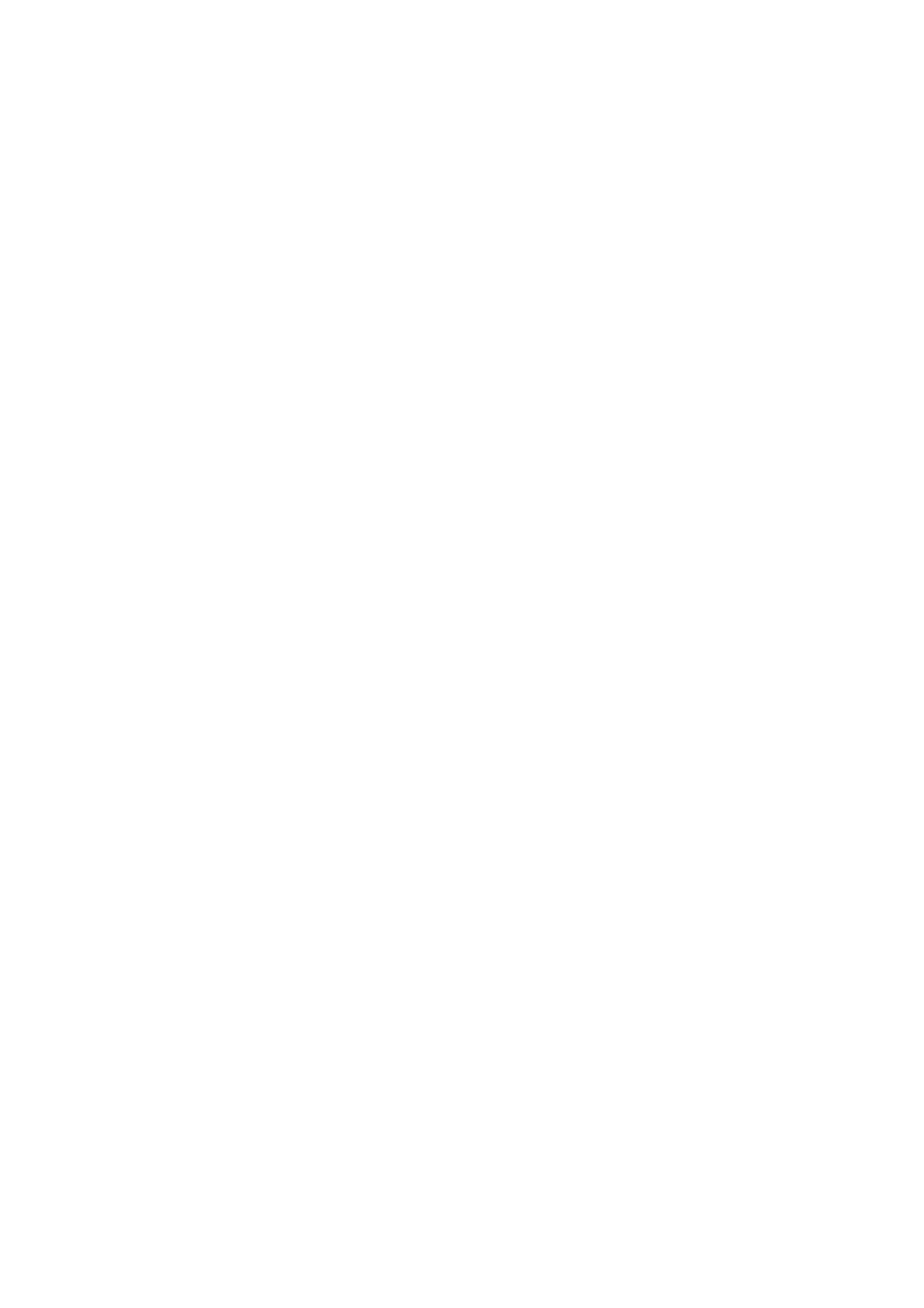
SEGURIDAD 2..........................................
DESCRIPCIÓN TÉCNICA 3...............................
INSTALACIÓN 8.........................................
OPERACION 9..........................................
MANTENIMIENTO 10.....................................
SICUREZZA 12...........................................
DESCRIZIONE TECNICA 13...............................
INSTALLAZIONE 18.......................................
USO 19..................................................
MANUTENZIONE 20......................................
SEGURANÇA 22.........................................
DESCRIÇÃO TÉCNICA 23.................................
INSTALAÇÃO 28..........................................
FUNCIONAMENTO 29....................................
MANUTENÇÃO 30........................................
SAFETY 32..............................................
TECHNICAL DESCRIPTION 33.............................
INSTALLATION 38........................................
OPERATION 39..........................................
MAINTENANCE 40........................................
ΑΣΦΑΛΕΙΑ 42...........................................
ΤΕΧΝΙΚΗ ΠΕΡΙΓΡΑΦΗ 43................................
ΕΓΚΑΤΑΣΤΑΣΗ 49.......................................
ΛΕΙΤΟΥΡΓΙΑ 50.........................................
ΣΥΝΤΗΡΗΣΗ 51.........................................
CROQUIS ACOTADO - DIMENSIONI - ESBOÇO COM DIMENSÕES -
DIMENSION DRAWING - ΕΧΕ∆ΙΑΓΡΑΜΜΑ ΜΕΓΕΘΩΝ ....
52
INSTRUCCIONES DE MONTAJE - ISTRUZIONI PER IL MONTAGGIO -
INSTRUÇÕES DE MONTAGEM -
ASSEMBLY INSTRUCTION - Ο∆ΗΓΙΕΣ ΣΥΝ∆ΕΣΗΣ 55
ESQUEMA - SCHEMA - ESQUEMA -
DIAGRAM - ΣΧΗΜΑ ΣΥΝ∆ΕΣΗΣ 58.................
PIEZAS DE DESGASTE - PAR TI DI USURA -
PEÇAS EXPOSTAS A DESGASTE - WEAR COMPONENTS -
ΑΝΑΛΩΣΙΜΑ ΑΝΤΑΛΛΑΚΤΙΚΑ 70.................
Reservado el derecho de cambiar las especificaciones sin previo aviso.
Specifiche senza preavviso.
Reservamo--nos o direito de alterar as especificações sem aviso prévio.
Rights reserved to alter specifications without notice.
∆ιατηρεßται το δικαß ωmα τροποποßησηj προδιαγραφþνΧωρßj προειδοποßηση.