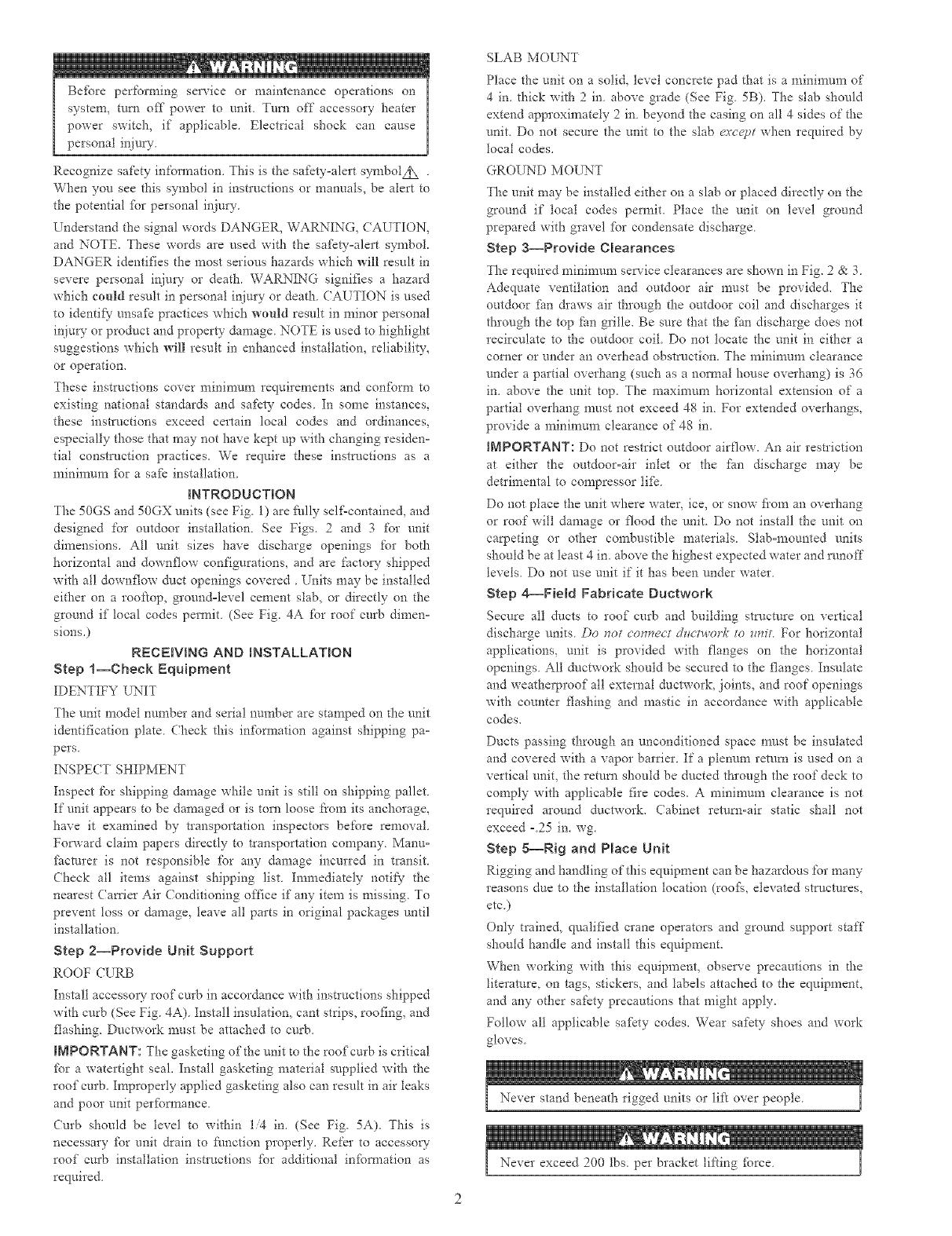
Be%re per%truing service or maintenance operations on
system, mm off power to m_iL Turn off accessory heater
power switch, if applicable. Electrical shock can cause
personal injury.
Recognize safety information. This is the saf?ty-alert symbol_
When you see this symbol in instrucfions or manuals, be alert to
the potential fbr personal injury.
Understand the signal words DANGER, WARNING, CAUTION,
and NOTE. These words are used with the safety-alert symbol.
DANGER identifies the most serious hazards which will result in
severe personal ir!imy or death. WARNING signifies a hazard
which could result in personal injury or death. CAUTION is used
to identify unsafB practices which would result in minor personal
injury or product and property damage. NOTE is used to highlight
suggestions which will result in enhanced installation, reliability_
or operation.
These instrucfions cover minimum requirements and confbrm to
existing national standards and safety codes. In some instances,
these instructions exceed certain local codes and ordinances,
especially those that rnay not have kept up with changing residen-
tial constroction practices. We require these instn/ctions as a
minimum fbr a saf_ installation.
_NTRODUCTION
The 50GS and 50GX units (see Fig. 1) are fully self:contained, and
designed for outdoor installation. See Figs. 2 arid 3 for unit
dimensions. All unit sizes have discharge openings for both
horizontal and downftow configurations, and are factouj shipped
with all downflow duct openings covered. Units may be installed
either on a rooftop, ground-level cement slab, or directly on the
ground if local codes permit. (See Fig. 4A fbr roof curb dinaen=
sions.)
RECEBVING AND INSTALLATION
Step 1--Check Equipment
IDENTIFY UNIT
The unit model number and serial number are stamped on the unit
identification plate. Check this infbrmation against shipping pa=
pers
INSPE( T SHIPMENT
Inspect for shipping damage while unit is still on shipping pallet
If unit appears to be damaged or is torn loose from its anchorage,
have it examined by tlansportation inspectors before removal
Fopxard claim papers directly to transportation company Manu=
facmrer is not responsible for any damage lucre'red in transit
(heck all items against shipping list Immediately notif}- the
nearest Can'ier Air ( onditioning office it"any item is missing. To
prevent toss or damage, 1cave all parts in original packages until
installation
Step 2--Provide Unit Support
ROOF CURB
Install accesso U root" curb in accordance with instructions shipped
with curb (See Fig. 4A) Install insulation, cant strips, roofing, and
flashing. Ductwork must be attached to curb
mMPORTANT: The gasketing of the unit m the roof cm'b is critical
for a watertight seal. Install gaskefing material supplied with the
roof curb. Improperly applied gasketing also can result in air teaks
and poor unit perfbrmance.
Cm'b should be level to within 1/4 in. (See Fig. 5A). This is
necessary fbr unit drain to fhnction properly. Refer to accesso W
roof curb installation instructions fbr additional infbm_ation as
required
SLAB MOUNT
Place the unit on a solid, level concrete pad that is a minimurn of
4 in. thick with 2 in. above grade (See Fig. 5B). The slab should
extend approximately 2 in. beyond the casing on all 4 sides of the
unit. Do not secure the unit to the slab except when required by
local codes.
GROUND MOUNT
The unit may be installed either on a slab or placed directly on the
ground if local codes permit. Place the unit on level ground
prepared with gravel for condensate discharge.
Step a--Provide Clearances
)"he required minimum service clearances are shown in Fig. 2 & 3.
Adequate ventilation and outdoor air must be provided. The
outdoor fhn &aws air through the outdoor coil and discharges it
through the top fan grille. Be sure that the fan discharge does not
recirculate to the outdoor coil. Do not locate the unit in either a
comer or under an overhead obstruction. The rninimum clearance
under a partial overhang (such as a nomaal house overhang) is 36
in. above the unit top. The rnaximum horizontal extension of a
partial overhang must not exceed 48 in. For extended overhangs,
provide a minirnm*n clearance of 48 in.
INPORTANT: Do not restrict outdoor airflow. An air restriction
at either the outdoor=air inlet or the fire discharge may be
detrimental to compressor lift.
Do not place the unit where water, ice, or snow fiom an overhang
or roof will damage or flood the unit. Do riot install the unit on
carpeting or other combustible materials. Stab=mounted units
should be at least 4 in. above the highest expected water and nmoff
levels. Do not use unit if it has been under water.
Step 4-==Field Fabricate Ductwork
Secure a11 ducts to roof curb arid building stnlcmre on vertical
discharge units Do t_nf connecf duct_ork to _mir For horizontal
applications, unit is provided with flanges on the horizontal
openings. All ductwork should be secured to the flanges. Insulate
and weatherproof all external ductwork, joints, and roof openings
with counter flashing and mastic in accordance with applicable
codes.
Ducts passing through an unconditioned space must be insulated
and covered with a vapor barrier. If a plenum remm is used on a
vertical unit, the return should be ducted through the roof deck to
comply with applicable fire codes. A rninimun_ clearance is not
required around ductwork. Cabinet retort>air static shall not
exceed -.25 in. wg.
Step 5--Rig and Pmaee Unit
Rigging and handling of this equipment can be hazardous for many
reasons due to the installation location (roof?_, elevated stn/cmres,
etc.)
Only trained, qualified crane operators and ground support staff
should handle and install this equipment.
When working with this equipment, observe precautions in t!-le
literature, on tags, stickers, and labels attached to the equipment,
and any other safety precautions that might apply.
Follow all applicable safety codes. Wear safety shoes and work
gloves.