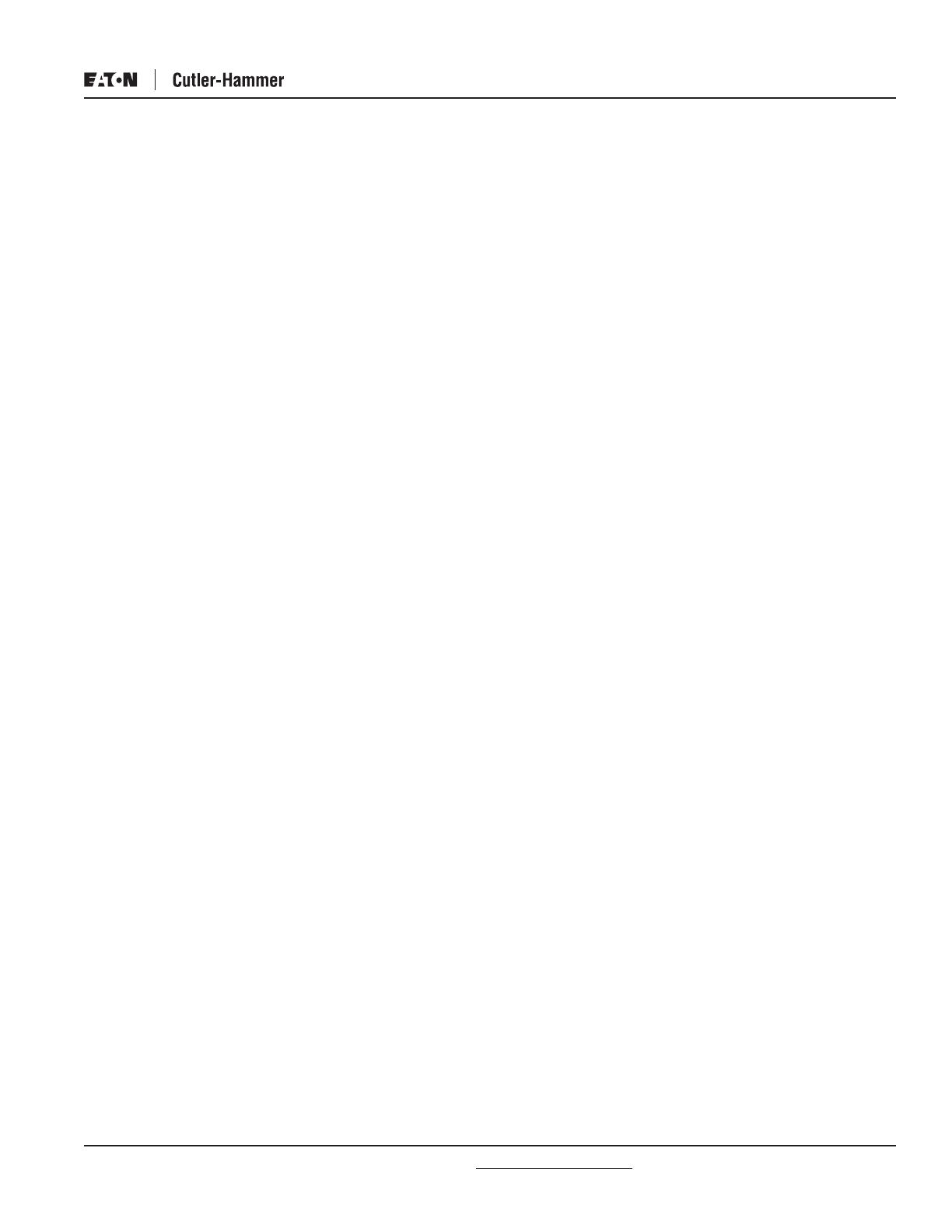
For more information visit: www.cutler-hammer.eaton.com
Page 2-1
IL17562BH04Effective 10/02
SECTION 2—PRODUCT OVERVIEW
2.0 General Overview
The MP-3000 Motor Protection Relay is available in either a fixed
mount, semi-flush case or in a semi-flush Quick Release drawout case.
Both housings are compact and fit a standard IQ cutout.
The optional Quick Release drawout case features 2-stage contact
disconnects and self-shorting Ct circuit terminal blocks. A spare self-
shorting terminal pair is available for use as relay removal alarm, or to
keep the contactor energized for continuous motor operation on relay
removal. The optional communication module (PONI) is externally
mounted on the fixed mount case and internally mounted in the
drawout case.
The MP-3000 has three phase current inputs and one ground current
input. Both 5 A and 1 A versions are available. The ground protection
and metering functions are best used with a zero-sequence ground Ct,
rather than from the residual connection of the phase Cts - the zero
sequence ground Ct provides greater ground fault sensitivity. The unit
is user programmable for 60 Hz or 50 Hz operation.
The MP-3000 has 2 discrete inputs, 4 form c (1 N.O. and 1 N.C.) output
contacts, and one 4 to 20 ma analog output. The relay lets the user
program the operation of all the I/O points except for the trip output. In
addition, the relay has 10 LED’s for the indication of protection on,
program mode, monitor mode, view setting mode, history mode, log
mode, trip, alarm, Aux 1 and Aux 2 output relay operation. A test page
in the program mode provides display indication of the discrete input
states and testing of the output relays, target LED’s and analog output
circuit.
A user-friendly operator interface provides quick access to the
settings, monitored values, motor history and operational logs. A large
LED alphanumeric display provides easy viewing from any angle.
Simple keypad operations provide quick and easy navigation through
all settings and stored data. The program mode and emergency
override buttons are access restricted via a seal and latched cover. An
integrated context-sensitive help button provides an online descriptive
display of functions, abbreviations and operations.
2.1 Optimum Motor Protection
The MP-3000 Motor Protection Relay has been designed for maximum
motor utilization and protection. It is desirable to run the motor as close
as possible to its design limits, while protecting it against excessive
heating and damaging overload conditions. The MP-3000 has field
proven protection algorithms developed from basic motor design
principles and operating parameters
The MP-3000 protects against rotor and stator overheating, short
circuits or insulation faults, excessive starting duty, and abnormal
operating conditions.
2.1.1 Intel-I-Trip (Adaptive I
2
t Motor Overload Protection)
Motor operation is typically limited by the rotor thermal capabilities, but
the measuring quantities are stator currents. This requires accurate
measurements and good motor thermal models to provide maximum
utilization and reliable protection.
The MP-3000 uses the field-proven Intel-I-Trip overload measurement
and motor thermal protection model that uses the manufacturer’s
nameplate data to develop an overload protection curve specifically for
the motor being protected. When RTDs are used, the Intel-I-Trip
overload protection curve becomes adaptive. The overload trip times
will change based on the modeling impact of the motor’s internal
temperature data. It also trips directly for high stator temperature.
The relay samples the current waveforms 36 times per cycle providing
accurate measurements of the positive and negative sequence
currents, as well as harmonic components which add to rotor and
stator heating. The negative sequence component of current causes
far greater heating effect on the rotor and has a greater impact on the
thermal model in the relay, as compared to the balanced or positive-
sequence component.
2.1.2 Instantaneous Overcurrent Protection
The MP-3000 has instantaneous phase overcurrent function to trip the
motor for fault currents, sometimes saving the fuses for medium-
current faults. This function can be disabled and has an adjustable time
delay on starting to avoid nuisance tripping on inrush.
2.1.3 Phase Unbalance Protection
Motor supply circuits are often fed through fuses and may be ener-
gized with one fuse blown, causing single phasing the motor. The MP-
3000 measures the current unbalance and can be used to alarm or trip
the motor before heating and a thermal-model trip. Pickup, start and
run timers, and separate alarm settings, are provided.
2.1.4 Ground Fault Protection
A separate measuring circuit is used to measure ground current. A
ground Ct is recommended for more sensitive protection against
winding insulation failure to ground. The relay ground Ct input can be
connected residually from the three phase Cts, but with much inferior
protection sensitivity. The ground fault protection has adjustable pickup
and time delay set points or can be disabled.
2.1.5 Jam Protection
The user-selectable Jam function protects motors that are running
against a sudden mechanical jam or stall condition. The common
application is on motors used on crushers, chippers or conveyors. It
detects an increase of motor current to a level above full load. Pickup,
start and run timers and a separate alarm setting are provided.
2.1.6 Underload Protection
The user selectable under-load function is used to detect the loss of
load on the motor. Coupling failure is a common cause for loss of load.
Pickup, start and run timers and a separate alarm setting are provided.
2.1.7 Remote and Differential Trip
One of the discrete inputs can be programmed to accept a contact
input from a separate differential relay or other device to trip the motor.
This provides local and remote target (logging) information, and utilizes
the trip contacts of the MP-3000. It will also record and log the motor
information at the time of the trip.
2.1.8 Zero-Speed Switch Trip
One of the discrete inputs can be programmed to accept a contact
input from a zero-speed switch connected to the motor shaft. This
provides faster tripping for a motor which remains completely stalled
when energized for a start. It provides backup protection for motors
with long acceleration timing.
2.2 Motor Starting and Control Functions
The MP-3000 Motor Protection relay includes logic to control the
number of starts that can occur on the motor in a given time period for
cold and hot motor conditions. Settable timers are provided to control
the time between starts and to restart a motor after a stop. Additional
logic is included for transition control of reduced-voltage starters.