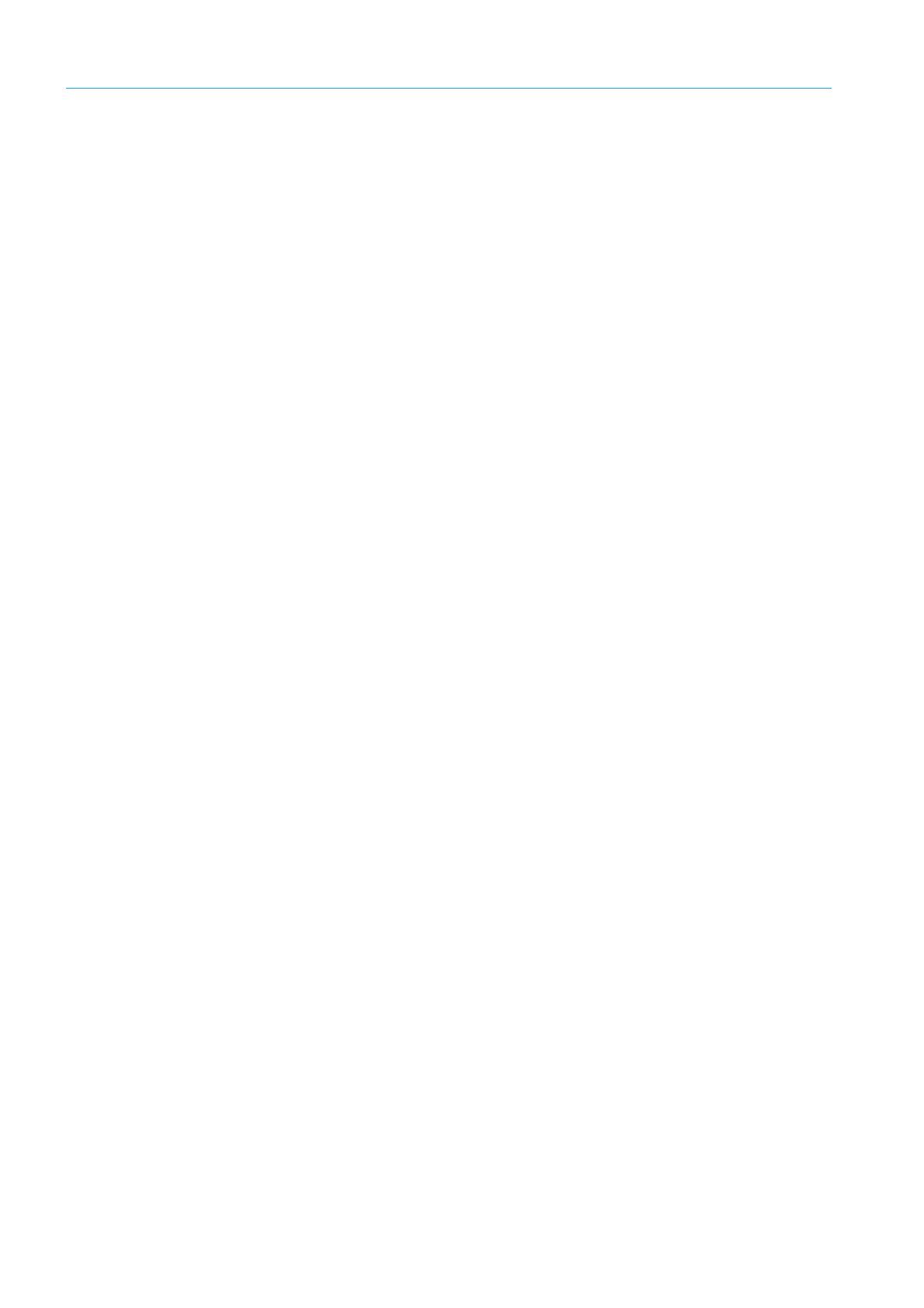
CONTENTS
4
8015383/ZUQ7/V1-3/2020-06 | SICKOPERATING INSTRUCTIONS | TRANSIC151LP
Subject to change without notice
1 Important information .............................................................................. 8
1.1 Main operating information............................................................................ 8
1.1.1 Installation location........................................................................ 8
1.2 Intended use ................................................................................................... 9
1.2.1 Purpose of the TRANSIC151LP...................................................... 9
1.2.2 Operation in potentially explosive atmospheres........................... 9
1.2.3 Approvals ...................................................................................... 9
1.3 Responsibility of user ................................................................................... 10
2 Product description ................................................................................. 11
2.1 Product identification ................................................................................... 11
2.2 Functional principle/measuring principle ................................................... 11
2.2.1 TRANSIC151LP probe design ...................................................... 11
2.3 TRANSIC151LP variants............................................................................... 12
2.3.1 Variant for in-situ-measurement.................................................. 12
2.3.2 Variant for extractive measurement............................................ 13
2.3.3 Variant for ambient gas measurement ....................................... 14
2.4 Explosion protection according to ATEX and IECEx..................................... 15
3 Installation................................................................................................17
3.1 Project planning............................................................................................ 17
3.1.1 Chemical tolerance ...................................................................... 17
3.1.2 Temperature conditions ............................................................... 17
3.1.3 Strong light sources near the oxygen measuring probe ............. 18
3.1.4 Pressure........................................................................................ 18
3.2 Information on installation in potentially explosive atmospheres.............. 19
3.3 Installation .................................................................................................... 19
3.3.1 Safety information........................................................................ 19
3.3.2 Prerequisites for assembly .......................................................... 20
3.3.3 Installation angle.......................................................................... 20
3.4 Installation options ....................................................................................... 21
3.4.1 Process conditions for installation options ................................. 21
3.4.2 TRANSIC151LP installation - in-situ with flange ......................... 21
3.4.3 TRANSIC151LP installation - extractive ...................................... 23
3.4.4 TRANSIC151LP installation - ambient gas measurements ....... 25
3.5 Connections .................................................................................................. 26
3.5.1 Connecting the TRANSIC151LP transmitter ............................... 28
3.5.2 Connecting the TSA151 voltage supply unit ............................... 29
3.5.3 Connecting the analog and digital outputs ................................. 30
3.5.4 Connecting power supply to the TSA151 voltage supply unit .... 30
3.5.5 Gas connection (optional)............................................................ 31
Contents