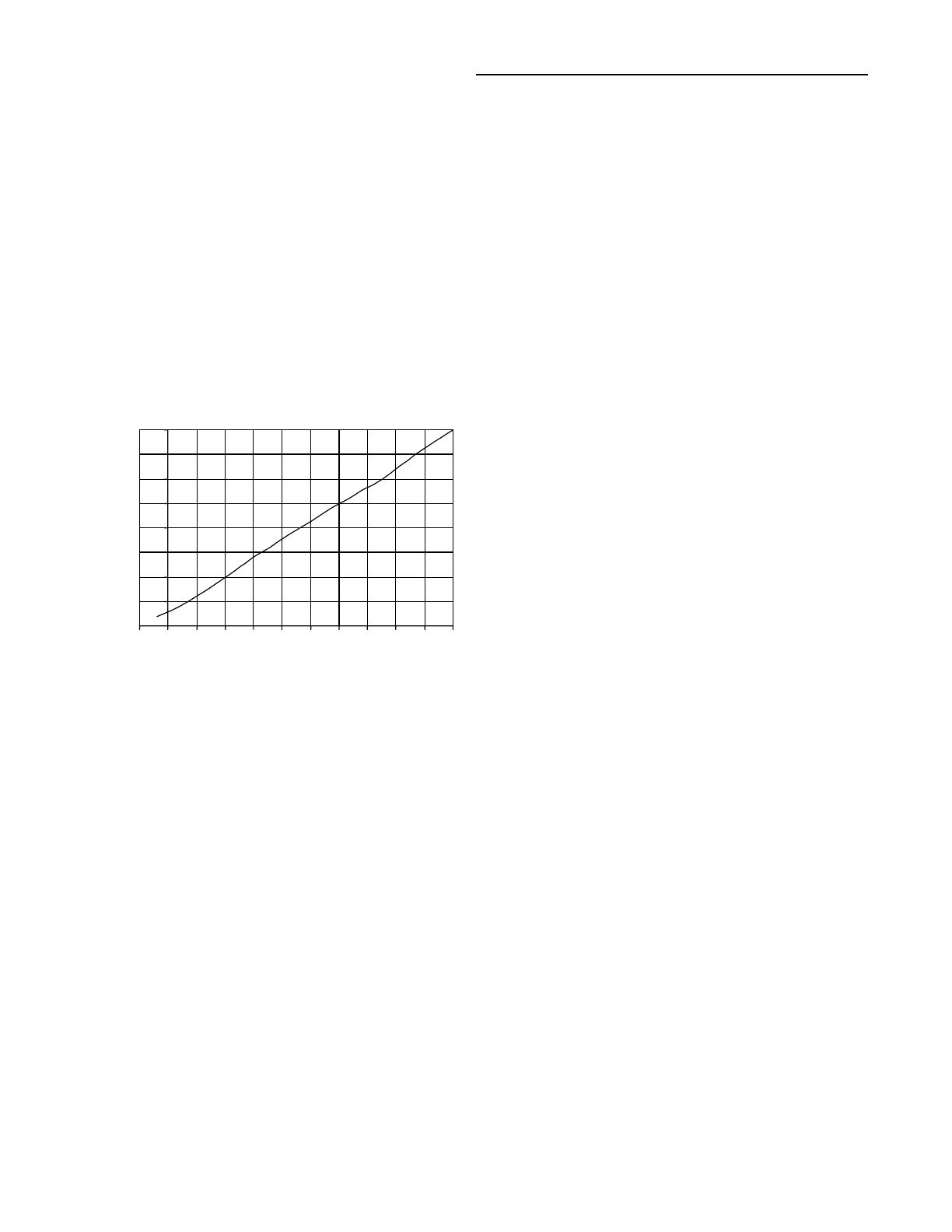
10
General Information (Continued)
Low Ambient Compressor Lockout
Utilizes an analog input device for CV & VAV applications.
When the system is configured for low ambient compressor
lockout, the compressors are not allowed to operate if the
temperature of the outside air falls below the lockout set-
point. When the temperature rises 5 F above the lockout
setpoint, the compressors are allowed to operate. The set-
point for units without the low ambient option is 50 F. For
units with the low ambient option, the setpoint is 0 F. The
setpoints are adjustable at the Human Interface inside the
unit control panel.
Space Pressure Transducer (3U62)
Is an analog input device used on CV & VAV applications
with the Statitrac option. It modulates the exhaust dampers
to keep the space pressure within the building to a cus-
tomer designated controlband. It is mounted in the filter
section just above the exhaust damper actuator and is con-
nected to the ECEM (1U52). Field supplied pneumatic tub-
ing must be connected between the space being controlled
and the transducer assembly.
Transducer Voltage Output vs Pressure Input
0.0
0.5
1.0
1.5
2.0
2.5
3.0
3.5
4.0
-0.5 0.0 0.5 1.0 1.5 2.0 2.5 3.0 3.5 4.0 4.5 5.0
P re ssur e (i nche s w . c. )
Volts
Morning Warm-Up - Zone Heat
When a system changes from an unoccupied to an occu-
pied mode, or switches from STOPPED to AUTO, or power
is applied to a unit with the MWU option, the heater in the
unit or external heat will be brought on if the space tem-
perature is below the MWU setpoint. The heat will remain
on until the temperature reaches the MWU setpoint. If the
unit is VAV, then the VAV box/unocc relay will continue to
stay in the unoccupied position and the VFD/IGV output
will stay at 100% during the MWU mode. When the MWU
setpoint is reached and the heat mode is terminated, then
the VAV box/unocc relay will switch to the occupied mode
and the VFD/IGV output will be controlled by the duct static
pressure. During Full Capacity MWU the economizer
damper is held closed for as long as it takes to reach
setpoint. During Cycling Capacity MWU the economizer
damper is allowed to go to minimum position after one
hour of operation if setpoint has not been reached.
Compressor Motor Winding Thermostats (2B7S1,
2B17S2, 2B27S5, 2B8S3, 2B18S4 & 2B28S6)
A thermostat is embedded in the motor windings of each
Scroll compressor. Each thermostat is designed to open if
the motor windings exceeds approximately 221 F. The ther-
mostat will reset automatically when the winding tempera-
ture decreases to approximately 181 F. Rapid cycling, loss
of charge, abnormally high suction temperatures, or the
compressor running backwards could cause the thermostat
to open. During a request for compressor operation, if the
Compressor Module (SCM) detects a problem outside of
it's normal parameters, it turns any operating
compressor(s) on that circuit "Off", locks out all compressor
operation for that circuit, and initiates a manual reset diag-
nostic.
Supply Air Temperature Low Limit
Uses the supply air temperature sensor input to modulate
the economizer damper to minimum position in the event
the supply air temperature falls below the occupied heating
setpoint temperature.
Freezestat (4S12)
Is a binary input device used on CV & VAV units with Hy-
dronic Heat. It is mounted in the heat section and con-
nected to the Heat Module (1U50). If the temperature of the
air entering the heating coil falls to 40 F, the normally open
contacts on the freezestat closes signalling the Heat Mod-
ule (1U50) and the Rooftop Module (RTM) to:
a. drive the Hydronic Heat Actuator (4U15) to the full
open position.
b. turn the supply fan "Off".
c. closes the outside air damper;
d. turns "On" the SERVICE light at the Remote Panel.
e. initiates a "Freezestat" diagnostic to the Human
Interface.
High Duct Temp Thermostats (Optional 3S16, 3S17)
Are binary input devices used on CV & VAV applications
with a Trane Communication Interface Module (TCI). They
provide "high limit" shutdown of the unit and requires a
manual reset. They are factory set to open if the supply air
temperature reaches 240 F, or the return air temperature
reaches 135 F. Once tripped, the thermostat can be reset
by pressing the button located on the sensor once the air
temperature has decreased approximately 25 F below the
cutout point.
Compressor Circuit Breakers (1CB8, 1CB9, 1CB10,
1CB11 & 1CB14, 1CB15, 1CB16, 1CB17)
The Scroll Compressors are protected by circuit breakers
which interrupt the power supply to the compressors if the
current exceeds the breakers “must trip” value. During a re-
quest for compressor operation, if the Compressor Module
(SCM) detects a problem outside of it's normal parameters,
it turns any operating compressor(s) on that circuit "Off",
locks out all compressor operation for that circuit, and ini-
tiates a manual reset diagnostic.
Constant Volume (CV) Units
Zone Temperature - Cooling
Relies on input from a sensor located directly in the space,
while a system is in the occupied "Cooling" mode. It modu-
lates the economizer (if equipped) and/or stages the me-
chanical cooling "On and Off" as required to maintain the
zone temperature to within the cooling setpoint deadband.
Zone Temperature - Heating
Relies on input from a sensor located directly in the space,
while a system is in the occupied "Heating" mode or an un-
occupied period, to stage the heat "on and off" or to modu-
late the heating valve (hydronic heat only) as required to
maintain the zone temperature to within the heating setpoint
deadband. The supply fan will be requested to operate any
time there is a requested for heat. On gas heat units, the
fan will continue to run for 60 seconds after the furnace is
turned off.
Supply Air Tempering
On CV units equipped with staged heat, if the supply air
temperature falls 10 F below the occupied heating setpoint
temperature while the heater is "Off", the first stage of heat
will be turned "On". The heater is turned "Off" when the sup-
ply air temperature reaches 10 F above the occupied heat-
ing setpoint temperature.