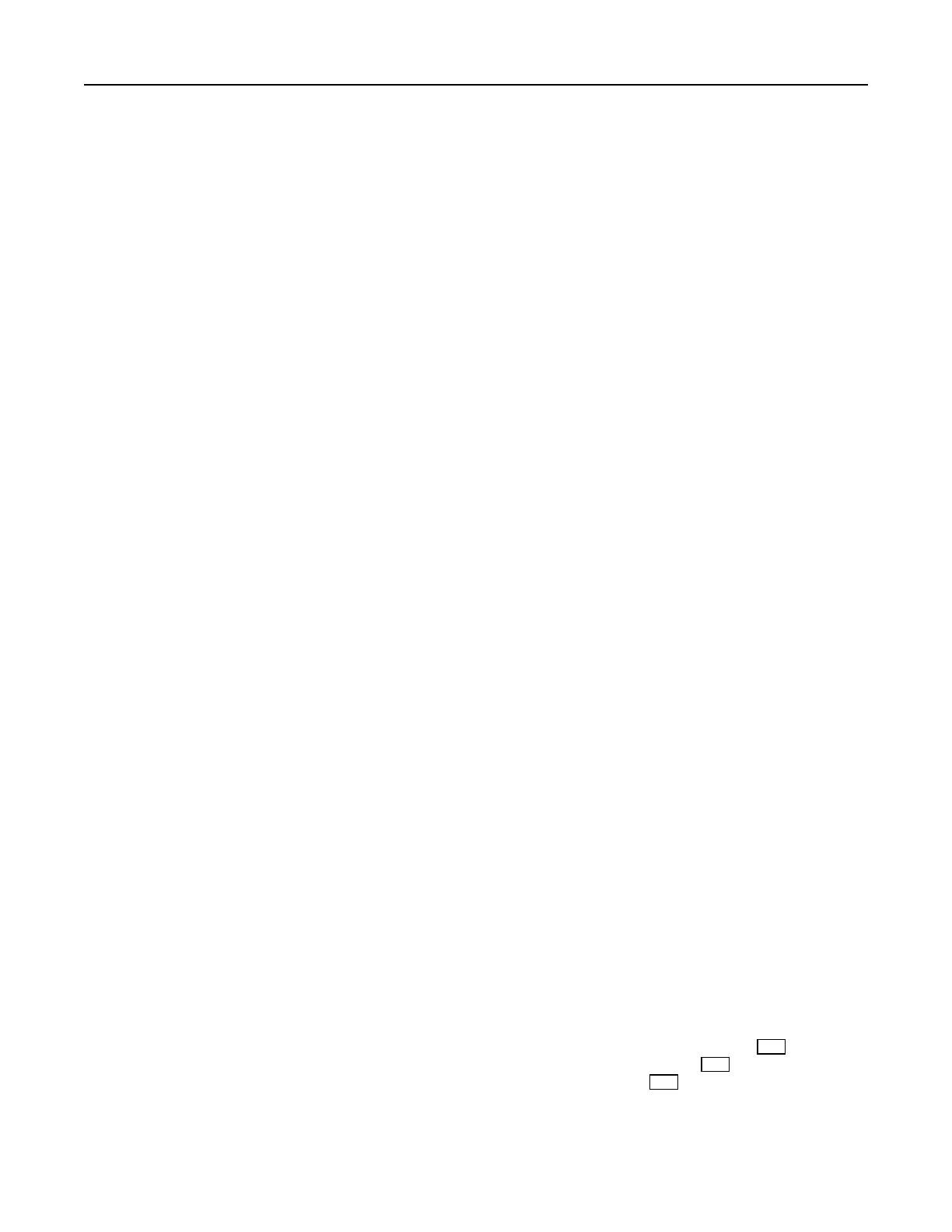
3
5693 982 - 04
Vitotronic 300, GW2B Installation and Service
General
Preparing for Installation
Control Unit Installation
Installation Sequence
Safety, Installation and Warranty Requirements..............2
Product Information....................................................2
Designations In The System Examples.........................6
System Example 1......................................................7
Single boiler system with Therm-Control...................7
Equipment required................................................8
Electrical installation scheme................................10
Mixing valve extension PCB..................................12
Required code....................................................12
System Example 2....................................................13
Single boiler system with shunt pump....................13
Equipment Required..............................................14
Electrical installation scheme................................16
Mixing valve extension PCB..................................18
Required code....................................................18
System Example 3....................................................19
Single boiler system with shunt pump and
3-way mixing valve..............................................19
Equipment required..............................................20
Electrical installation scheme.................................22
Mixing valve extension PCB..................................24
Required code.....................................................24
System Example 4....................................................25
Single boiler system with Vitocrossal.....................25
Equipment required..............................................26
Electrical installation scheme................................28
Mixing valve extension PCB..................................30
Required code.....................................................30
System Extension.....................................................30
Mounting the Control Unit..........................................31
Fitting the Control Unit Front......................................32
Opening the Control Unit...........................................33
Overview of Electrical Connections.............................34
Pump Connection Overview.......................................36
Inserting Cables and Applying Strain Relief...................37
Inserting the Boiler Coding Card.................................37
Inserting the LON Communication Module....................38
Adjusting the Fixed High Limit (if required)...................38
Changing the Adjustable High Limit (if required)...........39
Connecting Sensors...................................................39
Power Supply...........................................................40
External Connections.................................................41
Connecting Actuators................................................42
Connecting the Central Fault Message Facility..............43
Connection of Low Water Cut-off Device 150 ..............43
Connecting to Safety Equipment 150 ..........................43
External Burner Blocking 150 .....................................44
Page
Table of Contents