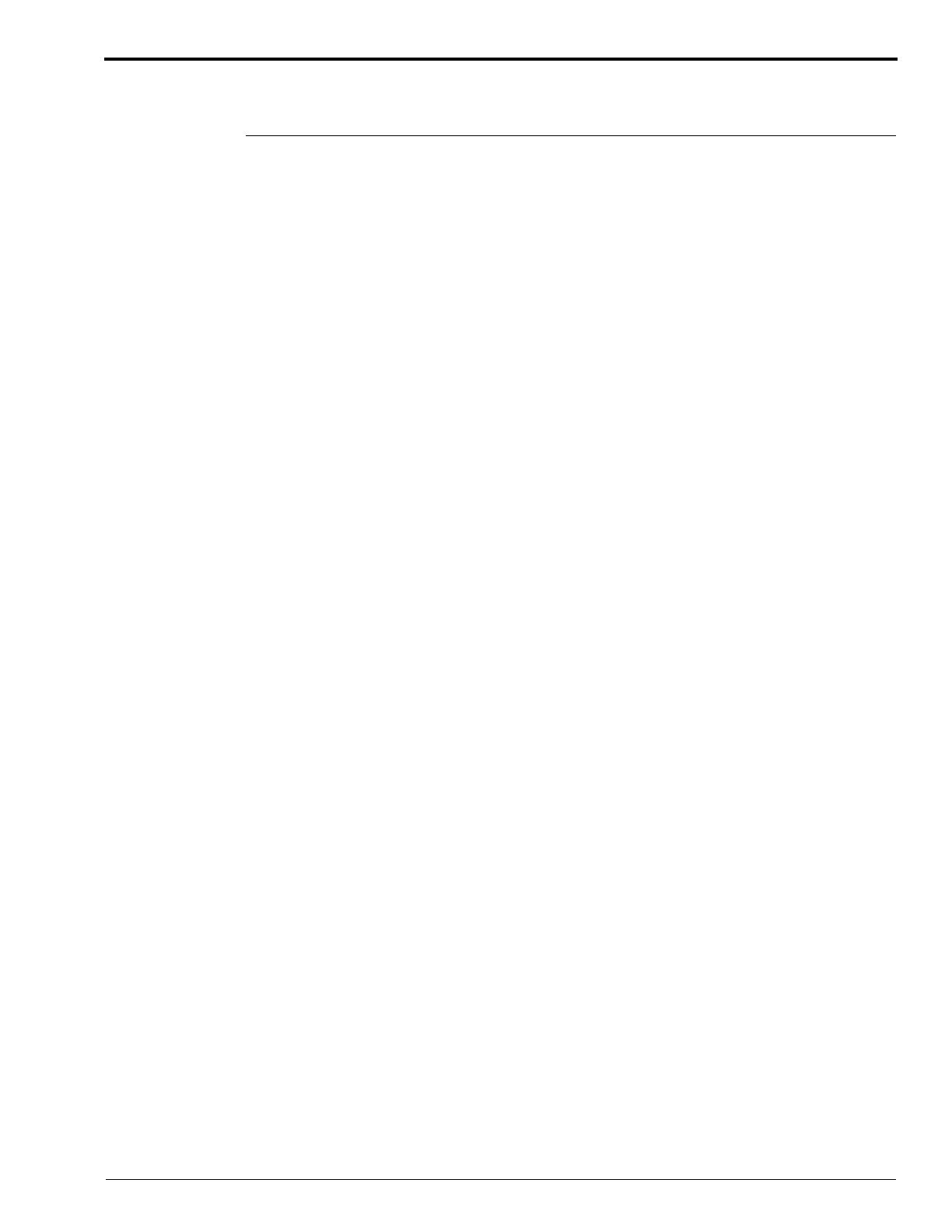
981090 – September 1995 3
Description Page
Table of Contents
Introduction . . . . . . . . . . . . . . . . . . . . . . . . . . . . . . . . . . . . . . . . . . . . . . . . . . . . . . . . . . . . 5
Electrostatic Discharge . . . . . . . . . . . . . . . . . . . . . . . . . . . . . . . . . . . . . . . . . . . . . . . . 5
Required Special Tools . . . . . . . . . . . . . . . . . . . . . . . . . . . . . . . . . . . . . . . . . . . . . . . . 6
Overview of the PROCESSOR. . . . . . . . . . . . . . . . . . . . . . . . . . . . . . . . . . . . . . . . . . 6
Energizing the PROCESSOR . . . . . . . . . . . . . . . . . . . . . . . . . . . . . . . . . . . . . . . . . . . 8
De-energizing the PROCESSOR . . . . . . . . . . . . . . . . . . . . . . . . . . . . . . . . . . . . . . . . 8
Draining the PROCESSOR TANKS. . . . . . . . . . . . . . . . . . . . . . . . . . . . . . . . . . . . . . 9
RACKS . . . . . . . . . . . . . . . . . . . . . . . . . . . . . . . . . . . . . . . . . . . . . . . . . . . . . . . . . . . . . . . . 10
Repairing the DEVELOPER and FIXER RACKS . . . . . . . . . . . . . . . . . . . . . . . . . . 10
Adjusting the DEVELOPER and FIXER RACKS for Squareness. . . . . . . . . . . 10
ENTRANCE ROLLER PAIR of the DEVELOPER and FIXER RACKS . . . . 11
EXIT ROLLER PAIR of the DEVELOPER and FIXER RACKS . . . . . . . . . . 13
Plastic ROLLERS of the DEVELOPER and FIXER RACK . . . . . . . . . . . . . . . 15
Removing the GUIDE SHOES of the DEVELOPER and FIXER RACKS . . . 16
Repairing the WASH RACK . . . . . . . . . . . . . . . . . . . . . . . . . . . . . . . . . . . . . . . . . . . 17
Adjusting the WASH RACK for Squareness . . . . . . . . . . . . . . . . . . . . . . . . . . . 17
ENTRANCE ROLLER ASSEMBLY of the WASH RACK . . . . . . . . . . . . . . . 18
EXIT SQUEEGEE ROLLER ASSEMBLY of the WASH RACK . . . . . . . . . . 22
CENTRAL DRIVE ROLLER PAIR of the WASH RACK . . . . . . . . . . . . . . . . 26
Disassembling a CENTRAL DRIVE ROLLER PAIR of the WASH RACK . . 26
WASH TUBES and GASKETS - WASH RACK . . . . . . . . . . . . . . . . . . . . . . . 30
Repairing the DRYER RACK. . . . . . . . . . . . . . . . . . . . . . . . . . . . . . . . . . . . . . . . . . . 32
Adjusting the DRYER RACK for Squareness . . . . . . . . . . . . . . . . . . . . . . . . . . 32
Removing the DRYER AIR TUBES . . . . . . . . . . . . . . . . . . . . . . . . . . . . . . . . . 33
Removing the DRYER ROLLERS . . . . . . . . . . . . . . . . . . . . . . . . . . . . . . . . . . 35
DRYER . . . . . . . . . . . . . . . . . . . . . . . . . . . . . . . . . . . . . . . . . . . . . . . . . . . . . . . . . . . . . . . 38
Removing the DRYER THERMISTOR (RT2), AIR VANE SWITCH (S4),
DRYER HEATER (R2), and DRYER BLOWER MOTOR (B1) . . . . . . . . . . . . . 38
Removing the DC INTERLOCK SWITCH S6, the DRYER THERMISTOR, and the AIR
VANE SWITCH . . . . . . . . . . . . . . . . . . . . . . . . . . . . . . . . . . . . . . . . . . . . . . . . . . . 41
Removing the DRYER HEATER. . . . . . . . . . . . . . . . . . . . . . . . . . . . . . . . . . . . . . . . 42
Removing the DRYER BLOWER . . . . . . . . . . . . . . . . . . . . . . . . . . . . . . . . . . . . . . . 44
MAIN DRIVE . . . . . . . . . . . . . . . . . . . . . . . . . . . . . . . . . . . . . . . . . . . . . . . . . . . . . . . . . . 46
Removing the DRIVE MOTOR . . . . . . . . . . . . . . . . . . . . . . . . . . . . . . . . . . . . . . . . . 46
Removing the MAIN DRIVE SHAFT . . . . . . . . . . . . . . . . . . . . . . . . . . . . . . . . . . . . 48
Adjusting the MAIN DRIVE CHAIN and the DRIVE MOTOR . . . . . . . . . . . . . . . . 50
Plumbing . . . . . . . . . . . . . . . . . . . . . . . . . . . . . . . . . . . . . . . . . . . . . . . . . . . . . . . . . . . . . . 52
Routing the TUBING and Positioning the SCREW CLAMPS . . . . . . . . . . . . . . . . . 52
Removing the RECIRCULATION PUMPS and the REPLENISHMENT PUMP. . . 55
Removing the DEVELOPER (B5) and FIXER (B6) RECIRCULATION PUMPS 55
Removing the WASH RECIRCULATION PUMP (B2) . . . . . . . . . . . . . . . . . . 57
Removing the DEVELOPER/FIXER REPLENISHMENT PUMP (B3) . . . . . 58
Adjusting the Fixer To Developer Replenishment Rate Ratio . . . . . . . . . . . . . . 60
Removing the DEVELOPER HEATER (R1). . . . . . . . . . . . . . . . . . . . . . . . . . . . . . . 61
Removing the DEVELOPER THERMISTOR (RT1). . . . . . . . . . . . . . . . . . . . . . . . . 62
Removing the DRAIN VALVES . . . . . . . . . . . . . . . . . . . . . . . . . . . . . . . . . . . . . . . . 65
Disassembling and Inspecting the DRAIN VALVES. . . . . . . . . . . . . . . . . . . . . 65
Replacing the DRAIN VALVES . . . . . . . . . . . . . . . . . . . . . . . . . . . . . . . . . . . . 67