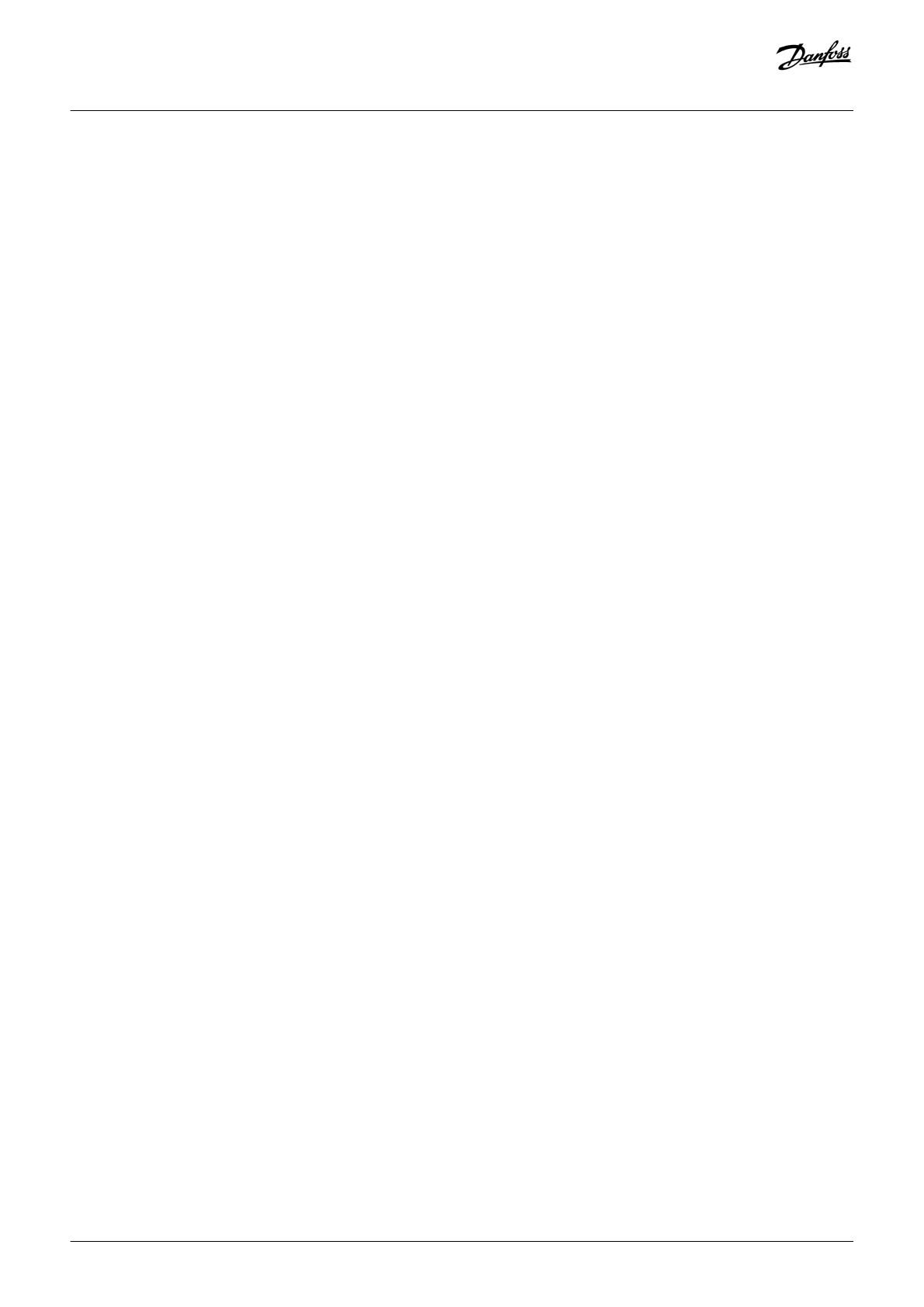
2 Introduction to IMC
2.1 An Overview to IMC
The Integrated Motion Controller (IMC) enables position control with all control principles and motor types with and without feedback
for the VLT.
IMC enables the following functions:
• Positioning
• Synchronization
• Homing
• Virtual Master
Position control in both positioning and synchronization modes can be either sensorless or with feedback.
In the sensorless control principle, the motor angle calculated by the motor controller is used as feedback. In the closed loop control
principle, VLT® AutomationDrive FC 302 supports 24 V encoders as standard. With extra options, the drive supports most standard
incremental and absolute encoders, and resolvers. The position controller can handle both linear and rotary systems. The controller
can scale positions to any relevant physical unit such as mm or °.
To activate IMC, select [9] Positioning or [10] Synchronization in parameter 1-00 Configuration Mode.
2.2 Software version and Control Card
Software version 48.33 and higher can only be installed on control card MK II. The white USB port identifies a control card MK II.
To order VLT® AutomationDrive FC 302 drives with the IMC software, select S067 as Software Release in position 24-27 of the type
code. For more information on ordering the software, see Design Guide.
2.3 Reference Handling
IMC can be used in positioning and synchronization applications without more options.
Positioning
Reference for the target position depends on any of the following positioning types:
• Absolute: Target position relates to the defined zero point of the machine.
• Relative: Target position relates to the actual position of the machine.
• Touch Probe: Target position relates to a signal on a digital input.
Position control can be sensorless or with feedback. For sensorless control, the motor angle calculated by the motor controller is used
as feedback. In closed- loop (with feedback) control principle, 24 V encoders are the standard option. With extra options, incremental
encoders, absolute encoders, and resolvers are supported.
The position controller can handle both linear and rotary systems. Position values are scaled to relevant physical units. All positioning
and synchronization are controlled either by digital I/O or fieldbus.
A positioning command requires 3 inputs:
• Target position
• Speed reference
• Ramp times
Introduction to IMC
Application Guide | VLT® Integrated Motion Controller
AB304441080478en-00101 / 130R0903
8 | Danfoss A/S © 2019.08