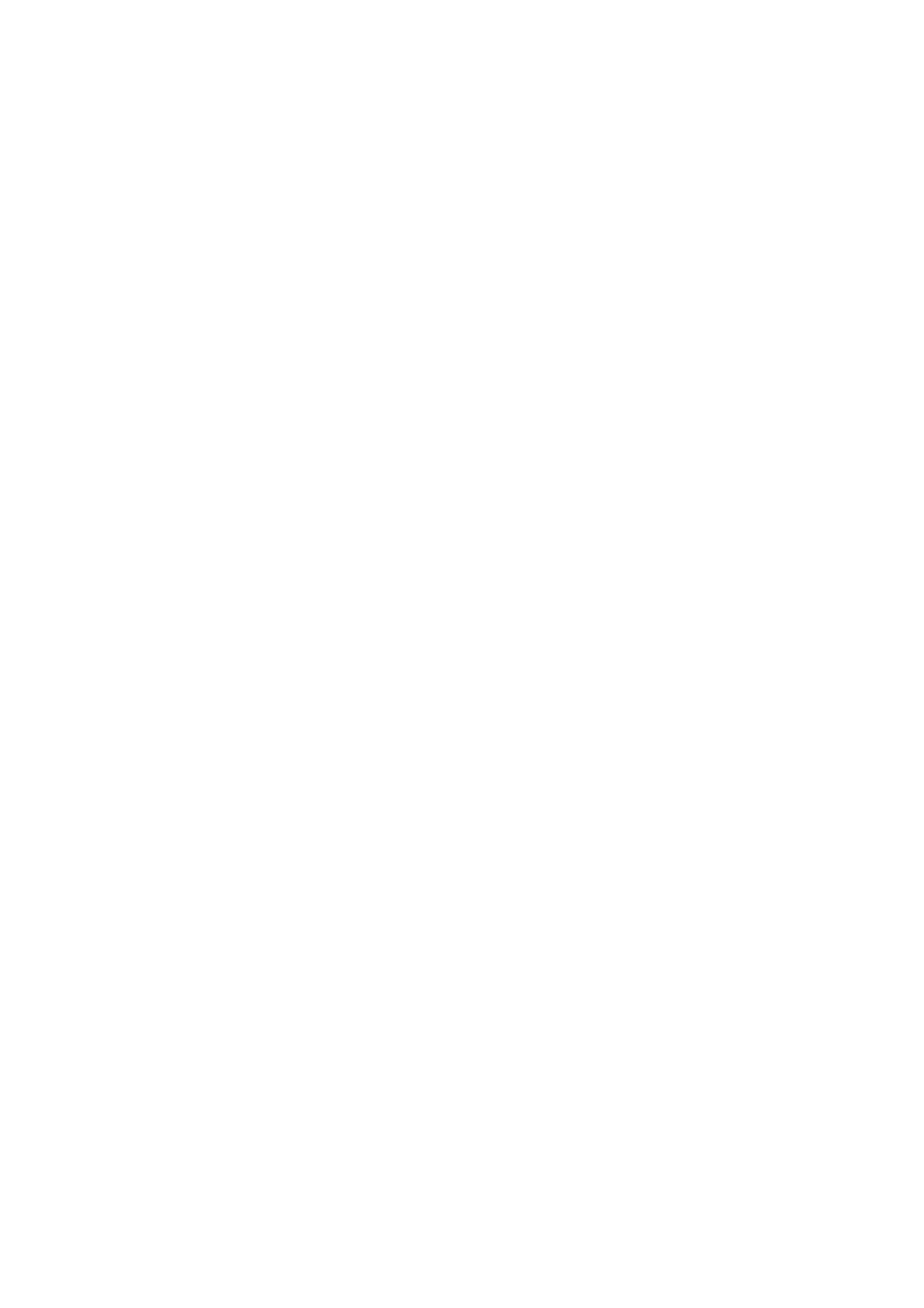
Miggytrac 1000 service manual
08.04.05
3
ver. GB1.0
1.5 Wheel (pos. 24 + 25)
The carriage has 4 wheels, each with two O-rings that make the friction to the surface.
Replacing the wheels:
Remove the outer side O-ring. Each wheel has a locking bolt (2,5mm socket headed hex bolt)
thru the wheel and the shaft.
1.6
Limit switch (pos. 2)
On each end of the carriage a limit switch is located. The switch stop both the movement of the
carriage and the welding process if a wire feeder is connected to the Burndy connector on the
front panel. The switch is “NO” (normally open).
Replacing the switch:
The limit switch is mounted into a threaded bore in the chassis. Unscrew the switch carefully.
The electrical connections are soldered (conn. “1” and “2”).
1.7
Magnet unit (pos. 33)
To make a light carriage as the Miggytrac 1000 stable, it’s equipped with an electro magnet in
the bottom of the chassis. To get the magnet source to the ground without loosing power and a
minimum of friction the magnet unit has 2 wheels. The magnet field is running in a loop between
one of the wheels – the plate/surface and back to the other wheel. Another advantages of this
system are no magnet field that influence on the welding process. The whole magnet unit is
spring loaded to make sure the carriage is moving as soft as possible.
The magnet unit is powered by a simple unregulated DC voltage (cpt. 2.1.C). The operator can
turn the magnet on/off with a switch on the front panel.
Removing the magnet unit:
The magnet unit is always a complete unit. Never try to dismantle it. Disconnect the power
supply. Place the carriage on the side. Remove the electronic unit (one screw on the top) and
disconnect the two cables “M” on the on the terminal block. Cut off the cable terminators (“M”)
on the end of the cable. Unscrew the 4 bolts on the bottom side of the carriage and place the
”electronic tower” carefully to one of the sides. Unscrew the 4 bolts on the top of the magnet
unit. Carefully pull the unit out and at the same time make sure that the cables are not blocked.
Magnet unit reassembly:
Try to slide the cables thru the hole in the bottom of the chassis and at the same time place the
new magnet unit in its position. Use a small portion of glume to lock the 4 bolts. Connect the
new cables back in the “M” position on the terminal block. Make a function test.
1.8
Maintenance
On each service remember to check:
Cleaning the wheels on the magnet unit.
Check the chain and lubricate with thin oil.
Check the O-rings, if necessary replace them.
Lubricate the guide wheels.