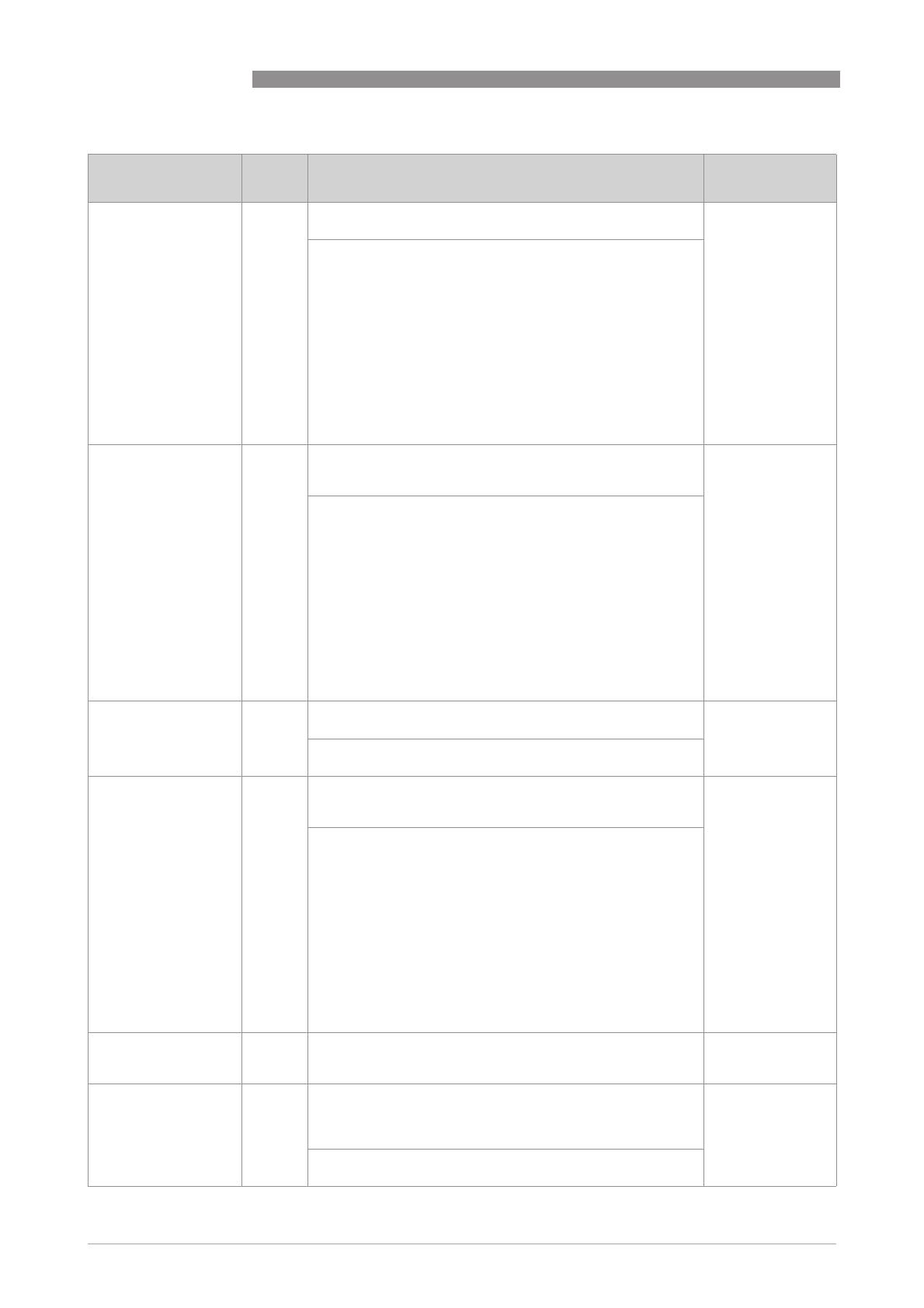
4
OPERATION
20
H250 M40
www.krohne.com 04/2020 - 4001208203 - AD H250-M40 FF R03 en
FD_CHECK_MAP
FD_CHECK_MAPFD_CHECK_MAP
FD_CHECK_MAP
Check Map R/W This parameter enables or disables conditions to be detected
as active for this alarm category. (00) Check
Setting:
(00) Check / (07) Blocked float /
(08) Gas bubbles in the liquid / (09) Pulsating flow /
(10) External magnetic fields /
(12) Electr. Temp. <-45°C or >+120°C/
(13) No output linearization /
(14) No temperature compensation / (15) No pre linearization /
(16) PV between 1.1 and 1.5 FS /
(17) Electr. Temp. <-40°C or >+85°C/
(19) Primary Variable > 150% / (20) Temp. Sensor Failure /
(21) Sensor B Failure / (22) Sensor A Failure /
(23) Invalid drift / (24) Crystal failure /
(25) Memory corrupted / (26) FRAM Error / (27) ROM Error /
(29) Internal communication
FD_CHECK_MASK
FD_CHECK_MASKFD_CHECK_MASK
FD_CHECK_MASK
Check Mask R/W This parameter allows the user to suppress any single or
multiple conditions that are active, in this category, from
being broadcast to the host through the alarm parameter.
Uninitialized
Setting:
(00) Check / (07) Blocked float /
(08) Gas bubbles in the liquid / (09) Pulsating flow /
(10) External magnetic fields /
(12) Electr. Temp. <-45°C or >+120°C/
(13) No output linearization /
(14) No temperature compensation /
(15) No pre linearization / (16) PV between 1.1 and 1.5 FS /
(17) Electr. Temp. <-40°C or >+85°C /
(19) Primary Variable > 150% / (20) Temp. Sensor Failure /
(21) Sensor B Failure / (22) Sensor A Failure /
(23) Invalid drift / (24) Crystal failure /
(25) Memory corrupted / (26) FRAM Error / (27) ROM Error /
(29) Internal communication
FD_CHECK_PRI
FD_CHECK_PRIFD_CHECK_PRI
FD_CHECK_PRI
Check Priority R/W This parameter allows the user to specify the priority of this
alarm category. 0
Setting:
0...15
FD_FAIL_ACTIVE
FD_FAIL_ACTIVEFD_FAIL_ACTIVE
FD_FAIL_ACTIVE
Fail Active RThis parameter reflects the error conditions that are being
detected as active as selected for this category. It is a bit
string, so that multiple conditions may be shown.
Uninitialized
Setting:
(00) Check / (07) Blocked float /
(08) Gas bubbles in the liquid / (09) Pulsating flow /
(10) External magnetic fields /
(12) Electr. Temp. <-45°C or >+120°C/
(13) No output linearization /
(14) No temperature compensation / (15) No pre linearization /
(16) PV between 1.1 and 1.5 FS /
(17) Electr. Temp. <-40°C or >+85°C/
(19) Primary Variable > 150% /
(20) Temp. Sensor Failure / (21) Sensor B Failure /
(22) Sensor A Failure / (23) Invalid drift / (24) Crystal failure /
(25) Memory corrupted / (26) FRAM Error / (27) ROM Error /
(29) Internal communication
FD_FAIL_ALM
FD_FAIL_ALMFD_FAIL_ALM
FD_FAIL_ALM
Fail Diagnostic Alarm This parameter is used primarily to broadcast a change in the
associated active conditions, which are not masked, for this
alarm category to a Host System.
UNACKNOWLEDGED
Unacknowledged R/W A discrete enumeration which is set to "Unacknowledged"
when an alarm occurs, and set to "Acknowledged" by a write
from a human interface device or other entity which can
acknowledge that the alarm/event has been noticed.
Uninitialized
Setting:
Uninitialized / Acknowledged / Unacknowledged
Parameter
ParameterParameter
Parameter
DD name
Access Description and settings Initial Value