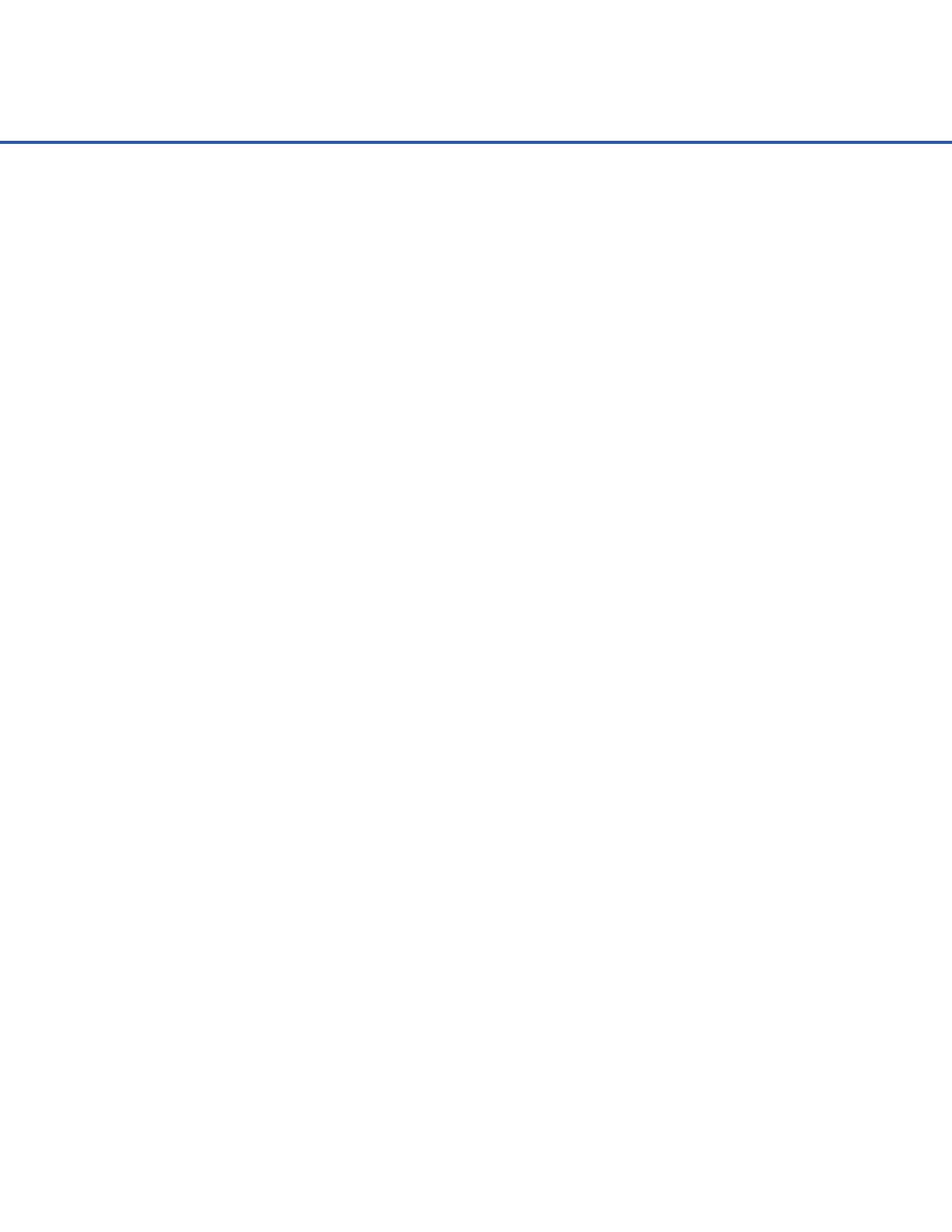
CONTENTS & WARRANTY
Warranty.................................................................................1
Chapter 1: Variables............................................................2
3
3
5
5
Chapter 2: Hardware & Installation..................................6
7
8
13
14
14
Chapter 3: Keypad / Display............................................16
17
21
21
Chapter 4: PC Menu Interface Operation.....................25
26
27
Chapter 5: Miscellaneous System Setup......................28
29
31
33
Chapter 6: Serial Port Options........................................37
41
Chapter 7: System Configuration Files.........................43
44
45
Chapter 8: System Status Menus / Options.................50
51
Chapter 9: Scanning Options..........................................58
59
Chapter 10: Built-in / Remote Stage Setup..................61
62
62
64
64
64
Chapter 11: Analog Inputs / 5-Volt Excitation.............66
67
67
69
69
70
70
71
Chapter 12: Digital I/O.....................................................72
73
74
Model Specific Features.....................................................
What’s In The Box................................................................
Modes of Operation...........................................................
Operating Auxilary Outputs..............................................
Front Panel Description......................................................
Panel Descriptions..............................................................
Sample Installations..........................................................
Testing the Installations....................................................
Hardware Revision Detection..........................................
Keypad / Display Operation.............................................
Familiarization...................................................................
Main Menu Description...................................................
PC Menu General Operations.........................................
Main Menu Screen............................................................
System Setup.....................................................................
Time Sync Options............................................................
Advanced System Setup Options...................................
Serial Port Hardware Description....................................
Configuration Files Menus...............................................
Sample Configuration File...............................................
Status Menus......................................................................
Scanning Menus................................................................
Stage / Temperature Menus.............................................
Stage Options (H-350XL Only)........................................
PtTmp Sensor Setup (H-350XL Only).............................
Remote Stage Setup Overview.......................................
Remote Stage Menus.......................................................
Analog Menus...................................................................
Analog Options................................................................
Analog Input Connections..............................................
Analog Inputs and Analog Ground Connections.........
Switched +5.00 Volt Reference Excitation.....................
Analog Input Setup Examples.........................................
Two Point Calibration Basics...........................................
Digital I/O Menus..............................................................
Digital I/O Options...........................................................
77
Chapter 13: Counter & Frequency Outputs.................79
80
83
Chapter 14: SDI-12 Operations.......................................84
88
90
92
93
93
94
95
Chapter 15: Logging Options.......................................101
Chapter 16: Operation with GOES Radio...................110
112
116
120
122
126
129
131
132
132
134
137
Chapter 17: ALERT Radio Operation...........................139
141
145
Chapter 18: 4 to 20 Milliamp Output..........................146
148
Chapter 19: Alarm Call Out...........................................149
Chapter 20: Data Card options.....................................154
Chapter 21: Operation with H-355/H-3551T............162
167
Chapter 22: Functions.....................................................168
170
171
173
174
174
174
175
175
176
Chapter 23: Maintenance / Troubleshooting............177
178
181
Quadrature Shaft Encoder Options................................
Counter and Frequency Menus......................................
Frequency Options...........................................................
SDI-12 Transparent Mode and Full Screen Mode.........
SDI-12 Sensor Mode........................................................
H-310 Setup......................................................................
SDI -12 Sensor Mode Supported Commands..............
SDI-12 Command and Response Protocol...................
Standard SDI-12 Command Set .....................................
H-350XL Supported Measurement Commands...........
Configuring the GOES Radio, General Options.........
GOES Self-Timed Options.............................................
Menus for Data Format set to SHEF..............................
Menus for Data Format set to BINARY.........................
GOES Random Options.................................................
GOES Diagnostics...........................................................
GOES Radio Setup Example..........................................
GOES Binary Data...........................................................
GOES Pseudo-Binary Look-up Table Instructions.......
Common GOES Terms...................................................
GOES Downlink Message Header Basics....................
ALERT Options................................................................
Special Cases for ALERT Transmissions.......................
4 to 20 Hardware Connections / Wiring......................
H-355/H-3551T Configuration......................................
Math Evaluator Operations............................................
Built-in Special Sensor Functions..................................
System Variables.............................................................
System Constants............................................................
Entering Functions..........................................................
User Defined Constants.................................................
Specific Purpose Functions............................................
Complex Functions.........................................................
Example Functions..........................................................
Troubleshooting..............................................................
Appendix A: Specifications...........................................