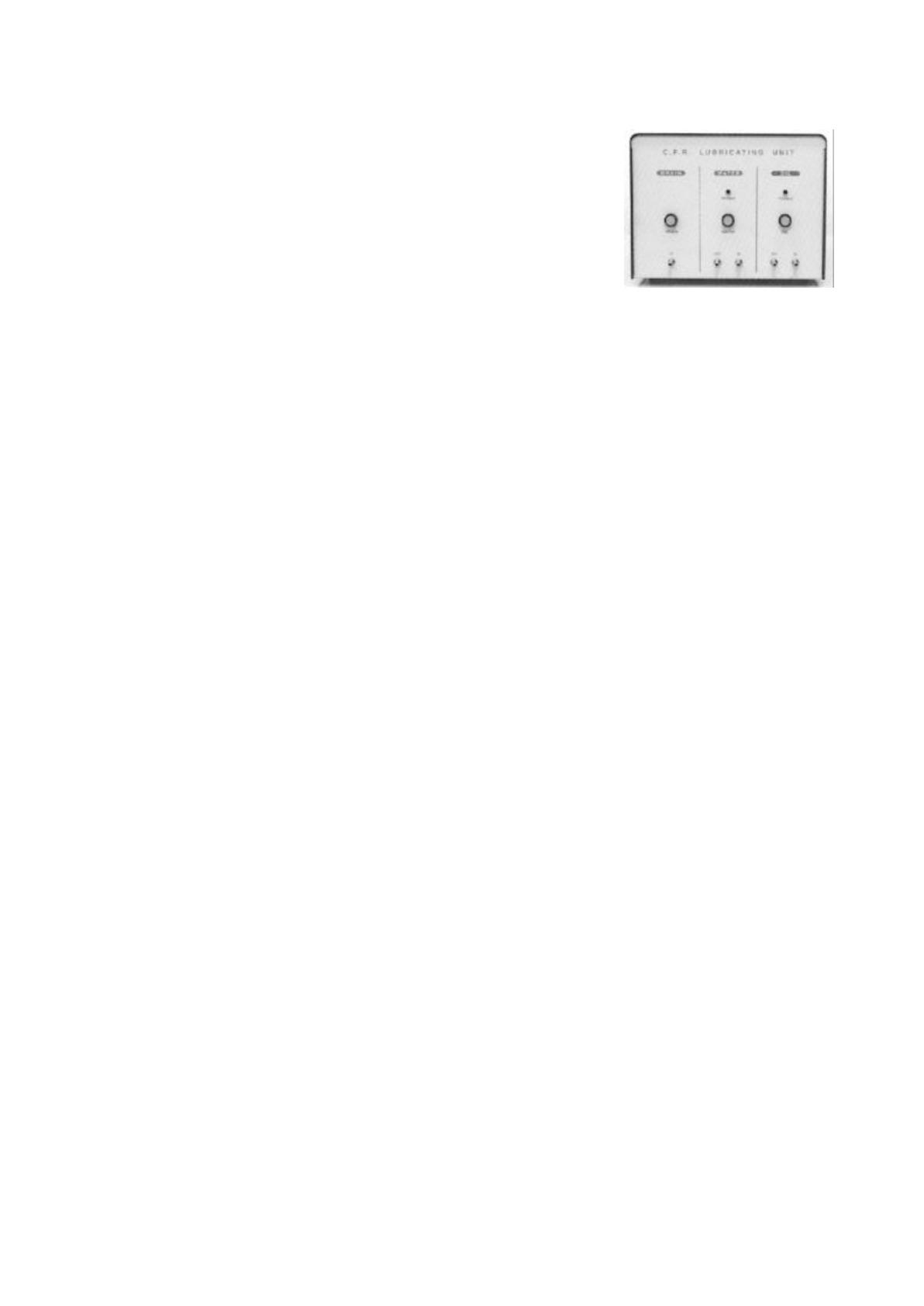
-9-
(2) Function
Lubricating unit assembly works as follows.
l Supplies lubricating oil to seal attachment assy.
l Sucks and recovers waste oil discharged from the bearing
housing assembly.
l Detects a malfunction when there is trouble in the supply
of lubricating oil or cooling water.
l When this safety device activates, solve the problem
quickly.
(3) Operation and the maintenance
1) The lubricating unit assembly is mounted on the centrifuge .
2) The power of this unit is 100-240 V of single-phase AC.
Please, connect the plug of the AC adapter with it.
3) Supply lubricating oil (P/N 463152) to the OIL bottle for lubricating oil by about 400 ml.
Check lubricating oil quantity every time it uses.
If becoming below the half of the bottle, replenish.
4) The switch of the control panel has the following function.
l The OIL switch is the ON-OFF switch of the lubricating oil pump.
Also, it is the ON-OFF switch of the lubricating oil flow abnormal detection equipment.
When the flow of lubricating oil stops, it informs in the buzzer sound.
When making this switch OFF, the buzzer sound stops.
l The WATER switch is the ON-OFF switch of the cooling water flow abnormal detection
equipment. When the flow of cooling water stops, it informs in the buzzer sound.
When making this switch OFF, the buzzer sound stops.
l The DRAIN switch is the ON-OFF switch of the waste oil suction pump.
l Please check the waste oil quantity of the DRAIN bottle after operation.
The operation procedure of each switch is being explained at this instruction manual.
When operating a rotor, operate according to them.
Fig.11 Lubricating unit