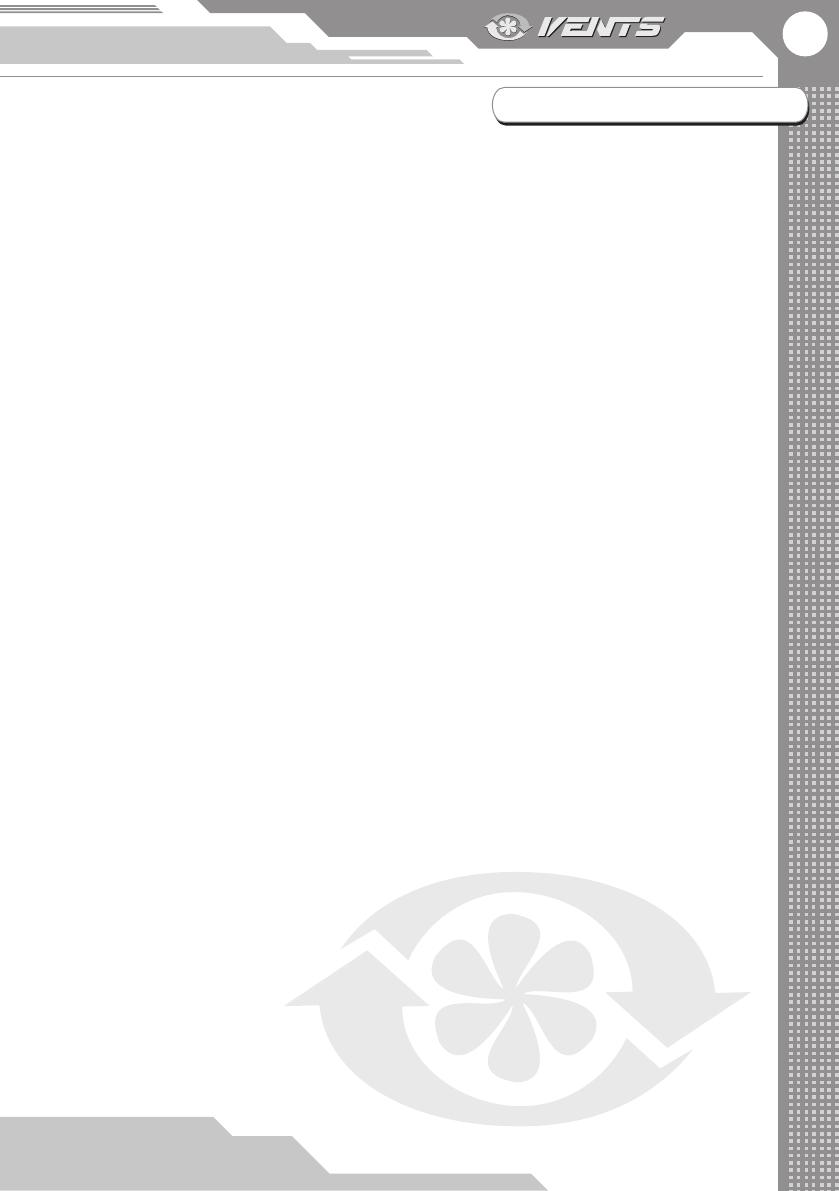
19
TECHNICAL MAINTENANCE
The unit requires maintenance works 3-4 times per year. Maintenance includes regular cleaning and
the following operations:
1. Filter maintenance (3-4 timed per year).
Dirty lters increase air resistance in the system and reduce supply air volume. Clean the lters as
required but at least once in 3-4 months. Use a vacuum-cleaner to remove the contamination or use a
new lter. Contact your seller for new lters.
Filter removal procedure (Fig. 19):
1. Remove four bolts with handles.
2. Open the unit access door and remove 2 M6 screws to release the stoppers. Shut the unit access
door ad lift it upwards to remove it from the supports.
3. Remove the heat exchanger from the unit by pulling its bend.
4. Remove the extract and supply lter.
Install the lters in reverse orders.
2. Heat exchanger inspection (once per year).
Some dust can get accumulated on the heat exchanger block even in case of regular maintenance
of the lters. To maintain the high heat exchange eciency, regular cleaning is required. To clean the
heat exchanger pull it out of the unit and ush it with warm soap or mild detergent water solution. Re-
install the dry heat exchanger to the unit.
3. Fan inspection (once per year).
Even in case of regular lter maintenance, some dust and grease can get accumulated inside the
fans and reduce the unit performance and supply air ow.
Clean the fans with a soft brush or cloth. No water and abrasive detergent, sharp objects or solvents
are allowed for cleaning to prevent the impeller damage.
4. Condensate drainage (once per year).
The drain pipes may get clogged with extracted particles. Pour some water inside the drain pan and
check the pipe for clogging. Clean the U-trap and drain pipe if required.
5. Supply air ow control (twice per year).
Leaves and other pollutions can clog the supply air grille and reduce the unit performance and
supply air volume. Check the supply grille twice per year and clean it as required.
6. Ductworks inspection (once in 5 years).
Even regular technical maintenance of the unit may not completely prevent dirt accumulation in
the air ducts, which impairs the unit performance. The air duct maintenance mens their regular cleaning
or replacement.
7. Control Unit Maintenance (as required).
The control unit must be serviced by an expert qualied for unassisted operations with electrical
installations up to 1000 V and made familiar with the present operation manual. Disconnect the unit
from the power mains prior to the control unit maintenance.
Control unit maintenance sequence (Fig. 20):
1. Take the unit access door and remove the heat exchanger.
2. Remove the self-tapping screws to release the protecting cover.
3. Remove the self-tapping screws securing the swivel control unit panel.
4. Remove the control unit lid.