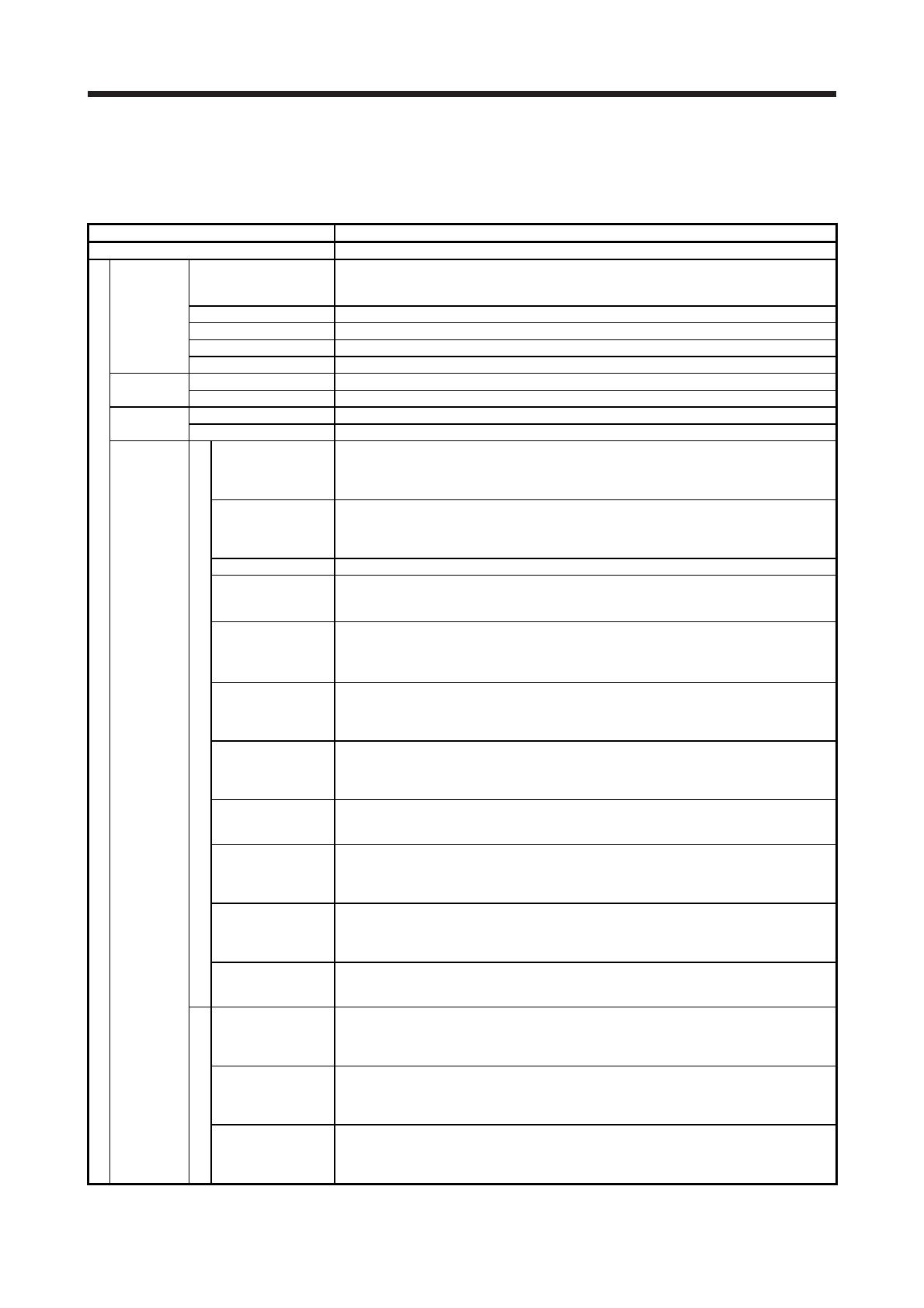
1. FUNCTIONS AND CONFIGURATION
1 - 2
1.1 Profile mode specification list
Only the specifications of the profile mode are listed here. For other specifications, refer to section 1.3 of
"MR-JE-_C Servo Amplifier Instruction Manual".
Item Description
Servo amplifier model MR-JE-_C
Profile mode
Profile
position mode
Command position range
Set with objects/registers.
Setting range of feed length: -999999 to 999999 [pulse],
Setting range of rotation angle: -360.000 to 360.000 [degree]
Command multiplication Electronic gear A/B multiple, A: 1 to 16777215, B: 1 to 16777215, 1/27649 < A/B < 8484
In-position range setting 0 pulse to ±65535 pulses (command pulse unit)
Error excessive ±3 revolutions
Torque limit Set with parameters or objects/registers.
Profile
velocity mode
Command speed range -21474836.48 r/min to 21474836.47 r/min (Clamped at the permissible speed)
Torque limit Set with parameters or objects/registers (Clamped at the maximum torque).
Profile torque
mode
Command torque range -3276.8% to 3276.7% (Clamped at the maximum torque)
Speed limit Set with parameters or objects/registers (Clamped at the permissible speed).
Homing mode
Manufacturer-specific
Dog type
(Rear end detection,
Z-phase reference)
Deceleration starts at the front end of the proximity dog. After the rear end is passed, the position
specified by the first Z-phase signal, or the position of the first Z-phase signal shifted by the specified
home position shift distance is used as the home position. If the stroke end is detected during home
position return, the direction of movement is reversed.
Count type
(Front end detection,
Z-phase reference)
At the front end of the proximity dog, deceleration starts. After the front end is passed, the position
specified by the first Z-phase signal after the set distance or the position of the Z-phase signal shifted
by the set home position shift distance is set as a home position. If the stroke end is detected during
home position return, the direction of movement is reversed.
Data set type The current position is set as the home position.
Stopper type
(Stopper position
reference)
A workpiece is pressed against a mechanical stopper, and the position where it is stopped is set as
the home position. If the stroke end is detected during home position return, [AL. 90 Home position
return incomplete warning] occurs.
Home position
ignorance
(servo-on position as
home position)
The current position at servo-on is set as a home position. A home position can be set without
switching to the home position return mode (Homing Mode).
Dog type
(Rear end detection,
rear end reference)
Deceleration starts from the front end of the proximity dog. After the rear end is passed, the position
is shifted by the travel distance after proximity dog and the home position shift distance. The position
after the shifts is set as the home position. If the stroke end is detected during home position return,
the direction of movement is reversed.
Count type
(Front end detection,
front end reference)
Deceleration starts from the front end of the proximity dog. The position is shifted by the travel
distance after proximity dog and the home position shift distance. The position after the shifts is set
as the home position. If the stroke end is detected during home position return, the direction of
movement is reversed.
Dog cradle type
A position, which is specified by the first Z-phase signal after the front end of the proximity dog is
detected, is set as the home position. If the stroke end is detected during home position return, the
direction of movement is reversed.
Dog type last Z-phase
reference
After the front end of the proximity dog is detected, the position is shifted away from the proximity dog
in the reverse direction. Then, the position specified by the first Z-phase signal or the position of the
first Z-phase signal shifted by the home position shift distance is used as the home position. If the
stroke end is detected during home position return, the direction of movement is reversed.
Dog type front end
reference
Starting from the front end of the proximity dog, the position is shifted by the travel distance after
proximity dog and the home position shift distance. The position after the shifts is set as the home
position. If the stroke end is detected during home position return, the direction of movement is
reversed.
Dogless Z-phase
reference
The position specified by the first Z-phase signal, or the position of the first Z-phase signal shifted by
the home position shift distance is used as the home position. If the stroke end is detected during
home position return, [AL. 90 Home position return incomplete warning] occurs.
CiA 402 type
Homing on positive
home switch and index
pulse
(method 3)
Same as the dog type last Z-phase reference home position return. Note that if the stroke end is
detected during home position return, [AL. 90 Home position return incomplete warning] occurs.
Homing on positive
home switch and index
pulse
(method 4)
Same as the dog cradle type home position return. Note that if the stroke end is detected during
home position return, [AL. 90 Home position return incomplete warning] occurs.
Homing on negative
home switch and index
pulse
(method 5)
Same as the dog type last Z-phase reference home position return. Note that if the stroke end is
detected during home position return, [AL. 90 Home position return incomplete warning] occurs.