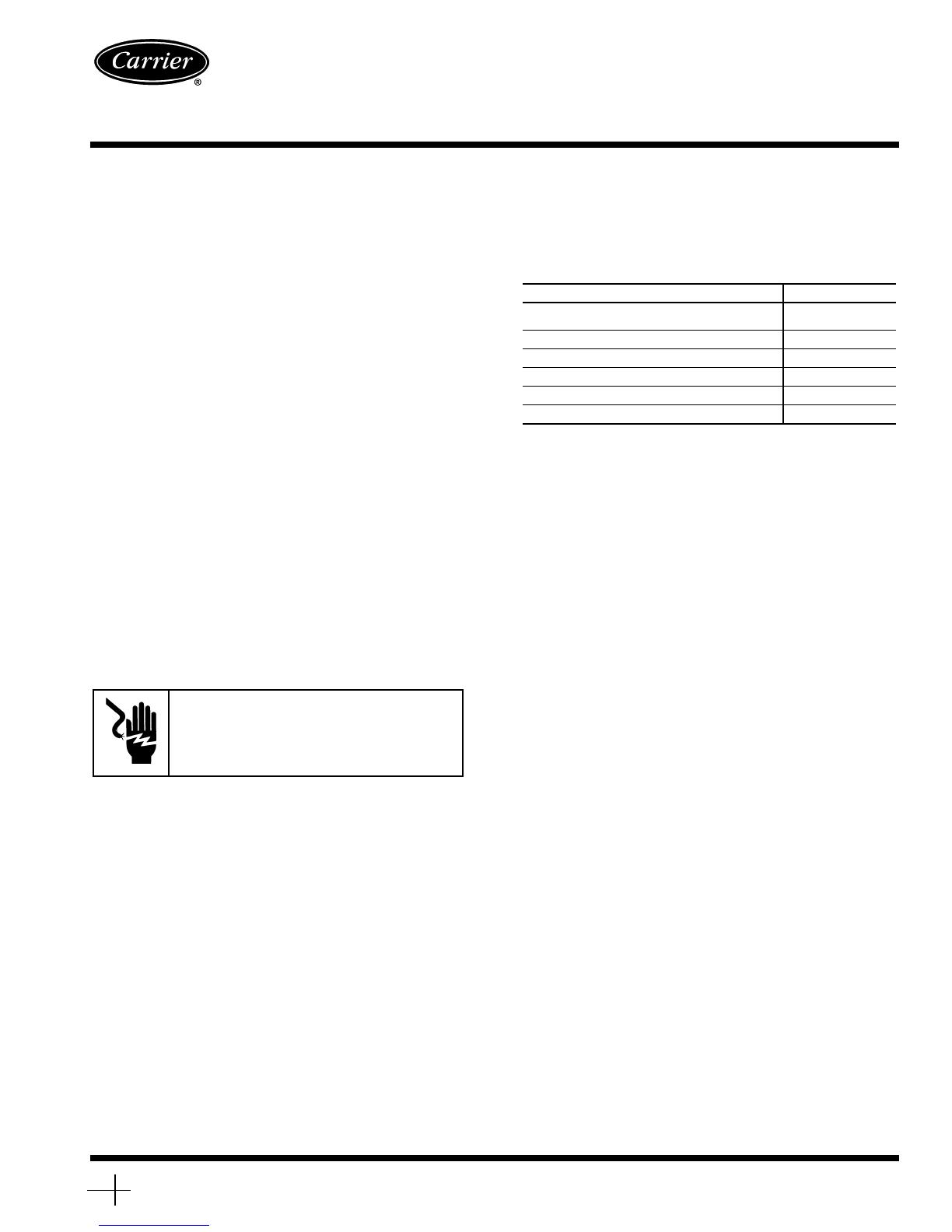
Manufacturer reserves the right to discontinue, or change at any time, specifications or designs without notice and without incurring obligations.
PC 903 Catalog No. 533-076 Printed in U.S.A. Form 30GTN-3SI Pg 1 6-99 Replaces: New
Book 2
Tab 5c
Installation Instructions
Part Number 30GT-911---060
CONTENTS
SAFETY CONSIDERATIONS. . . . . . . . . . . . . . . . . . . 1
INTRODUCTION . . . . . . . . . . . . . . . . . . . . . . . . . . . . . . . . 1
INSTALLATION . . . . . . . . . . . . . . . . . . . . . . . . . . . . . . 1-10
Install Harness and Make Wire
Connections. . . . . . . . . . . . . . . . . . . . . . . . . . . . . . . . . . 1
Configure Control (All Sizes). . . . . . . . . . . . . . . . . . 7
Temperature Reset (4 to 20 mA). . . . . . . . . . . . . . . 8
Demand Limit (4 to 20 mA) . . . . . . . . . . . . . . . . . . . . 9
Demand Limit (Switch Controlled) . . . . . . . . . . . 10
SAFETY CONSIDERATIONS
Installation of this accessory can be hazardous due to sys-
tem pressures, electrical components, and equipment location
(such as a roof or elevated structure).
Only trained, qualified installers and service technicians
should install, start up, and service this equipment (Fig. 1).
When installing this accessory, observe precautions in the
literature, labels attached to the equipment, and any other
safety precautions that apply.
• Follow all safety codes.
• Wear safety glasses and work gloves.
• Use care in handling and installing this accessory.
INTRODUCTION
The Energy Management Module Accessory (EMM) pack-
age is required for additional Temperature Reset, Demand
Limit, and Ice Done features of the ComfortLink™
30GTN,GTR and 30GUN,GUR chillers. Temperature Reset
function by return water, outside air or space temperature do
NOT require the addition of this accessory. The following ad-
ditional features are supported by this accessory:
• temperature reset by 4 to 20 mA field supplied signal.
• demand limit control via field supplied two-step switch
input.
• demand limit control via field supplied 4 to 20 mA
signal.
• support of unoccupied operation for ice making through
field supplied contacts.
Accessory Package Contents
INSTALLATION
1. Inspect the package contents for missing or damaged
parts. File a claim with shipping agency if parts are
damaged. Notify your Carrier representative if any
items are missing.
2. Open and tag all electrical disconnects.
3. Open the left side control box door to access the con-
trol wiring side of box.
4. Using the five no. 6 screws provided in the package,
mount the EMM in the pre-drilled holes in the control
panel near the lower left corner of the display/fuse
bracket. See Fig. 2. Using the two no. 10 screws pro-
vided in the package, mount the terminal block above
the EMM board.
5. For size 130-210 machines (and modules 230A-420A,
330B-420B), mount the EMM board above TB5. See
Fig. 3.
6. The board addresses are set through 4-position DIP
switches. All switches are set to ON for all boards. See
Fig. 1.
Install Harness and Make Wire Connec-
tions — Locate harness supplied with accessory. use the
30GT415088 harness for 040-110 sizes (and modules 230B-
315B). Use the 30GT415224 harness for 130-210 sizes (and
modules 230A-420A and 330B-420B).
Make four plug connections at the EMM using the connec-
tors labeled EMM-J1, J4, J6, and J7. See Fig. 4 and 5.
Two remaining plug connections need to be made. Connect
the plug labeled 30GT415224 at the Main Base Board (MBB)
for all 040-110 sizes. Connect the plug labeled EXV-J3/MBB-
J3 at the Expansion Valve Board (EXV), if installed for 040-
110 sizes. Otherwise, connect the plug to the Main Base Board
(MBB). See Fig. 4.
For sizes 130-210 connect the plug labeled MBB-J2/
CXB-J2 to the Main Base board (MBB) or to the Expansion
Board (CXB, if installed) and connect the plug labeled EXV-J3
CXB-J3 at the Expansion Board (CXB, if installed). Other-
wise, connect the plug to the Expansion Valve Board (EXV).
See Fig. 5.
ELECTRIC SHOCK HAZARD.
To avoid the possibility of electrical shock,
open and tag all disconnects before installing
this equipment.
ITEM QUANTITY
Energy Management Module,
30GT515218 1
Terminal Block, HY84FE029 1
Screws, no. 6 3/4-in. long 5
Screws, no. 10 3/4-in. long 2
Harness Assembly, 30GT415088 1
Harness Assembly, 30GT415224 1
30GTN,GTR,GUN,GUR040-420
Energy Management Module (EMM)
Accessory
50/60 Hz