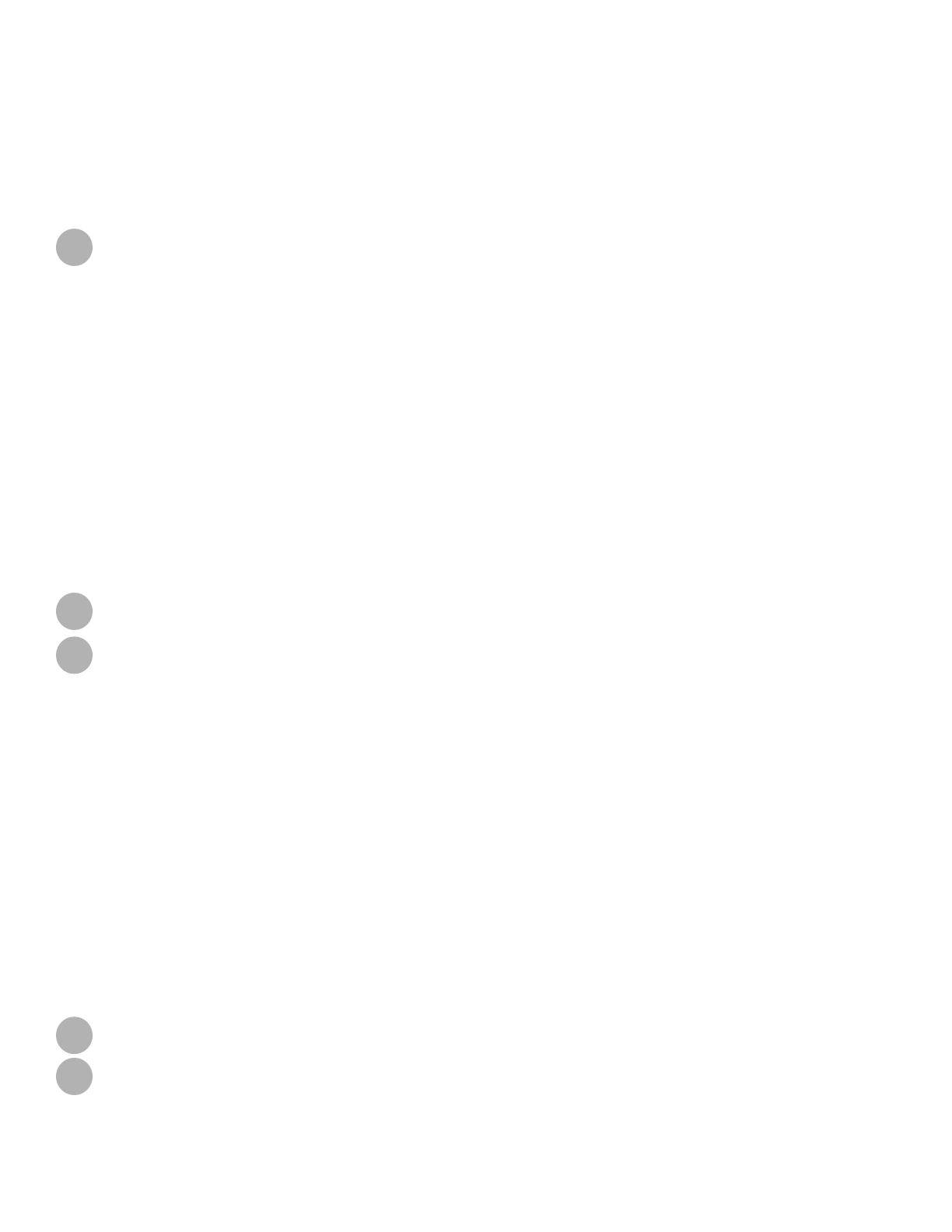
3D Systems, Inc.
3
ProX 800 Printer - Inside View ..........................................................................18
Material Delivery Module (MDM)...........................................................................20
Print Mode ..........................................................................................20
Stand-by Mode .......................................................................................20
MDM Capacity .......................................................................................20
Material Container ....................................................................................20
Printhead Overview ......................................................................................23
User Interface...........................................................................................24
Light Stack..............................................................................................25
Manual Ooad Cart .....................................................................................25
SOFTWARE OVERVIEW ................................................................................26
Home Screen............................................................................................26
Status Screen ...........................................................................................27
Print Queue Screen ......................................................................................28
Print History Screen......................................................................................29
Detail Pop-up Screen .....................................................................................30
Material Status Screen....................................................................................31
Tools Menu Screen.......................................................................................32
Elevator/Leveler Settings Screen ...........................................................................33
Print Applicator Screen ...................................................................................34
Printhead Settings Screen ................................................................................35
Settings Screen..........................................................................................36
Manual Printer Connection Screen .........................................................................37
Printer Information Settings Screen ........................................................................38
Network Settings Screen..................................................................................38
Heater Settings Screen ...................................................................................39
Scale Factor Settings Screen...............................................................................40
Build Settings Screen.....................................................................................41
Drawing Settings Screen..................................................................................42
New Functionality for GUI v1.1.5443........................................................................42
3DSPRINT SOFTWARE OVERVIEW .......................................................................47
SYSTEM OPERATIONS .................................................................................48
Print Applicator Installation and Removal ...................................................................48
Print Applicator Cleaning .................................................................................49
Material Delivery Module (MDM) Installation ................................................................49
MDM Removal ..........................................................................................51
Material Delivery Module Temperature Control ..............................................................51
Auto Material Rell System................................................................................51
Installing Material Containers .............................................................................52
Material Container Removal...............................................................................53
Setting the Ooad Position ...............................................................................54
Printing a Part...........................................................................................56
Home the Elevator ....................................................................................56
Setting the Start Position ..............................................................................57
To Set the Start Position: ...........................................................................57
Removing Bubbles ....................................................................................58
Selecting a Print Job and Printing the Part ...............................................................58
Drain the Build Platform ...............................................................................59
Installation of Print Platform Without Ooad Cart ........................................................60
Installation of Print Platform With Ooad Cart ...........................................................61
Remove Print Platform Without Ooad Cart .............................................................62
Remove Print Platform With Ooad Cart ................................................................63
POST-PROCESSING BUILD PARTS .......................................................................64
MAINTENANCE ......................................................................................67
Dust Removal ...........................................................................................67
Preventive Maintenance . . . . . . . . . . . . . . . . . . . . . . . . . . . . . . . . . . . . . . . . . . . . . . . . . . . . . . . . . . . . . . . . . . . . . . . . . . . . . . . . . . 67
Customer Preventive Maintenance.........................................................................67
Cleaning the Print Applicator ...........................................................................67
Replace the Tubing in the Peristaltic Pump ...............................................................68
10
11
12
13
14