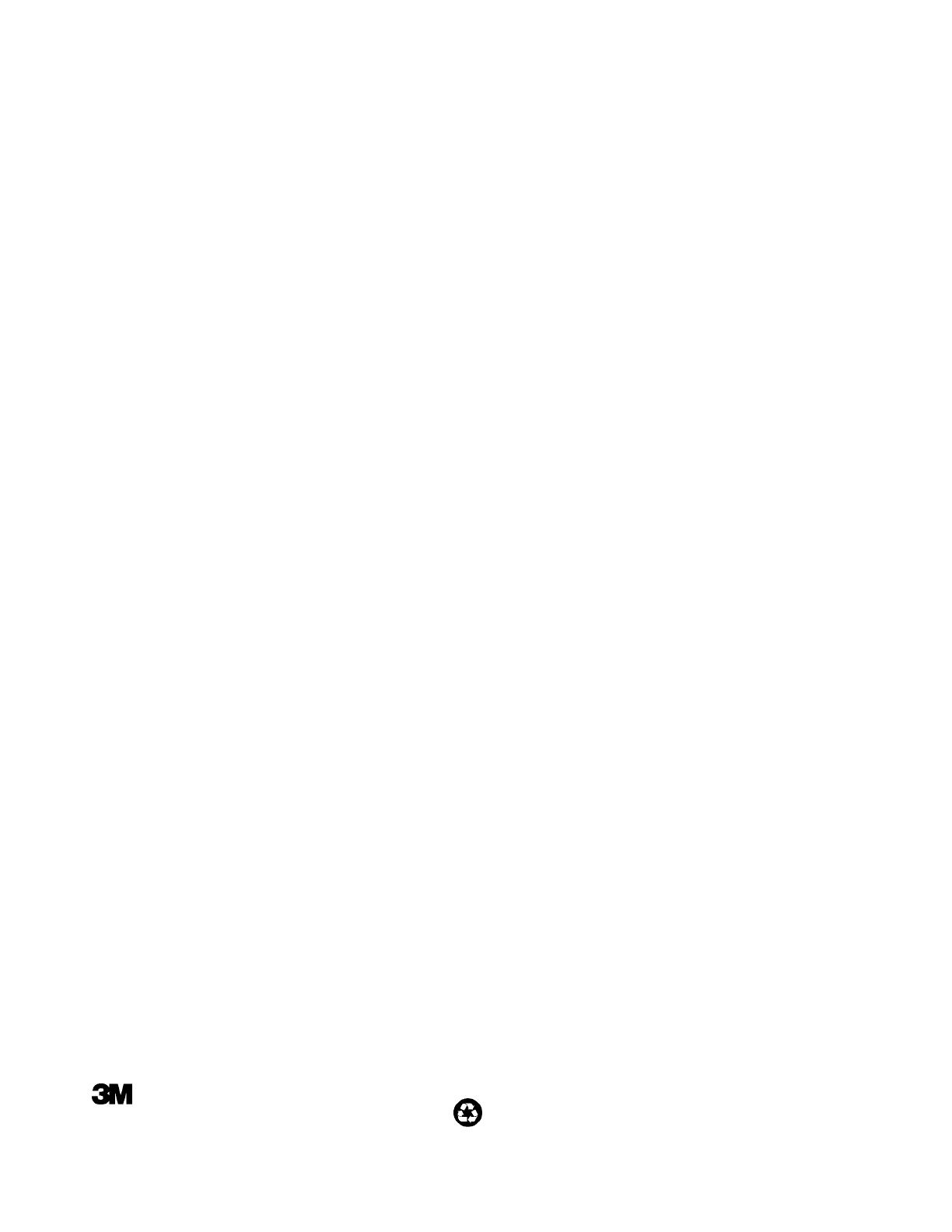
Important Notice to Purchaser:
22 89(9,3,498 9,*/40*(2 04-573(9054 (4+ 7,*533,4+(90548 7,2(9,+
95 9/, ",22,78 675+:*98 (7, )(8,+ 54 04-573(9054 ),20,;,+ 95 ),
7,20()2, ):9 9/, (**:7(*> 57 *5362,9,4,88 9/,7,5- 08 459
.:(7(49,,+ ,-57, :9020?04. 9/, 675+:*9 9/, :8,7 8/5:2+
+,9,7304, 9/, 8:09()0209> 5- 9/, 675+:*9 -57 098 049,4+,+ :8, #/,
:8,7 (88:3,8 (22 70818 (4+ 20()0209> </(985,;,7 04 *544,*9054 <09/
8:*/ :8,
4> 89(9,3,498 57 7,*533,4+(90548 5- 9/, ",22,7 </0*/ (7, 459
*549(04,+ 04 9/, ",22,78 *:77,49 6:)20*(90548 8/(22 /(;, 45 -57*, 57
,--,*9 :42,88 *549(04,+ 04 (4 (.7,,3,49 80.4,+ )> (4 (:9/570?,+
5--0*,7 5- 9/, ",22,7 #/, 89(9,3,498 *549(04,+ /,7,04 (7, 3(+, 04
20,: 5- (22 <(77(490,8 ,=67,88,+ 57 03620,+ 04*2:+04. ):9 459
20309,+ 95 9/, 03620,+ <(77(490,8 5- 3,7*/(49()0209> (4+ -094,88 -57
( 6(790*:2(7 6:7658, </0*/ <(77(490,8 (7, /,7,)> ,=67,882>
+08*2(03,+
"! " # # # $"! ! ' #!
!" $! ' #!' $ $# #
# # ! "#!# #' ! '
$!' ! ! ' !# ! " $# "
"$"# ! $!! ' !" # $" '
# "!" !$#" ## &! #%
6801 River Place Blvd.
Austin, TX 78726-9000
Electrical Products Division
Printed on 50% recycled
waste paper, including 10%
post-consumer waste paper.
09/5 04 $"
@