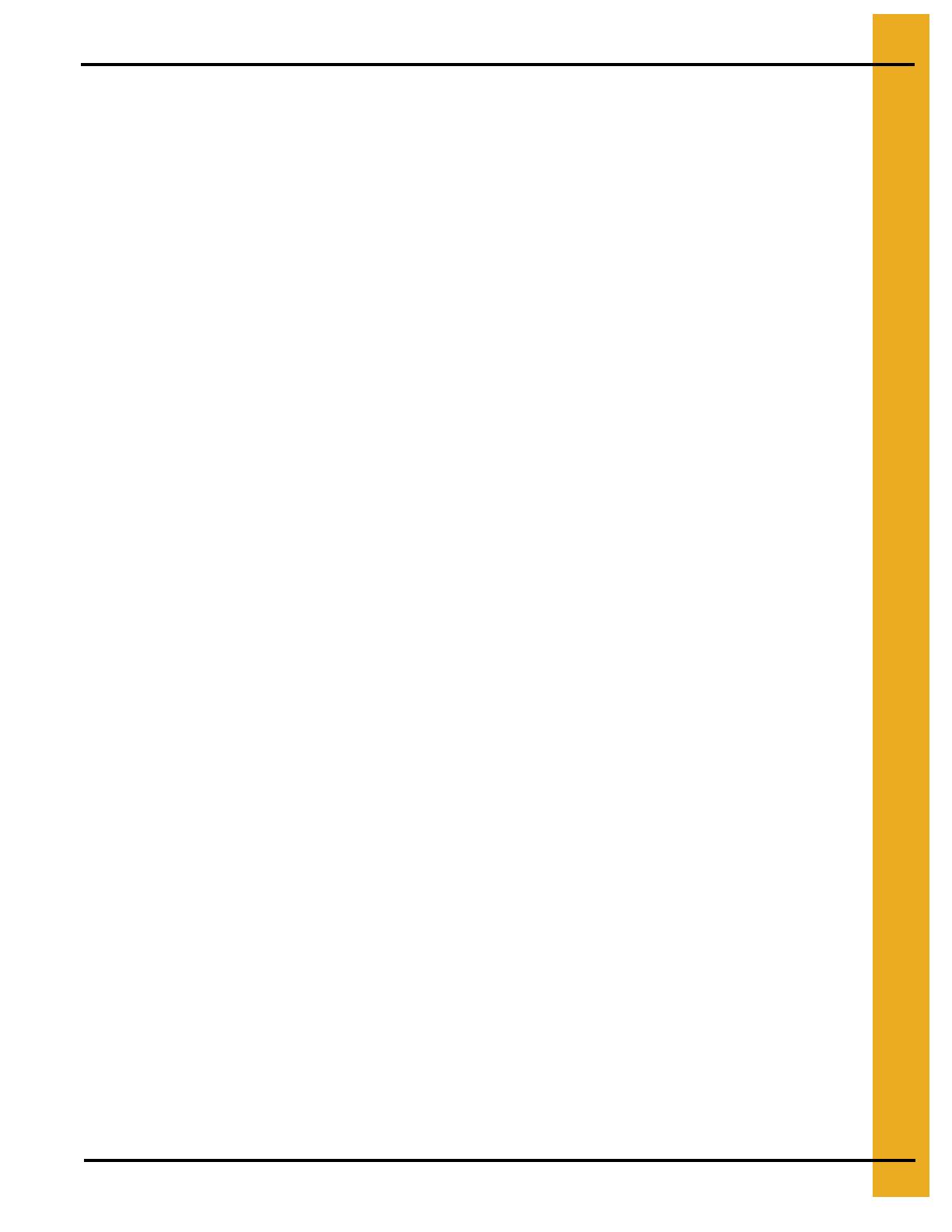
PNEG-552 100 Series Dryer 3
Table of Contents
Contents
Chapter 1 Safety ..................................................................................................................................................5
Safety Guidelines ............................................................................................................................... 5
Dryer Operation .................................................................................................................................. 6
Emergency Stop ................................................................................................................................. 6
Safety Precautions ............................................................................................................................. 7
Chapter 2 Safety Alert Decals ............................................................................................................................8
Chapter 3 Dryer Control Panel .........................................................................................................................12
Dryer Control Panel Featuring the 100 Series Control System ........................................................ 13
Special Features .............................................................................................................................. 18
Safety Circuit Shut Down Messages ................................................................................................ 18
Chapter 4 Error Conditions ..............................................................................................................................20
Chapter 5 Dryer Pre-Start Checks ...................................................................................................................22
Inspect the Metering Rolls ................................................................................................................ 22
Set Control Switches ........................................................................................................................ 22
Electrical Power ................................................................................................................................ 23
Control Power Switch ....................................................................................................................... 23
Power Start Button ........................................................................................................................... 23
Fuel Check ....................................................................................................................................... 23
Load Auger ....................................................................................................................................... 23
1 Speed Operation ........................................................................................................................... 23
Metering Roll Operation ................................................................................................................... 24
Fan Switch ........................................................................................................................................ 24
Burner Safety ................................................................................................................................... 25
Heater Test Fire ............................................................................................................................... 25
Staged Batch Check ......................................................................................................................... 25
Dryer Shut Down .............................................................................................................................. 26
Stopping Dryer Operation ................................................................................................................. 26
Emergency Stop ............................................................................................................................... 26
Chapter 6 Dryer Start-Up ..................................................................................................................................27
Continuous Flow Operation .............................................................................................................. 27
Full Start-Up Check .......................................................................................................................... 27
Filling the Dryer ................................................................................................................................ 27
Staged Batch Operation ................................................................................................................... 28
Starting the Dryer ............................................................................................................................. 30
Adjusting the Temperature ............................................................................................................... 31
Full Heat Continuous Flow Operation .............................................................................................. 32
Adjusting the Moisture Control ......................................................................................................... 33
Chapter 7 Service ..............................................................................................................................................34
Seasonal Inspection and Service ..................................................................................................... 34
Suggested Lubricants....................................................................................................................... 35
Lubrication Procedures .................................................................................................................... 35
Additional Checks ............................................................................................................................. 35
Fan Propeller Removal and Installation ........................................................................................... 37
Threaded Bushing Holes .................................................................................................................. 37
Clearance Holes ............................................................................................................................... 37
Fan Motor Removal and Installation ................................................................................................. 38
Heater Parts Removal and Installation .........................................................................................
.... 40
Metering Roll Servicing .................................................................................................................... 41
How to Determine a Metering Roll Problem ..................................................................................... 42
How to Clear a Jammed Metering Roll ............................................................................................. 43