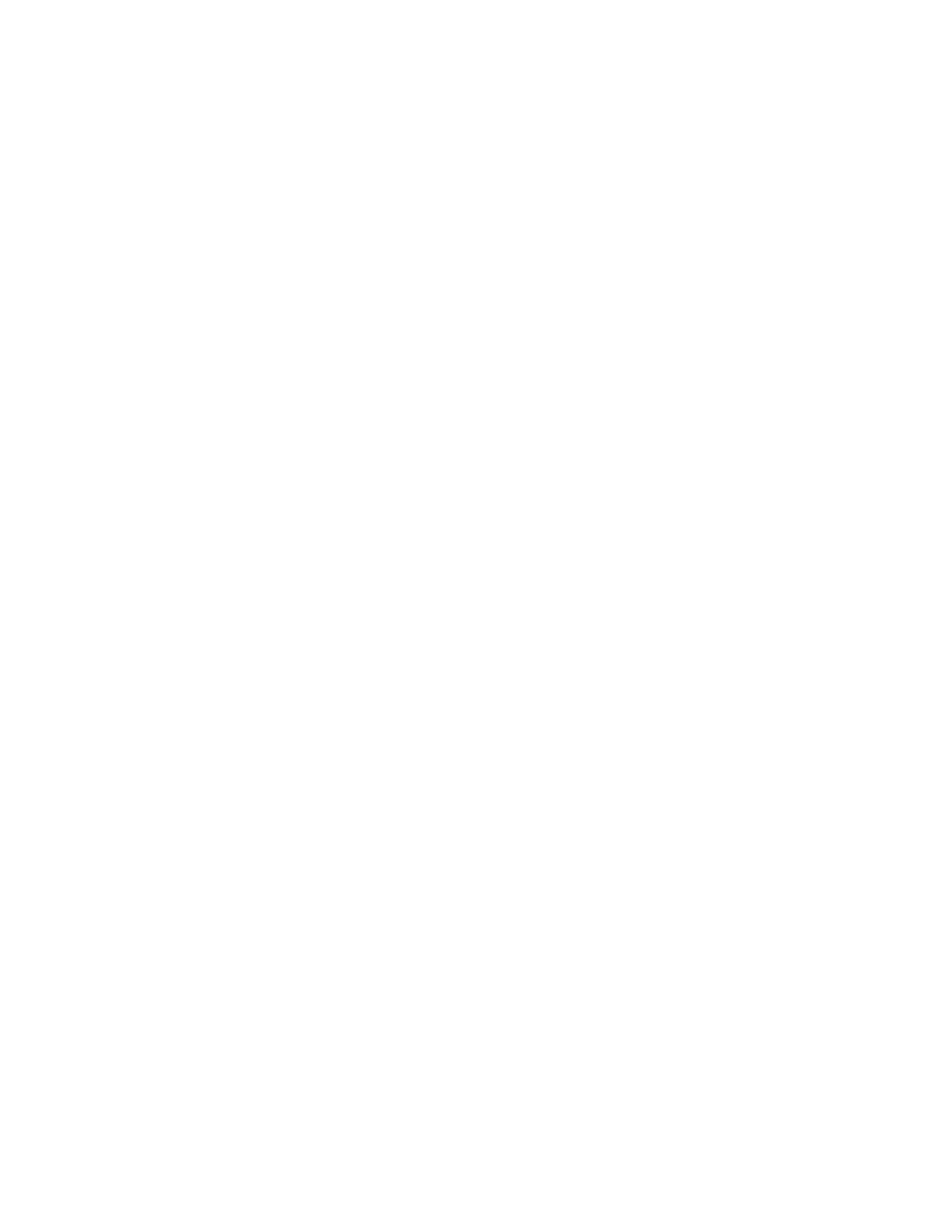
© Olivier Nicolas Micro user manual rev 4, 26th Oct 2014 p 9
4.4. Power bus and gyro considerations.
The power supply system consists of a normal rail that can handle 5 amps from each end. The micro receivers are not equipped
with any battery backer system or voltage regulators.
The Micro receivers are the world's smallest units with integrated gyros.
These are available on our Micro Gyro I and III receivers. These gyros are extremely stable under a broad range of
temperatures and can operate in Normal or Heading Hold mode.
The gyro gains can be set via the software or from the transmitter and can be assigned to any channel.
The receiver outputs can be freely assigned to any transmitter output and up to 8 servos can be synchronized if they are
connected to the same control surface simply by a click of the mouse.
The description of all of the GigaControl software/ BAT transmitter functions is detailed in a separate user manual.
4.5. Transmitter system considerations.
The Weatronic system can operate from both a specific DV4 antenna module that plugs into the existing transmitters like the
Taranis unit, or the dedicated Weatronic BAT transmitters.
The optional DV4 module or BAT series transmitter are fitted with a micro SD card that automatically stores all data transmitted
or received during the flight. Thanks to a small condenser the information will not be lost if the transmitter power fails or if the
transmitter malfunctions. The information can always be retrieved for analysis at a later stage. This can be considered as a black
box system. In the event of a system failure or crash this function will greatly assist in identifying the root cause of the event.
All Weatronic Dual 2.4 Dual FHSS systems include an extremely comprehensive telemetry function which can record
parameters as the signal strength received by both half receiver, the voltage of the batteries, the receiver temperature as well
as various telemetry data like GPS information or air speed indications.
As standard, our 2.4 Dual FHSS micro receivers feedbacks the following data to the transmitter:
• Signal strength (range warning)
• Receiver battery pack voltage
If these values fall outside of a certain range a warning will given. The red ‘ERROR’ LED will begin flashing on the transmitter
module and if an earphone is fitted a voice annunciation will be heard.
When using our GigaControl software a variety of other parameters can be broadcast to the ‘ERROR’ LED and/ or by voice to
earphones. Additionally, the Micro SD card will be storing all of the data received and transmitted and this information can be
shown as a ‘live stream’ on a PC screen.
Weatronic adapter modules are available for all popular Multiplex, Futaba and JR/Graupner transmitters which are fitted with
removable modules. Up to 12 channels can be operated with the DV 4 modules.