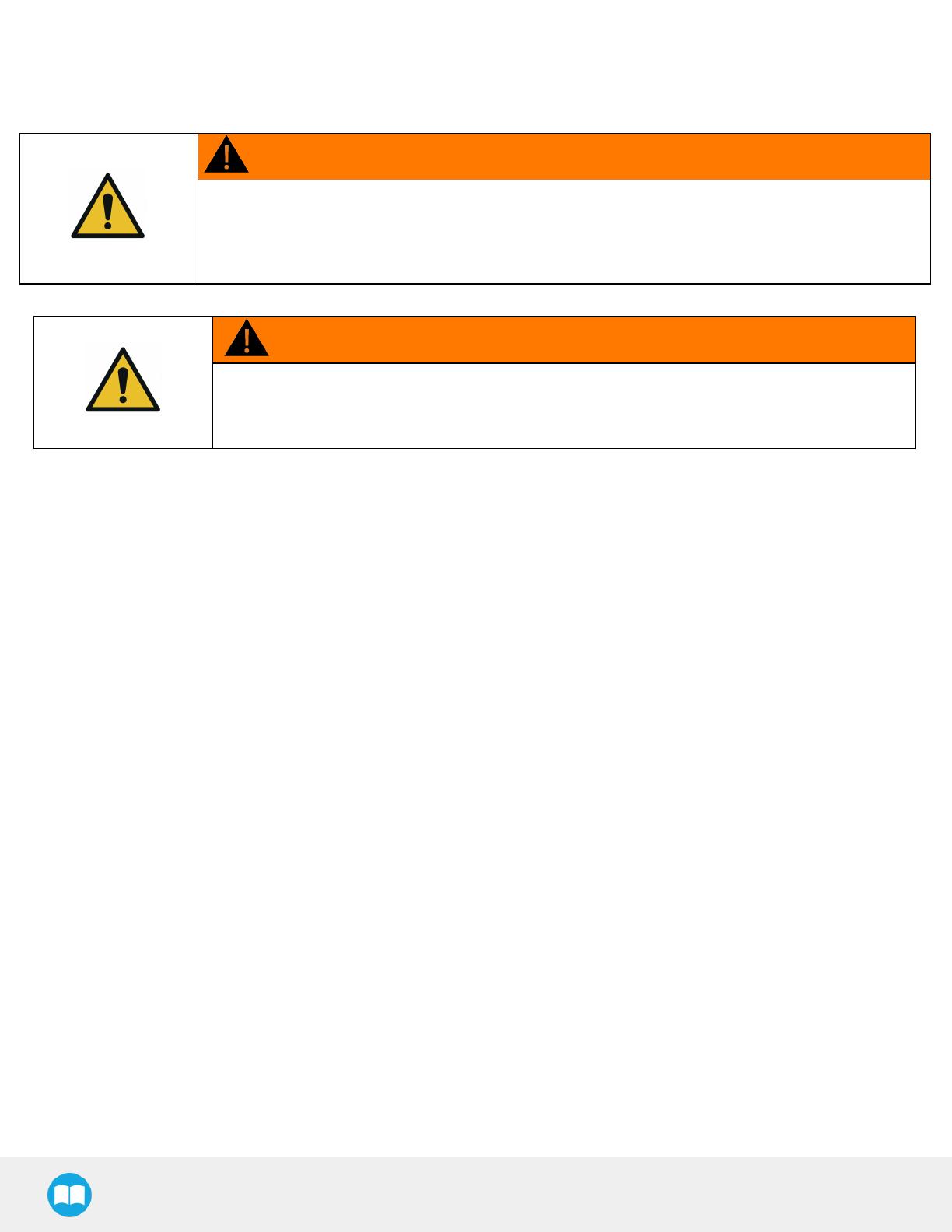
2.2. Risk Assessment
2.2.1. General Risk Assessment
WARNING
The user must have read and understood all of the instructions in the following manual before operating
the Robotiq Palletizing Solution. Any use of the Palletizing Solution in non-compliance with these
instructions is deemed inappropriate and may cause injury or damage.
It is the user's responsibility to ensure that all local safety measures and regulations are met.
WARNING
Unauthorized Modification
DONOTmodify or alter the equipment without the express written consent and approval of the
manufacturer.
The entire cell (i.e., the robot, the PowerPick Vacuum Gripper or any other gripper, the linear axis, and any other equipment used in
the final application) must go through a comprehensive risk assessment process before they can be used.
All cells being different, it is important to perform a risk assessment and to enforce the required standards. Please note that the
results of the risk assessment depend on the usage and application.
The following non-exhaustive list presents risks that must be assessed during the integration process:
lRisk of load ejection resulting from loss of vacuum.
lRisk of load dropping resulting from loss of vacuum.
lRisk of pinching by any moving component of the Robotiq Palletizing Solution or the robot.
lRisk of damage or breaking if using a custom suction cup bracket that does not meet the technical requirements.
lRisk of damaged objects or injury resulting from a collision between an object and the robot, the gripper or the boxes.
lRisk of injury resulting from a collision between a person and the Solution.
Additional hazards may be present, depending on the configuration and what is being palletized. For instance, the object handled
by the gripper could be inherently dangerous to the operator.
To ensure an adequate level of safety, floor markings must be applied to delineate safe zones around the Solution. It is the
responsibility of the integrator to establish the proper safe distance from the Solution to protect the user.
13