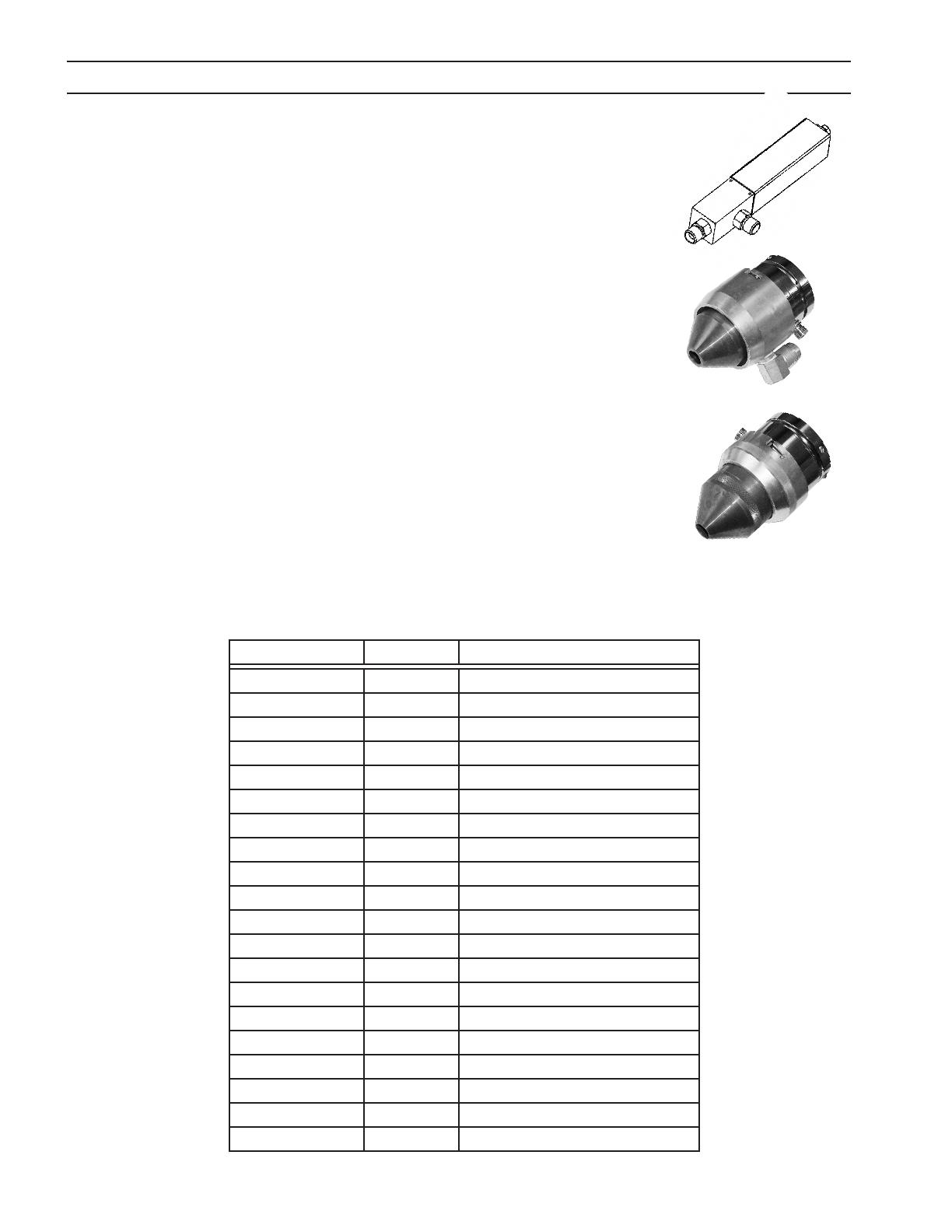
138
PT-36 Repair & Accessories Kit ...................................................................................0558005221
SECTION 2 DESCRIPTION
2.4.1 PT-36 Torch Consumable Kits
2.4 Optional Accessories:
Test Flow Meter - This valuable troubleshooting tool allows measurement of the ac-
tual plasma gas ow through the torch ...............................................................................21317
Bubble Muer - When used in conjunction with a water pump recirculating water
from the table and by using compressed air, this device creates a bubble of air which
enables a PT-36 Plasmarc Cutting Torch to be used underwater with slight sacrice
of cut quality. This system also permits operation above water as the ow of water
through the muer reduces fume, noise, and arc U.V. Radiation).
(for installation/operation instructions see manual 0558006722) ............................. 37439
Air Curtain - This device when supplied with compressed air is used to improve the
performance of the PT-36 Plasmarc Cutting Torch when cutting underwater. The de-
vice mounts onto the torch and produces a curtain of air. This allows the plasma arc to
operate in a relatively dry zone, even though the torch has been submerged to reduce
noise, fume, and arc radiation. To be used in underwater applications only.
(for installation/operation instructions see manual 0558006404) .............................37440
Part Number Quantity Description
0558003804 1 Torch Body PT-36 w/O-rings
996528 10 O-ring 1.614 ID x .070
0558002533 2 Bae, 4 Hole x .032
0558001625 2 Bae, 8 Hole x .047
0558002534 1 Bae, 4 x .032 Reverse
0558002530 1 Bae, 8 x .047 Reverse
0558005457 1 Bae, 4 Hole x .022
0558003924 3 Electrode Holder PT-36 w/O-ring
86W99 10 O-ring .364 ID x .070
37082 2 Nozzle Retaining Cup, Standard
21796 1 Shield Gas Diuser, Low Current
21944 5 Shield Gas Diuser, Standard
22496 1 Shield Gas Diuser, Reverse
37081 2 Shield Retainer, Standard
0558003858 2 Contact Ring w/screw
37073 6 Screw, Contact Ring
93750010 2 Hex Key Wrench .109"
996568 1 Nut Driver 7/16" (Electrode tool)
0558003918 1 Electrode Holder Tool PT-36
77500101 1 Silicon Grease DC-111 5.3oz