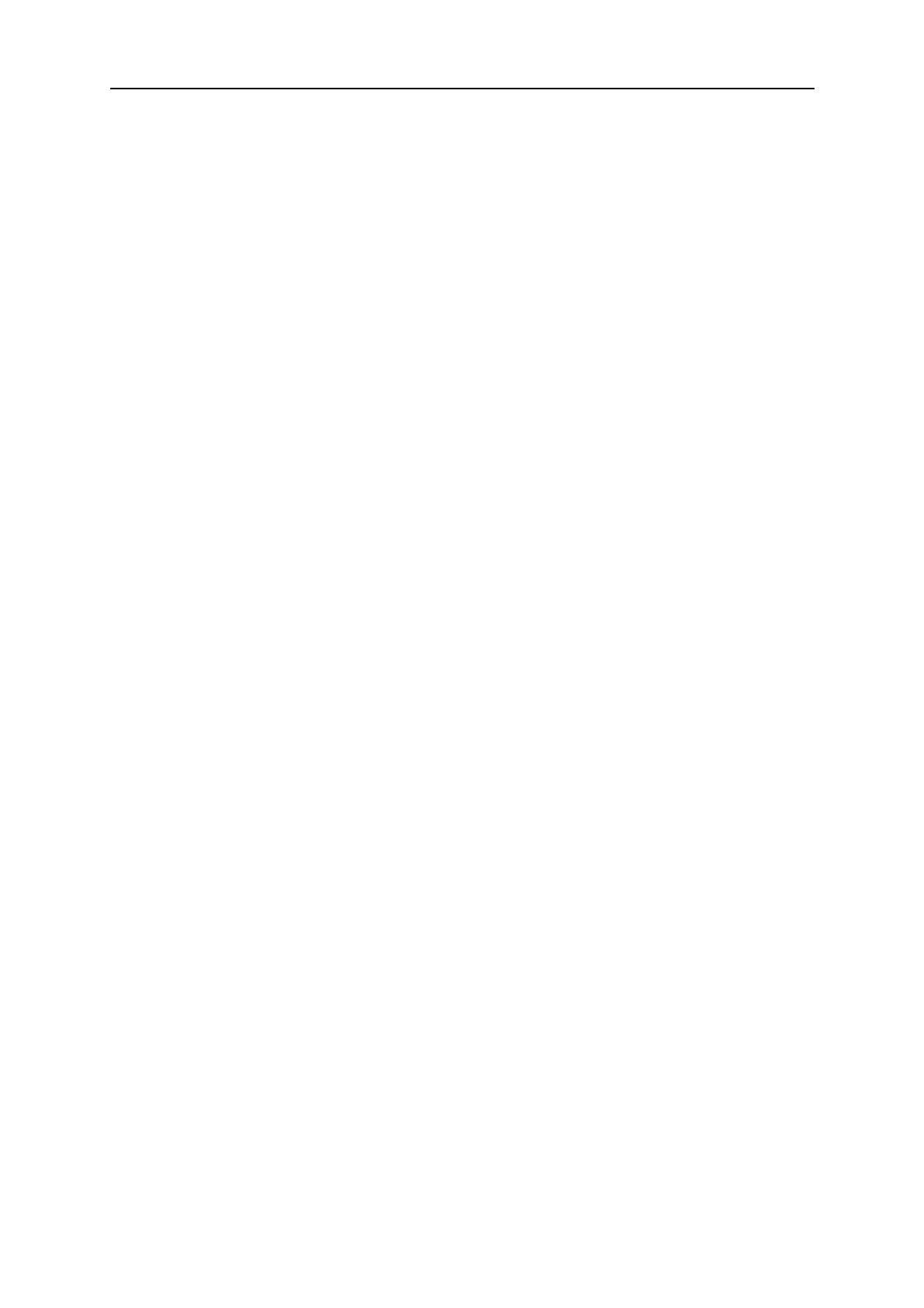
TABLE OF CONTENTS
0740 801 028 © ESAB AB 2017
READ THIS FIRST.................................................................................... 4
INTRODUCTION....................................................................................... 5
WIRING DIAGRAM................................................................................... 7
Component description ......................................................................... 7
A2, A6 PEK Control Unit, Serial no. 921-, 943-, 049-, 327-xxx-xxxx ... 8
A2, A6 PEK Control Unit, Serial no. 628-xxx-xxxx .............................. 10
TECHNICAL DATA ................................................................................... 12
INSTALLATION AND CONNECTIONS .................................................... 13
External connections ............................................................................. 13
Internal connections .............................................................................. 15
DESCRIPTION OF OPERATION.............................................................. 23
1 MMC unit .............................................................................................. 23
Circuit board identity............................................................................. 23
1AP1:1 Power supply and CAN bus..................................................... 24
CAN bus & termination...................................................................... 26
1AP1:2 Display control ......................................................................... 27
1AP1:3 Pushbutton monitoring............................................................. 27
Buzzer ............................................................................................... 28
1AP1:4 USB memory ........................................................................... 28
1AP1:5 Encoder monitoring ................................................................. 29
1AP1:6 Ethernet interface, from serial no. 628-xxx-xxxx ..................... 30
1AP1:7 USB-host B (internal), from serial no. 628-xxx-xxxx................ 31
1AP1 Component positions.................................................................. 32
26 Motor control & motor drive ............................................................. 34
26AP1 Motor control .............................................................................. 34
Circuit board identity............................................................................. 34
26AP1:1 Power supply ......................................................................... 34
26AP1:2 CAN bus & termination .......................................................... 35
26AP1:3 Encoder for wire feed motor .................................................. 36
26AP1:4 Encoder for travel motor ........................................................ 37
26AP1:5 Travel limit switches............................................................... 37
26AP1:6 Laser lamp supply ................................................................. 38
26AP1:7 External Start/Stop switch ..................................................... 38
26AP1 Component positions................................................................ 39
26AP2 Motor drive.................................................................................. 40
26AP2:1 Power supply ......................................................................... 40
26AP2:2 Motor 1 drive (Wire feed at CN7)........................................... 41
26AP2:3 Motor 2 drive (Travel motion at CN6) .................................... 43
26AP2:4 Relay outputs......................................................................... 44
26AP2 Circuit board versions............................................................... 45
26AP2 Component positions................................................................ 46