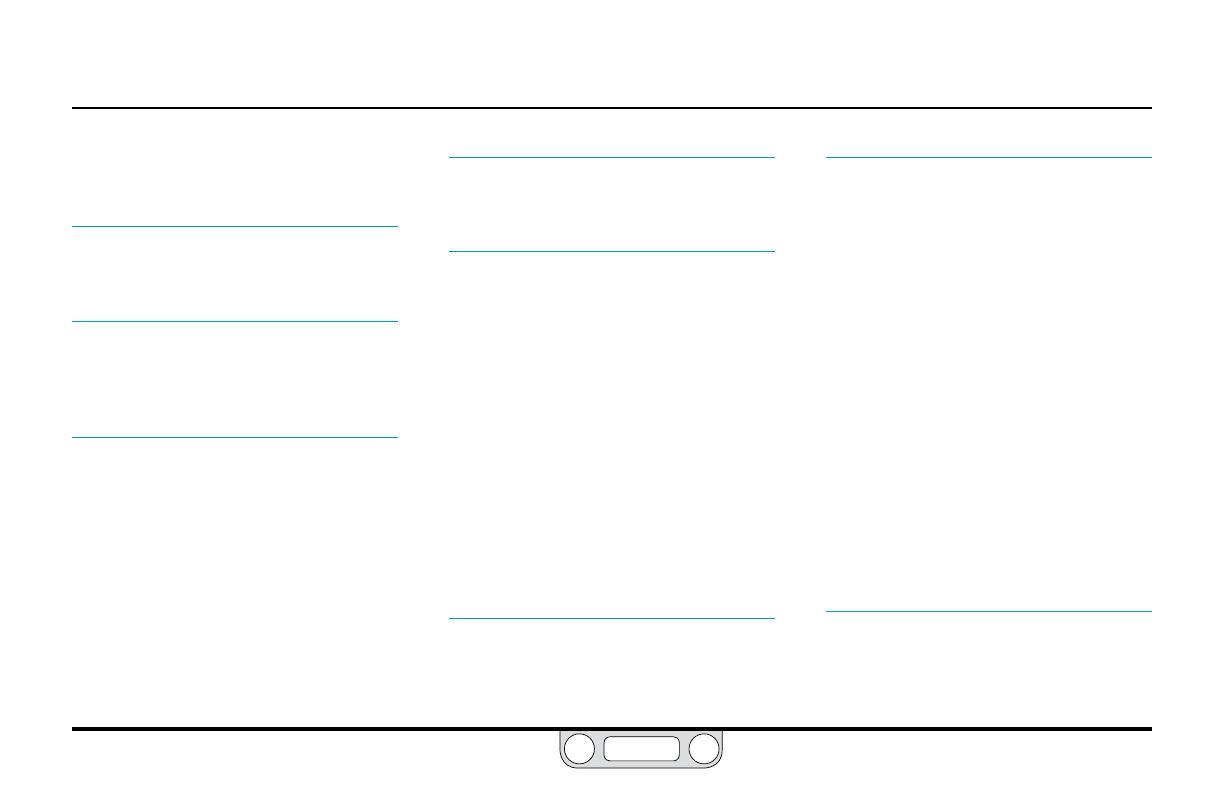
ER5000 —
10
Table of Contents
www.emerson.com/tescom
Table of Contents
Safety, Installation & Operations
Precautions 2
TESCOM™ ELECTRONIC CONTROLLERS . . . . . 3
TESCOM REGULATORS . . . . . . . . . . . . . 6
Table of Contents 9
Table of Contents . . . . . . . . . . . . . . . 10
Conventions of This Manual . . . . . . . . . . 13
Navigating This Manual . . . . . . . . . . . . 13
Features and Specifications 14
ER5000 Series Part Numbering System . . . . 15
ER5000 Standard Features . . . . . . . . . . 15
ER5000 Dimensions – Side Views . . . . . . . 16
ER5000 Dimensions – Top and Bottom View . . 17
ER5050 Hazardous Location Model . . . . . . 18
Dimensions – Side Views . . . . . . . . . . . 18
ER5050 Hazardous Location Model . . . . . . 19
Dimensions – Top and Bottom View . . . . . . 19
ER5000 Specifications . . . . . . . . . . . . 20
Hazardous Location Model (ER5050)
Specifications . . . . . . . . . . . . . . . . 22
Accessories . . . . . . . . . . . . . . . . . . 24
What’s New 25
New Features . . . . . . . . . . . . . . . . . 26
Replacing an ER3000 with an ER5000 . . . . . 27
How It Works 29
The ER5000: How It Works . . . . . . . . . . 30
Understanding PID Controllers . . . . . . . . 31
PID Controllers: Three Components
Are Better Than One 32
A Typical PID Control System 33
Tuning a PID Controller 35
Rules of Thumb for PID Tuning 35
The ER5000: Typical Application
(Non-Hazardous Location) . . . . . . . . . . 39
Controlling System Pressure 39
A Note Concerning Non-Venting
Regulators in Closed Loop Applications 41
Monitoring System Control Limits 42
The ER5000: Control Modes . . . . . . . . . . 43
Internal Feedback Mode 43
External Feedback Mode 43
Cascade Mode 43
Glossary of Terms 44
Terms Relating to PID Controllers
and Controller Tuning . . . . . . . . . . . . 45
Terms Relating to Regulators . . . . . . . . . 52
Getting Started 57
Before You Begin . . . . . . . . . . . . . . . 58
ER5000 Quick Reference: Jumpers,
Terminal Blocks and Wires and LEDs . . . . . 59
Verify your shipment . . . . . . . . . . . . . 60
Additional items not included: 61
Tools you will need for the installation: 61
Additional items and tool you will need for
an installation in a Hazardous Location: 61
Verify the configuration of your application . . . . 62
Verify that all operational requirements
have been met . . . . . . . . . . . . . . . . 63
Verify that all safety requirements
have been met . . . . . . . . . . . . . . . . 63
Mount the ER5000 on the regulator . . . . . 64
Connect and verify the power supply . . . . . 65
Verify the Jumper J6 configuration . . . . . . 68
Connect the USB cable
(not supplied with ER5050) 71
Install the ERTune
™
program . . . . . . . . . 72
Connect pressure to the system . . . . . . . . 73
Start up and tune the system . . . . . . . . . 75
Installation Variations 76
Before You Begin . . . . . . . . . . . . . . . 77
ER5000 Installation Variations —
Wiring Diagrams . . . . . . . . . . . . . . . 78
Terminal Blocks and Wires . . . . . . . . . . 79