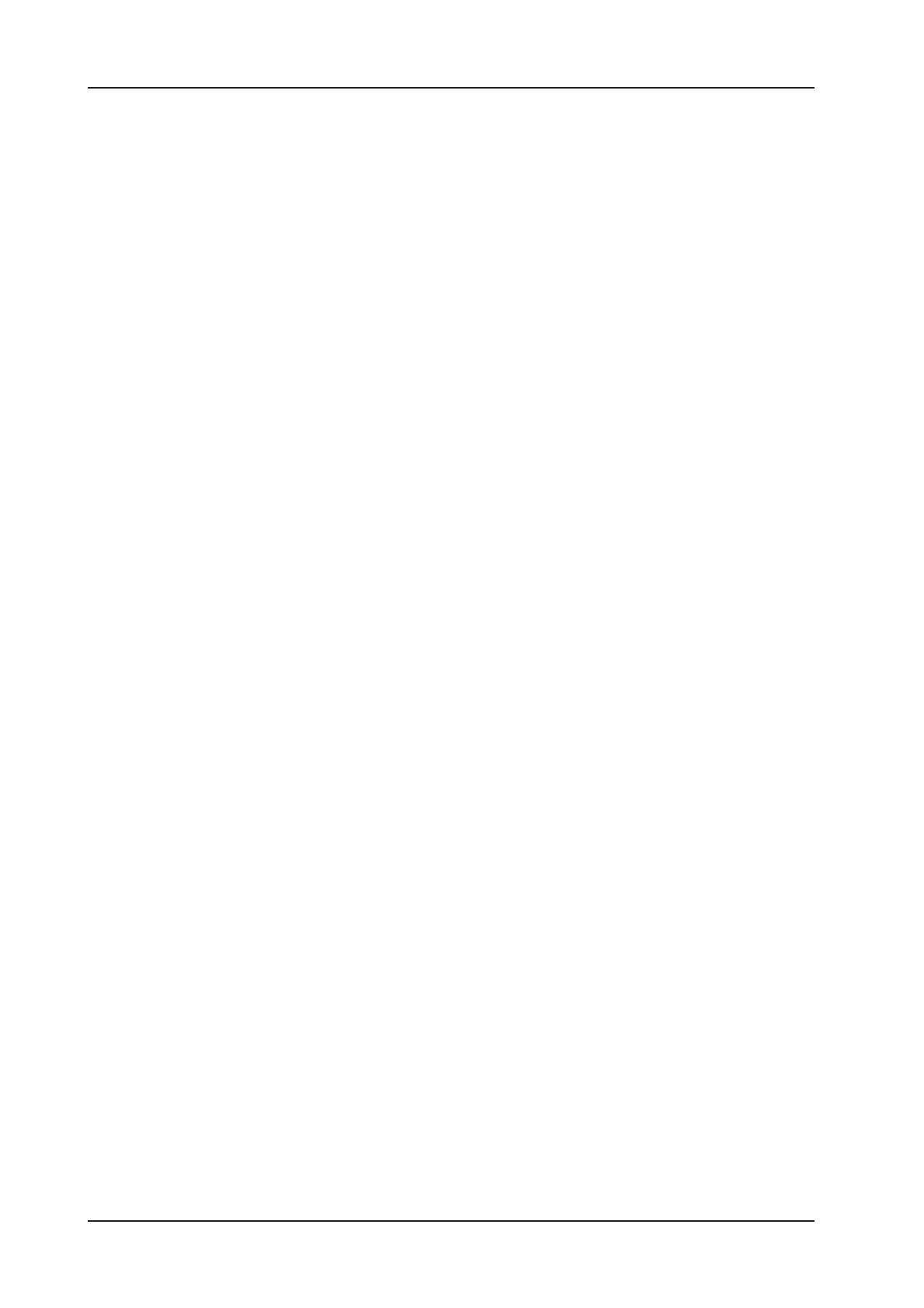
SYSTEMA
6
Rev. 03GB0602
2.2 Functionning description
The "INFRA…ROSSO" ceramic heaters models are the following:
a) Mod. SCR 25 m with pre-mix combustion and manual variation of thermal power.
b) Mod. SCR 45 m with pre-mix combustion and manual variation of thermal power.
c) Mod. SCR 25 a with pre-mix combustion and automatic variation of thermal power by a InfraNet
control network and a Inet electric board (see specifications in the following paragraphs).
d) Mod. SCR 45 a with pre-mix combustion and automatic variation of thermal power by a InfraNet
control network and a Inet electric board (see specifications in the following paragraphs).
The functioning procedure of the over described models can be resumed in the following points :
A) The models …m (manual), with the digital PWM variator situated inside the equipment are regulated
at the factory during the final control before delivery to the thermal power requested (see table at
paragraph 2.3).
The demanded power will remain fix. If necessary it will be possible to modify the power according the
climate conditions of the moment, by the ground control board, using a linear potentiometer or by a
remote infrared control (optional).
The models …m (manual) with the remote control, will be programmed with the power requested by the
final user (see table at paragraph 2.3) and they will be controlled by a ON/OFF ambient thermostat.
Sequence of functioning of models …m (manual):
After the reception of the electric input, the lighting and start up procedure begins, with the following
steps :
1) The 577 DBC device starts the fan for the mixing chamber washing, for a minimum of 10 seconds.
The fan will start at the maximum speed, for a determined time, then it twill go down to the
programmed speed with the digital PWM variator.
2) When the washing stage is completed, the lighting discharge takes place for a minimum of ten
seconds (Ts 10) ; in the same time the gas valve 848 Sigma will be put in the open position by
electronic card.
3) The 848 Sigma gas valve will supply the gas at a pressure equal to the depression generated by
the fan (for instance fan depression 5 mbar > pressure delivered by the valve 5 mbar > pressure
read downstream the valve = 0).
4) The mixture generated inside the mixing chamber will be lighted on the ceramic plate. After a time
interval Ts the ignition discharge will stop and the electrode will switch automatically to the function
of flame detection.
If lighting will not take place or the flame will not be detected, the 577 DBC device, after a time interval
of 20 seconds, will make a second lighting attempt.
The equipment reset is of electric type with extinction and new lighting of electric supply.
5) The power at start up will be equal to the maximum power of the heater for the time interval
programmed in the PWM variator. After this lighting step, the thermal power of the heater will be
the one which will have been established (for instance : for SCR 25 m - programmed power PWM
20% - Start at 70% of PWM corresponding to 24 kW/h - After the start up time, the thermal flow
of the heater will be the one which will have been fixed PWM 20% = 12 kW/h).
B) The models…a (automatic) will be different from the manual models only by the standpoint of
control of the emitted power which in the manual models can be selected manually while in the
automatic models the thermal power is modulated by the master INET electric board (which is
outside the heater) as a function of the temperature detected in the ambient air, compared with
the established temperatures of manual models (SET POINT).
The master INET electric board, will change with the proportional integrated the fan speed and, as a
consequence, the gas flow and the emitted power.
The lighting sequence for the automatic models will be the one shown at the previous points 1-2-3-4.