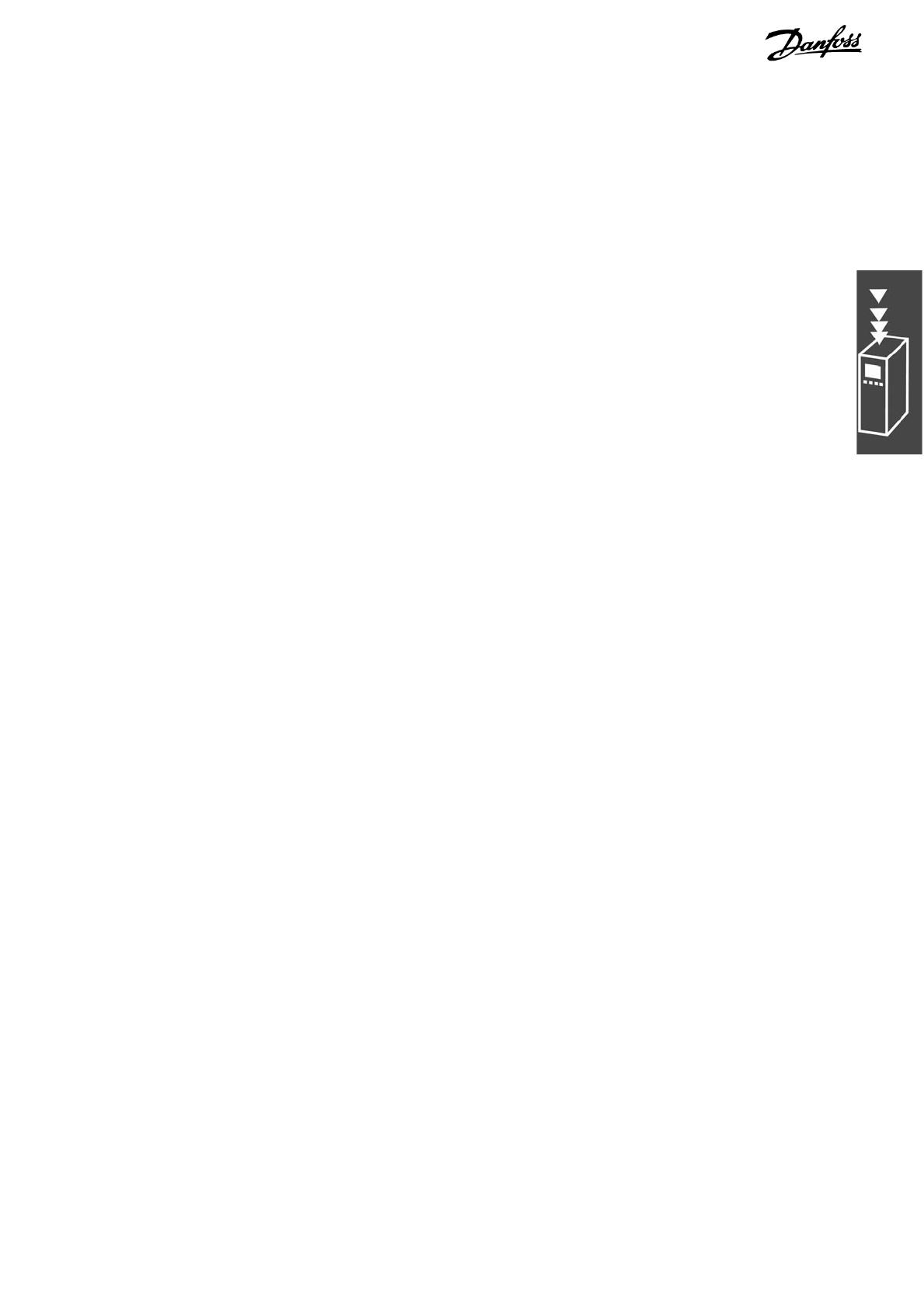
MCO 305 Design Guide
__ Introduction to VLT Motion Control Option MCO 305 __
MG.33.L2.02 – VLT is a registered Danfoss trademark 15
Encoder
MCO 305 supports various encoder types:
Incremental encoder with RS422 signal type.
Incremental encoder with sine–cosine signal type.
Absolute encoder with SSI interface.
Master and feedback/slave encoder type can be selected independently; encoders can be rotary or linear.
Selection of encoder type depends on application requirements and general preferences. Attention must
however be paid to the resolution of the selected encoder. There are 3 important selection criteria:
Maximum position accuracy is +/- 1 encoder increment.
To ensure stable and dynamic control a minimum of 20 encoder increments per PID controller sample
period (default is 1 millisecond) is needed at the minimum application velocity.
Maximum frequency of the MCO 305 encoder inputs must not be exceeded at maximum velocity.
The feedback encoder can be mounted directly on the motor shaft or behind gearboxes and/or other types
of transmissions. There are how ever some important issues to be aware of when mounting the encoder:
There should be a firm connection between motor and encoder. Slip, backlash, and elasticity will reduce
control accuracy and stability.
When the encoder is running at a low speed it must have a high resolution in order to meet the above
requirement (minimum 20 encoder increments per controller sample).
Program Execution
MCO 305 can store multiple programs, up-to 90. Only one of these programs can be executed at a time,
there are three ways to control which program to execute:
Via parameter 33-80 Activated Program Number.
Via digital inputs (parameters 33-50 through 33-59, 33-61 and 33-62).
Via PC software.
One program must be defined as Autostart program, the Autostart program is automatically executed after
power up. Without Autostart program it is only possible to execute a program via PC software.
The Autostart program is always executed first, if the Autostart program is terminated (no loop or by EXIT
command) the following can happen:
1. When parameter 33-80 (Activated Program Number) = -1 and no input (parameters 33-50 through 33-
59, 33-61 and 33-62) is selected as Start program execution ([13] or [14]). The Autostart program will
restart.
2. When parameter 33-80 (Activated Program Number) -1 and no input (parameters 33-50 through 33-
59, 33-61 and 33-62) is selected as Start program execution ([13] or [14]). The selected program (par.
33-80) will be executed.
3. When an input (parameters 33-50 through 33-59, 33-61 and 33-62) is selected as Start program
execution ([13] or [14]) and one or more inputs are selected as Program select ([15]). The selected
program (Program select inputs) will be executed when the Start program execution input is activated.
The active program can be aborted via a digital input when defining an input as Break program execution
(Option [9] or [10] in 33-50 through 33-59, 33-61 and 33-62). The aborted program can be restarted via a
digital input when defining an input as Continue program execution (Option [11] or [12] in 33-50 through
33-59, 33-61 and 33-62).
Starting the Autostart program after power-up can be avoided by pressing the [Cancel] key of the FC 300
LCP during power-up. The key must be pressed until the message User abort (error 119) appears in the
display.