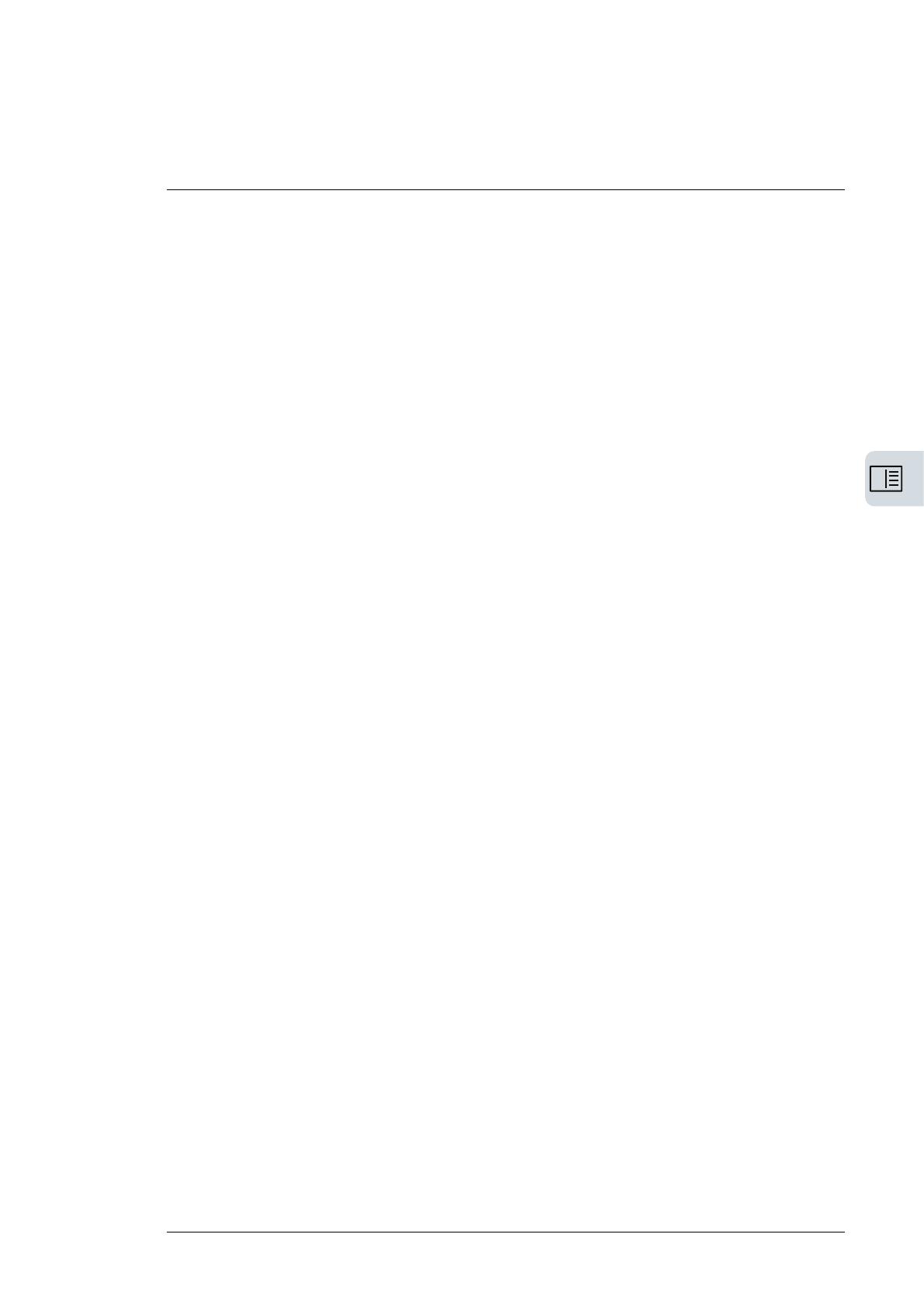
Table of contents
1 Introduction to the manual
7Contents of this chapter ..........................................................................
7Applicability ........................................................................................
7Target audience ...................................................................................
7Terms and abbreviations .........................................................................
8Related documents ...............................................................................
8ACS880 single drive modules ...............................................................
8ACS880 single drive cabinets ...............................................................
8ACS580, ACH580 and ACQ580 drive modules ..........................................
8AH580-07 and ACQ580-07 cabinets ...........................................................
2 Electrical planning guidelines
11Contents of this chapter ..........................................................................
11Limitation of liability ...............................................................................
11Selecting the supply disconnecting device ....................................................
11Cabinets ........................................................................................
11Modules .........................................................................................
11European Union ............................................................................
12North America ..............................................................................
12Other regions ...............................................................................
12Selecting the main contactor (breaker) ........................................................
12Cabinets ........................................................................................
12Modules .....................................................................................
12Examining the compatibility of the motor and drive ..........................................
13Protecting the motor insulation and bearings .............................................
13Requirements table ...........................................................................
15Availability of du/dt filter and common mode filter by drive type ....................
16Additional requirements for explosion-safe (EX) motors .............................
16
Additional requirements for ABB motors of types other than M2_, M3_, M4_, HX_
and AM_ .....................................................................................
16Additional requirements for braking applications ......................................
16Additional requirements for the regenerative and low harmonics drives ..........
16Additional requirements for ABB high-output and IP23 motors .....................
16Additional requirements for non-ABB high-output and IP23 motors ................
17Additional data for calculating the rise time and the peak line-to-line voltage ....
19Additional note for sine filters ............................................................
19Selecting the power cables ......................................................................
19General guidelines ............................................................................
20Typical power cable sizes ....................................................................
21Power cable types .............................................................................
21Preferred power cable types .............................................................
21Alternate power cable types ..............................................................
22Not allowed power cable types ..........................................................
22Additional guidelines, North America .......................................................
23Metal conduit ...............................................................................
23Power cable shield ............................................................................
Table of contents 5