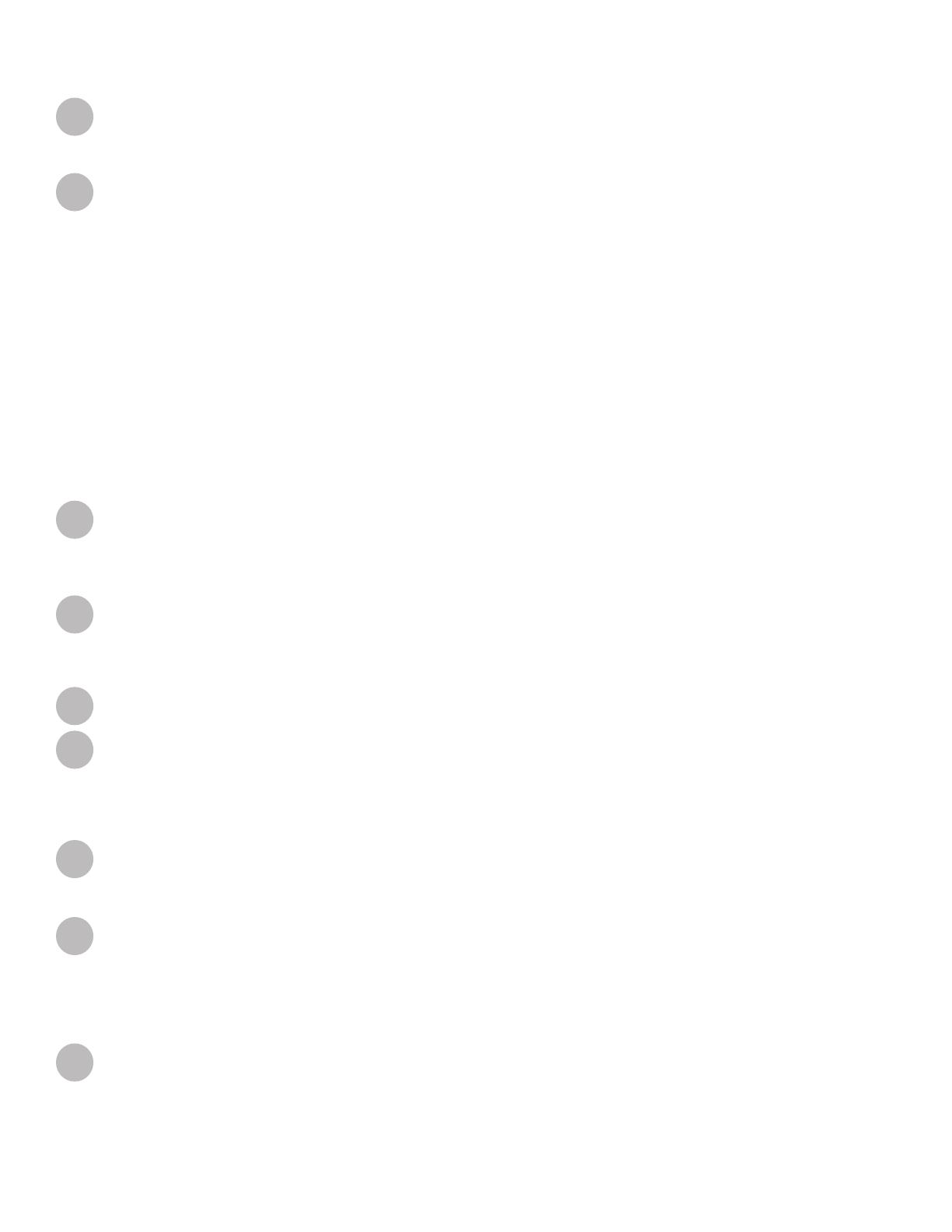
3D Systems, Inc.
1
CONTENTS
HOW TO PREPARE FOR INSTALLATION .................................................................3
Safety Precautions.................................................................................... 3
When You are Ready for Installation ...................................................................... 3
WHAT YOUR SYSTEM INCLUDES .......................................................................4
Required System Components .......................................................................... 4
ProX 500 SLS 3D Printer ............................................................................5
ProX Material Quality Control (MQC) System ............................................................6
Part Transfer Cart .................................................................................9
Chiller ...........................................................................................9
Nitrogen Generator ................................................................................9
Vacuum Cleaner .................................................................................10
Dust Extractor ...................................................................................10
ProX 500 SLS Transformer .........................................................................10
Recommended Optional Equipment ......................................................................11
Room Area Oxygen Monitor. . . . . . . . . . . . . . . . . . . . . . . . . . . . . . . . . . . . . . . . . . . . . . . . . . . . . . . . . . . . . . . . . . . . . . . . . 11
Bead Blaster ....................................................................................11
Consumables ....................................................................................... 12
Nitrogen Consumption .............................................................................12
SLS Materials. . . . . . . . . . . . . . . . . . . . . . . . . . . . . . . . . . . . . . . . . . . . . . . . . . . . . . . . . . . . . . . . . . . . . . . . . . . . . . . . . . . . 12
Replaceable Filters Kit .............................................................................12
Coolant. . . . . . . . . . . . . . . . . . . . . . . . . . . . . . . . . . . . . . . . . . . . . . . . . . . . . . . . . . . . . . . . . . . . . . . . . . . . . . . . . . . . . . . . . 13
FACILITY REQUIREMENTS CHECKLIST .................................................................14
About the Checklist .................................................................................. 14
How to Submit Your Completed Facilities Checklist.......................................................... 14
Facility Requirements Checklist - ProX 500 SLS 3D Printer and Auxiliary Equipment ............................... 15
ROOM REQUIREMENTS ..............................................................................16
Clearance Requirements – ProX 500 Station .............................................................. 16
Clearance Requirements – ProX MQC System............................................................. 16
Floor Requirements . . . . . . . . . . . . . . . . . . . . . . . . . . . . . . . . . . . . . . . . . . . . . . . . . . . . . . . . . . . . . . . . . . . . . . . . . . . . . . . . . . 16
ATMOSPHERE REQUIREMENTS .......................................................................17
ELECTRICAL REQUIREMENTS ........................................................................18
ProX 500 Process Station Power Requirements ............................................................ 18
ProX 500 Transformer Requirements .................................................................... 18
ProX MQC System Power Requirements ................................................................. 18
Grounding Requirements.............................................................................. 19
CHILLER REQUIREMENTS ............................................................................20
Chiller Electrical Requirements ......................................................................... 20
Chiller Coolant Requirements .......................................................................... 20
NITROGEN AND COMPRESSED AIR REQUIREMENTS .....................................................21
Nitrogen Supply Requirements ......................................................................... 21
Nitrogen Supply Options .............................................................................. 21
N
2
Generator O
2
Exhaust ...........................................................................21
Nitrogen Supply and Exhaust Lines...................................................................... 21
Compressed Air Requirements ......................................................................... 21
RECEIVING, MOVING, AND STORING THE SYSTEM .......................................................22
What Your Shipment Includes .......................................................................... 22
Required and Optional System Components. . . . . . . . . . . . . . . . . . . . . . . . . . . . . . . . . . . . . . . . . . . . . . . . . . . . . . . . . . . . 22
SLS Materials and Filters.............................................................................. 23
Shipping Weights and Dimensions ...................................................................... 23
ProX 500 Ship Kit. . . . . . . . . . . . . . . . . . . . . . . . . . . . . . . . . . . . . . . . . . . . . . . . . . . . . . . . . . . . . . . . . . . . . . . . . . . . . . . . . 24
1
2
3
4
5
6
7
8
9